Coût du moulage sous pression : comment calculer le prix des pièces moulées sous pression ?
Temps de publication:2025-02-03 Trier par:Le blog Nombre de vues:740
Dans l'industrie manufacturière, le procédé de moulage sous pression est largement utilisé pour la production de toutes sortes de pièces et de composants, grâce à sa haute précision et à sa grande efficacité de production. Cependant, le calcul du coût du moulage sous pression est souvent une partie importante de l'entreprise pour la fixation des prix et le contrôle des coûts. Une bonne compréhension du coût des composants moulés sous pression permet non seulement de fixer des prix raisonnables, mais aussi d'aider les entreprises à optimiser le processus de production et à améliorer les bénéfices. Dans ce document, nous analyserons le coût du moulage sous pression, fournirons une méthode de calcul des coûts détaillée et discuterons de la manière d'optimiser les coûts afin de réduire le coût global du moulage sous pression.
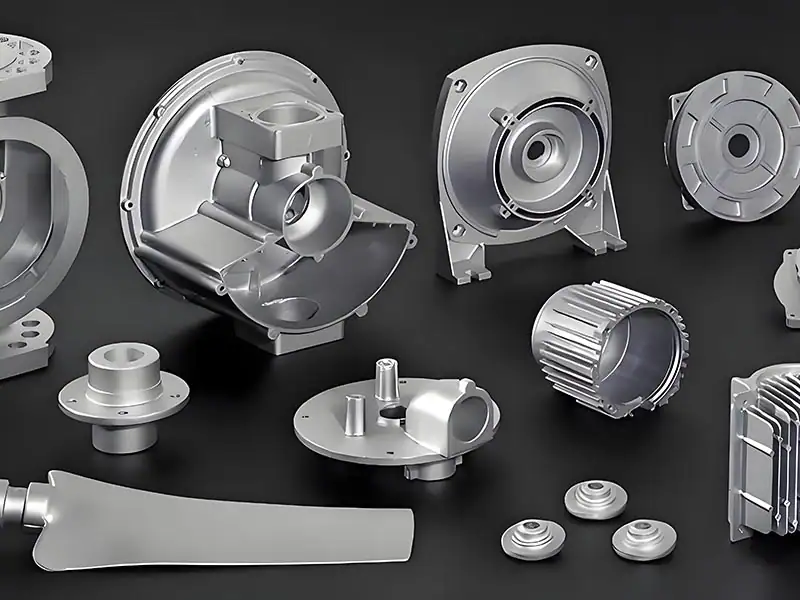
Le moulage sous pression est-il coûteux ?
Le coût du moulage sous pression n'est en effet pas faible, ce qui est la principale raison pour laquelle de nombreuses entreprises hésitent à choisir ce procédé. Bien que le moulage sous pression excelle dans la précision, l'efficacité et la fabrication de pièces complexes, son coût élevé, en particulier pour la production de petits lots, décourage souvent les entreprises. C'est pourquoi Ningbo Hexin suggère aux entreprises d'adopter le procédé de moulage sous pression lorsqu'elles réalisent une production de masse, afin de diluer le coût. Voici quelques facteurs clés qui influencent le coût du moulage sous pression :
Modélisation métrique tridimensionnelle des coûts de moulage sous pression (dans ADC12)aluminium(coquillages à titre d'exemple)
1. le contrôle dynamique des coûts des matériaux
- Formule de base : C_m=(W_p×ρ×P_m×(1+15% perte))/taux de rendement
- Valeurs mesurées des variables clés :
- Volatilité des matériaux : différence de prix de l'aluminium ADC12 entre le pic et la vallée de 4 200 $/t en 2023 (voir figure 1).
- Optimisation des parois minces : l'épaisseur de la paroi d'un embout de moteur électrique a été ramenée de 3,5 mm à 2,8 mm, et le coût des matériaux d'une seule pièce a été réduit de 19%.
- Contrôle du matériau secondaire : le matériau secondaire 30% est ajouté lorsque les propriétés mécaniques du 12% diminuent, ce qui nécessite d'équilibrer la fenêtre de traitement.
2. la gestion du cycle complet des coûts des moules
Type de moule | Coût initial (millions de dollars) | Durée de vie (modules) | Évaluation individuelle ($) |
---|---|---|---|
Cavité simple H13 | 48 | 80,000 | 0.60 |
SKD61 à quatre cavités | 126 | 150,000 | 0.21 |
Source des données : Ningbo Hexin 2022 Mould Database |
3) Déconstruction des éléments du coût de fabrication
- Structure des coûts d'une unité de moulage sous pression de 2800 tonnes :
- Amortissement de l'équipement : 23 $/heure (amortissement linéaire sur 5 ans)
- Coût de la consommation d'énergie : 18kW-h/module x 1,2 = 21,6
- Coût de la main-d'œuvre : 0,38 personne/équipe x 45 $/heure = 17,1
- Consommation de matières auxiliaires : agent de pulvérisation 2,3 yuans / fois le moule
Six voies technologiques d'ingénierie pour la réduction des coûts
Voie 1 : Optimisation de l'ingénierie synchronisée avec la DFM
- Cas : Boîtier de filtrage d'une station de base 5G
- Programme original : 8 grandes sections épaisses (épaisseur maximale de la paroi 8 mm)
- Solution optimisée : optimisation de la topologie + voie d'eau de suivi, réduction du poids 23%
- Résultat : réduction du coût des matériaux par pièce de 16,5%, réduction de la durée du cycle de tir de la presse de 18%.
Voie 2 : Mouler un système de conception intelligente
- Modèle d'efficacité économique pour les moules à cavités multiples :
Q_critique = (C_multi-empreinte - C_mono-empreinte)/(S_mono-empreinte - S_multi-empreinte)
Moules économiques à quatre empreintes pour des quantités de commande > 52 000 pièces
Voie 3 : réglage fin des paramètres du processus
- Courbe de vitesse d'injection de pression en fonction de la porosité (Fig. 2) :
- Fenêtre optimale : taux de défaut <2% à 3,8-4,2m/s
- Pour chaque augmentation de 0,5 m/s de la vitesse, le taux d'usure du moule augmente de 37%.
Voie 4 : Systèmes de production intelligents
- Comparaison des effets de la mise en œuvre :
| Les lignes traditionnelles, les lignes intelligentes, les métriques, etc.
|--------------|----------|----------|
| oee | 68% | 89% |
Taux de produit non satisfaisant | 4.2% | 1.8% | 4.2% | 1.8% | 1.8% | 1.8%
Consommation d'énergie unitaire | 3,6kW-h/kg | 2,9kW-h/kg | 2,9kW-h/kg | 2,9kW-h/kg
Voie 5 : Adaptation précise des finitions de surface
- Analyse du gradient de coût :
- Oxydation native : 6-8 $/pièce
- Oxydation par micro-arc : 22-25 $/pièce
- Revêtement PTFE : 35-40 $ par pièce
Note : Calculée sur la base d'une surface de 300 mm x 200 mm.
Piste 6 : innovation collaborative dans la chaîne d'approvisionnement
- Modèle d'approvisionnement direct en aluminium liquide pour la réduction des coûts :
- Modèle traditionnel : achat de lingots d'aluminium + fusion Coût = prix des matières premières + 1200 RMB/tonne
- Modèle d'approvisionnement direct : livraison d'aluminium liquide Coût = prix des matières premières + 480 RMB/tonne
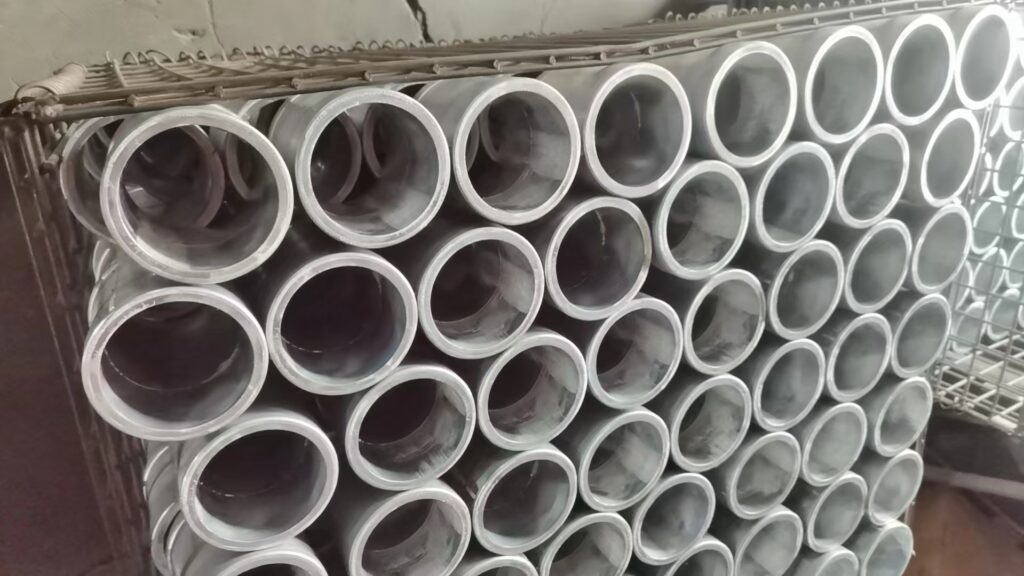
Troisièmement, stratégie d'optimisation des coûts du processus de moulage sous pression
1. optimisation des paramètres du processus
- Adaptation de la vitesse et de la pression d'injection: :
- Un projet de tubage de moteur de véhicule à énergie nouvelle a montré que la vitesse d'injection de la pression était passée de 3,2 m/s à 3,8 m/s, tandis que la pression d'injection était ajustée de 850 bar à 920 bar, et que la porosité était réduite de 2,81 TTP3T à 1,21 TTP3T.
- Optimisation des bénéfices : réduction de 11,5 dollars de la perte de ferraille par unité
- Contrôle de la température du moule: :
- Adopter la technologie de contrôle de la température de partition, réduire la différence de température du moule de ±25℃ à ±8℃.
- Résultat : la durée de vie du moule a augmenté de 30%, le coût par pièce a été réduit de 0,18 RMB.
2. mise à niveau intelligente
- Système de surveillance en temps réel :
- La fluctuation de la courbe d'injection de pression est contrôlée à ±1,5%.
- Précision de l'avertissement de défaut du 92%
- Avantage : réduction des pertes liées aux temps d'arrêt d'environ 230 000 dollars par an.
3. la gestion de la production allégée
Le taux d'erreur humaine est réduit par 67% ruptures. En outre, des conditions de stockage raisonnables permettent d'éviter d'endommager les moules en cas de non-utilisation.
Mise en œuvre du changement rapide de moule (SMED) :
Temps de changement de moule réduit de 45 minutes à 18 minutes
Augmentation annuelle de la capacité de 15%
Opérations standardisées :
Taux de standardisation opérationnelle porté à 95%
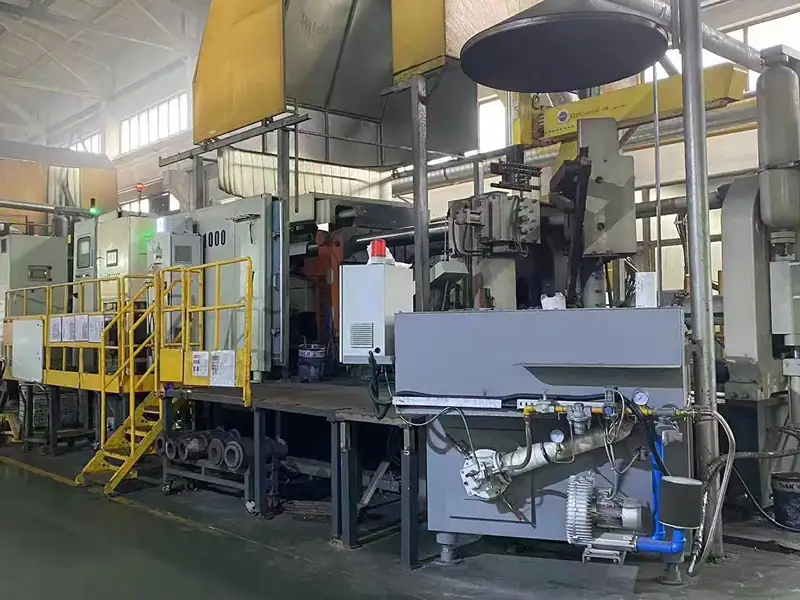
Questions fréquemment posées
Q1 : Comment évaluer l'économie du processus de moulage sous pression ?
- Adoption de l'analyse du seuil de rentabilité :
Q_critique = (coût du moule + part d'équipement)/(prix de vente unitaire - coût variable unitaire)
Exemple : Q_critique = 12 500 pièces pour un projet de gros œuvre, c'est-à-dire économique pour les quantités commandées > 12 500 pièces.
Q2 : Comment réduire les coûts pour les commandes de petites quantités ?
- Programme recommandé :
- Adoption d'un cadre de moule universel + conception de l'insert, réduction du coût du moule 40%
- Augmentation de l'utilisation des matériaux de 25% grâce au choix d'un procédé de formage semi-solide
- Cas : réduction réussie des coûts d'une coque de dispositif médical (500 pièces) 31%
Q3:Comment prolonger la durée de vie des moules ?
- Technologies clés :
- Traitement de surface : le traitement TD peut améliorer la durée de vie des moules de 2 à 3 fois.
- Stratégie de maintenance : nettoyage au plasma tous les 5 000 moules
- Données mesurées : la durée de vie d'un moule H13 est passée de 80 000 à 150 000 cycles de moulage.
Q4:Comment choisir le tonnage optimal de la machine de coulée sous pression ?
- Formule de calcul :
P_Machine à couler = (A_Projection x P_Ratio Pression)/1000
Parmi eux :- A_Projection : Surface projetée de la pièce (cm²)
- P_Pression spécifique : 550-850 bar recommandé pour les alliages d'aluminium.
- Facteur de sécurité : 1,2-1,5
Q5 : Comment réduire le coût du traitement de surface ?
Stratégie de classement : Scénario d'application Processus recommandé Gamme de coûts ($/pc) Pièces d'apparence courantesablage+Anodisation8-12Pièces résistantes à l'usure et à la corrosionOxydation par micro-arc18-25Exigences hautement décorativesElectrophorèse+pulvérisation30-45
HERSHIN : Votre partenaire pour le moulage sous pression
Malgré le coût élevé du moulage sous pression, une optimisation raisonnable et le choix de partenaires professionnels permettent aux entreprises de maîtriser leurs coûts tout en garantissant la qualité. En tant que prestataire de services expérimenté dans le domaine du moulage sous pression, Ningbo Hersin s'engage à fournir à ses clients des solutions efficaces et économiques.
Grâce à notre équipe d'ingénieurs professionnels, nous sommes en mesure de fournir des services de conception et de fabrication de moules personnalisés en fonction des besoins de nos clients. En outre, nous proposons une large gamme d'options de matériaux et de solutions de traitement de surface afin de garantir que vos produits présentent le meilleur équilibre entre la qualité et le coût.
En tant qu'entreprise certifiée ISO 9001:2015, nous disposons d'équipements de production avancés et d'un système de contrôle de qualité strict. En choisissant Ningbo Hexin, vous pouvez non seulement bénéficier de réductions de coûts allant jusqu'à 30%, mais aussi d'un délai de livraison rapide. Il vous suffit de télécharger vos fichiers de conception sur notre plateforme en ligne pour obtenir un devis et une analyse de faisabilité (DfM) dans les 12 heures.
problèmes courants
Q1 : Le moulage sous pression est-il adapté à la production de petits lots ?
Le moulage sous pression est plus adapté à la production de masse en raison de son coût initial plus élevé (par exemple, la fabrication du moule). Pour la production à petite échelle, il est recommandé d'envisager d'autres procédés tels queusinageOu l'impression 3D.
Q2 : Comment choisir le bon matériau de moulage ?
Le choix du matériau du moule doit être basé sur l'échelle de production, la complexité de la pièce et les propriétés du matériau. Pour les gros volumes de production, il est recommandé de choisir des matériaux à haute résistance et résistants à l'usure afin de prolonger la durée de vie du moule.
Q3 : Dans quelle mesure la production automatisée peut-elle réduire les coûts ?
L'automatisation de la production peut réduire considérablement les coûts de main-d'œuvre tout en augmentant la productivité et l'homogénéité des produits. Les économies exactes dépendent de l'échelle de production et du degré d'automatisation.
Q4 : Un traitement de surface est-il nécessaire ?
Le traitement de surface peut améliorer l'apparence et la durabilité des produits, mais toutes les pièces n'en ont pas besoin. Les entreprises doivent choisir le bon traitement de surface en fonction des besoins réels de leurs produits afin d'éviter les coûts inutiles.
Pratiques de développement de systèmes d'aide à la décision en matière de coûts
Ningbo Hexin a développé une plateforme de cotation intelligente basée sur le système ISO 9001 :
- Réponse rapide en 24 heures : télécharger le modèle 3D → obtenir un rapport DFM + un tableau de ventilation des coûts
- Prise en charge des bases de données dynamiques :
- Accès aux cours des métaux en temps réel de Shanghai Nonferrous
- Intégration de plus de 2800 ensembles de données historiques sur les coûts des moules
- Précision de la prédiction des coûts : ±5% (échantillon de validation N=137)
La sélection des procédés du point de vue de l'économie de l'ingénierie
Taille de la commande (pièces) | Procédures recommandées | Gamme d'avantages en termes de coûts |
---|---|---|
<500 | Usinage CNC | Faible 28%-45% |
500-3000 | Coulée semi-solide | Faible 12%-25% |
>3000 | Moulage sous pression | optimal en termes de coûts |
remarques finales
Le contrôle des coûts de moulage sous pression est un projet systématique tout au long du cycle de vie du produit. Grâce à la méthode d'analyse originale de la "carte tridimensionnelle des coûts", Ningbo Hexin a aidé avec succès 37 entreprises à réaliser une réduction moyenne des coûts globaux de 22,6%.