Outillage rapide : des solutions innovantes pour accélérer le développement et la fabrication des produits
Temps de publication:2025-02-14 Trier par:Le blog Nombre de vues:561
À l'ère des changements technologiques rapides, l'industrie manufacturière subit une profonde transformation, passant de la "priorité à l'échelle" à "l'agilité et l'efficacité". L'outillage rapide (Rapid Avant-propos : dilemme et avancées de la Chine en matière de fabrication de moules
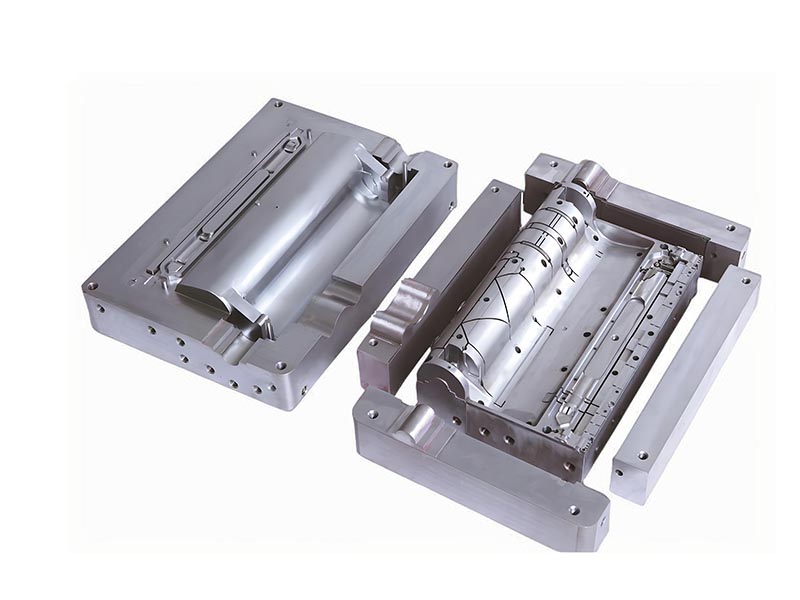
En tant qu'ingénieur profondément engagé dans l'industrie de la fonderie depuis 23 ans, je (He Xin) ai été témoin de la métamorphose de la Chine, qui est passée du statut de grand importateur de moules à celui d'innovateur indépendant. À Ningbo, lieu de rassemblement de l'industrie du moule, nous avons connu le long cycle traditionnel de développement des moules en acier, le coût élevé des essais et des erreurs, mais aussi la percée révolutionnaire apportée par la technologie des moules rapides. Le présent document combine le moulage à haute pression, coulée à basse pression et d'autres scénarios d'application pratique, révélant le rôle de l'outillage rapide dans le processus de production. aluminium Logique technique critique dans la fabrication de composants.
1) L'essence des moules rapides : pas de compromis, mais une correspondance précise
1.1 Les trois principaux points faibles des moules traditionnels
- temps coûtLe développement d'un moule de coulée à haute pression peut prendre jusqu'à 8 à 12 semaines.
- pression financièreLe moule du carter de moteur automobile coûte plus de 2 millions de dollars
- Risque d'essais et d'erreurs: : coulée gravitationnelle Une modification structurelle du moule coûte 150 000 dollars supplémentaires.
1.2 Orientation technique de l'outillage rapide
Réalisé grâce à une triple innovation en matière de science des matériaux, de traitement et de technologie de simulation :
- Cycle Compression 70%Délai de livraison : 7 jours ouvrables minimum entre la conception et le moulage d'essai.
- Réduction des coûts 50%-80%Le coût des moules en aluminium peut être contrôlé entre 80 000 et 150 000 dollars.
- Correspondance précise des quantités d'essai de productionPermet de répondre aux besoins d'une usine pilote de 500 à 30 000 pièces.
2、Solutions de moules rapides pour quatre grands procédés de moulage
2.1 Scénario de la coulée sous haute pression (HPDC)
Le moulage à haute pression est un processus dans lequel la soupe d'alliage d'aluminium fondue à 680-720°C est pressée dans la cavité du moule à une vitesse de 10-50m/s sous une force de serrage de 1600-2000T, et le défi principal est que le moule doit résister à des charges thermo-mécaniques extrêmes. L'innovation de l'outillage rapide dans ce scénario se reflète dans la double optimisation du matériau et de la structure : l'acier QRO90 pour le travail à chaud est utilisé pour remplacer l'acier H13 traditionnel, dont la composition d'alliage molybdène-vanadium augmente la résistance à la fatigue thermique de 40%, et avec le traitement de nitruration de la surface (profondeur de couche de 0,2-0,3 mm), il peut prolonger la durée de vie de l'outillage jusqu'à plus de 30 000 cycles de moulage. Conception structurelle du système d'inserts modulaires, pour les zones vulnérables (telles que les portes, la position de la goupille d'éjection) pour le renforcement local, une entreprise de Ningbo, la production de couvercles d'extrémité de moteurs à énergie nouvelle, grâce au remplacement rapide des inserts pour réduire le temps de maintenance du moule de 8 heures à 1,5 heure. En termes d'économie, le coût par pièce est réduit de 18,6 ¥ à 7,3 ¥ pour les moules traditionnels, et le cycle de développement est réduit à 12 jours, ce qui est particulièrement adapté aux projets de pièces structurelles automobiles dont la production annuelle est inférieure à 50 000 pièces.
Difficultés techniques: :
- Le moule doit résister à une force de serrage de 1600T
- Les alliages d'aluminium fondent à des températures allant jusqu'à 700°C.
- Durée de vie du module >50 000 cycles
Solutions d'outillage rapide: :
- Amélioration des matériauxRemplacement de l'acier conventionnel H13 par l'acier pour travail à chaud QRO90
- Optimisation structurelleLes inserts sont utilisés dans le noyau pour renforcer localement les zones critiques.
- données en temps réelBoîtier de dissipation thermique pour station de base 5G avec une durée de vie de 32 000 cycles de moulage à Ningbo, en Chine.
2.2 Scénarios de coulée à basse pression (LPDC)
La coulée à basse pression injecte l'aluminium liquide en douceur dans la cavité du moule grâce à une pression d'air de 0,5 à 0,8 MPa, ce qui convient particulièrement à la production de pièces à parois minces nécessitant des densités élevées. La percée du moule rapide dans ce domaine se concentre sur le contrôle de la température et l'optimisation du système de coulée : le développement d'un système de contrôle de la température du moule multizone (précision de ±2℃) avec une conception de canal de refroidissement à gradient, de sorte que le rendement du plateau de batterie de nouvelle énergie produit par une entreprise de Ningbo a augmenté de 81% à 95%. Le système de coulée conçu par la technologie d'optimisation topologique a raccourci le temps de remplissage de 9,2 secondes à 6,8 secondes, et a augmenté le taux d'utilisation du métal de 12%. La solution d'outillage rapide adopte des inserts en acier prétrempé P20 + alliage de cuivre local, ce qui réduit le coût de l'outillage à 45% par rapport à la solution traditionnelle. Elle est particulièrement adaptée aux essais pilotes de pièces structurelles complexes telles que les boîtiers hydrauliques aérospatiaux, avec un délai d'exécution typique de 15-20 jours, et prend en charge la production de petits lots de 3 000 à 8 000 pièces.
avancée technologique: :
- Développement d'un système spécial de contrôle de la température des moules (précision de ±2℃)
- Conception d'un canal de refroidissement à gradient
- cas (droit)Dans le cadre d'un projet de construction de véhicules à énergie nouvelle, le rendement du produit est passé de 781 à 931 TTP3T.
2.3 Scénario de coulée par gravité
La coulée par gravité repose sur le remplissage par le poids propre du métal liquide et est couramment utilisée dans la production de pièces complexes et de grande taille. Rapid Mould a réalisé trois innovations majeures dans ce domaine : premièrement, l'impression 3D d'un moule en sable et la technologie composite d'un moule en métal, grâce au processus SLS pour produire un noyau en sable (niveau de précision CT8) combiné à un moule extérieur en acier, de sorte que le cycle de production du bloc-cylindres du moteur est passé de 45 jours à 12 jours ; deuxièmement, le système de contrôle de l'équilibre thermique, incorporé dans les zones clés du moule avec des inserts en alliage de cuivre (conductivité thermique de 380W/m-K), de sorte qu'une culasse de moteur diesel marin de l'usine de fabrication du bloc-cylindres de l'usine de fabrication du bloc-cylindres de l'usine de fabrication du bloc-cylindres a été réduite de 40%. Le gradient de température a été réduit de 40% ; troisièmement, la conception intelligente de l'échappement, qui utilise des bouchons d'évent en métal poreux au lieu des fentes d'échappement traditionnelles, a permis de réduire le taux de défauts de porosité du moulage de 15% à moins de 3%. Les données économiques montrent que le nombre de moules d'essai du programme de moulage rapide est réduit de 2,3 fois en moyenne, et que le coût d'un seul moule d'essai est réduit de 12 à 18 000 yuans, ce qui est particulièrement adapté au développement de composants d'engins de construction à grande échelle dont le poids d'une seule pièce est supérieur à 50 kg.
Pratiques innovantes: :
- Technologie de combinaison de sable d'impression 3D et de moule métallique
- Incrustation localisée d'un alliage de cuivre pour améliorer l'équilibre thermique
- avantage économiqueRéduction de 40% du nombre d'essais de moules et de 65% du temps de cycle grâce à l'optimisation du système de coulée.
3、Cinq technologies de base pour le moulage rapide
3.1 Matrice de sélection des matériaux
scénario d'application | matériel de recommandation | Dureté (HRC) | Conductivité thermique (W/m-K) | indice de coût |
---|---|---|---|---|
coulée à haute pression | H11+ nitruration de surface | 48-52 | 24.3 | ★★★★ |
Alliages d'aluminium en petites quantités | Aluminium aérospatial 7075 | 35-40 | 130 | ★★★ |
Pièces structurelles de haute précision | Acier à outils S7 | 54-56 | 29.4 | ★★★★☆ |
3.2 Comparaison des procédés de traitement de surface
- oxydation par micro-arcFormation d'une couche de céramique de 10-30μm, résistance à la température >800°C
- Revêtement DLCLe coefficient de frottement a été ramené à 0,1, ce qui a permis de multiplier par 3 la durée de vie des moules.
- exemple concretLe projet d'un moule d'enveloppe de turbocompresseur est traité avec un revêtement composite, et la durée de vie du moule dépasse les 80 000 fois.
3.3 Modèle de prévision de la durée de vie
Basé sur des données de simulation Moldflow avec suivi sur le terrain :
L=K× (σappliedσUTS)m×Nthermal
Parmi eux :
- KConstantes du matériau (0,8-1,2 pour les alliages d'aluminium)
- mIndice de fatigue (6,5 pour les moules en acier, 4,2 pour les moules en aluminium)
- Exemples d'applicationsErreur de prédiction à ±8%
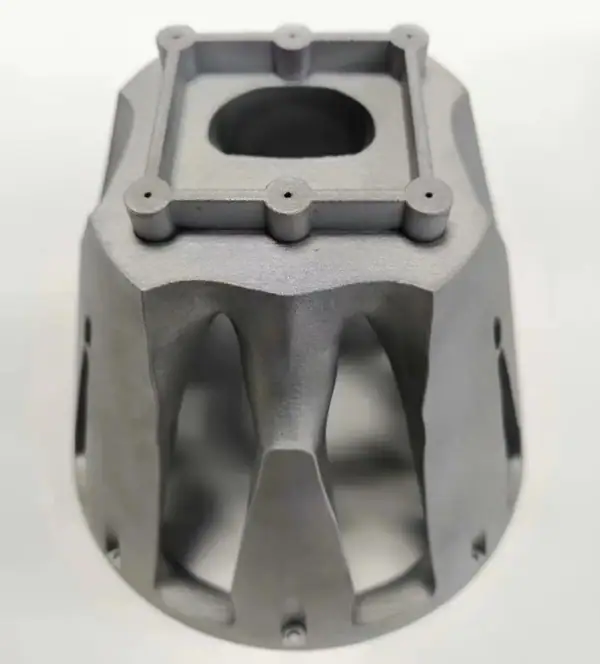
Impression 3D Prototypage rapide
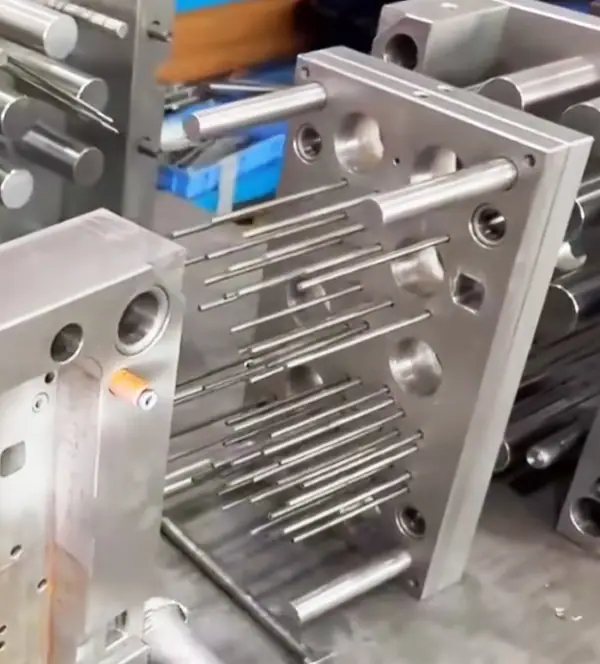
Outillage rapide
4、L'intégration de l'impression 3D et de l'innovation rapide en matière de moules
Le canal d'eau de refroidissement conforme est l'avantage principal des moules d'impression 3D : moules fabriqués par la technologie SLM, l'espacement entre le canal de refroidissement et le contour du produit peut être contrôlé à 1,5-2mm (processus de forage traditionnel ≥ 8mm), de sorte que le cycle d'injection d'une calandre automobile est raccourci de 48 secondes à 32 secondes, et la quantité de déformation est réduite de 0,8mm à 0,3mm.La technologie d'impression de matériaux en gradient peut réaliser la combinaison de la dureté élevée de HRC55 sur la surface du noyau et de la ténacité élevée de HRC35 dans le noyau. L'analyse économique montre que pour les moules complexes comportant plus de 5 formes de voies d'eau, le coût total de la solution d'impression 3D peut être réduit de 42% par rapport à la CNC, ce qui est particulièrement adapté aux scénarios de précision tels que les moules de puces microfluidiques médicales. Les limites techniques actuelles résident dans la taille maximale de moulage (la plupart des dispositifs ≤ 500 mm) et les exigences de post-traitement (les surfaces d'accouplement clés nécessitent encore une finition CNC), mais avec le développement de la technologie multi-laser, on s'attend à ce que l'impression globale de moules à l'échelle du mètre puisse être réalisée en 2025.
4.1 Points de rupture technologique
- Canaux de refroidissement conformesRéduire la durée du cycle d'injection de 23% et la déformation de 40%.
- Impression de matériaux en dégradéDureté de la surface du noyau HRC55, ténacité interne HRC35
- Données de casAmélioration de l'efficacité de refroidissement du moule d'un abat-jour à LED de 37%
4.2 Analyse économique
norme | Moules CNC conventionnels | Moules imprimés en 3D |
---|---|---|
cycle de développement | 18 jours | 6 jours |
Coûts structurels complexes | 100% | 65% |
Coûts de modification | 30% | 8% |
5. trois recommandations pratiques pour les entreprises manufacturières
- Mise en place d'un système de classement des moules: :
- Moules de classe A (>100 000 moules) : moules en acier conventionnels
- Moules de classe B (10 000-50 000 moules) : Moules en acier rapide
- Moules de classe C (<10 000 moules) : impression 3D/moules en aluminium
- Mise en œuvre des jumeaux numériques: :
- Introduction du système de simulation MAGMA au stade de la conception du moule
- Installation de capteurs IoT pour surveiller la distribution des contraintes pendant la phase de production
- Mise en place d'un mécanisme de réaction rapide: :
- Bibliothèque de réserve de moulures standardisées (couvrant la spécification commune 80%)
- Mise en place de réseaux régionaux de collaboration (Ningbo a formé un cercle de chaîne d'approvisionnement de 2 heures)
Conclusion : les dix prochaines années de l'industrie du moule
À partir du projet de plateforme cloud de Ningbo Mould que nous mettons en œuvre, le moule rapide se transforme en un produit intelligent et orienté vers les services :
- Système de cotation intelligent5 minutes pour générer une solution de moule en entrant des paramètres
- traçabilité blockchainTraçabilité de la qualité sur l'ensemble du cycle de vie
- Bibliothèque de moules partagéeRéduction des coûts d'inventaire des PME 30%
Outillage rapideFoire aux questions (FAQ)
Q1 : L'outillage rapide peut-il être utilisé pour la production de masse ?
R : Une évaluation basée sur un scénario est nécessaire :
- Moule en alliage d'aluminium : convient pour les petites séries <5000 pièces
- Moules en acier pré-durci : capacité de 30 000 à 50 000 pièces
- Il est recommandé d'intégrer un système de surveillance numérique pour évaluer l'état des moules en temps réel.
Q2:Comment contrôler la précision dimensionnelle de l'outillage rapide ?
A : Programme recommandé :
- Phase d'usinage : à l'aide de machines-outils à 5 axes + mesure en ligne (précision ±0,02mm)
- Phase d'essai du moule : inspection complète des dimensions clés à l'aide d'une machine à mesurer tridimensionnelle (MMT).
- Phase de production de masse : échantillonnage et test tous les 500 moules
Q3 : Quelles sont les technologies innovantes pour le traitement de surface de l'outillage rapide ?
R : Trois technologies de pointe :
- Revêtement laser : réparation des zones d'usure à un coût réduit 40%
- Revêtement nanocomposite : coefficient de frottement réduit à 0,08
- Nitruration au plasma : dureté de surface jusqu'à HV1200
Q4 : Quelles sont les limites des moules imprimés en 3D ?
A : Principales limitations actuelles :
Exigences en matière de post-traitement : la finition CNC des surfaces d'accouplement critiques est souvent nécessaire.
Taille maximale : la plupart des dispositifs sont limités à 500 x 500 x 500 mm.
Sélection des matériaux : actuellement, les principaux matériaux utilisés sont l'acier moulé, l'alliage d'aluminium et l'acier inoxydable.