Conception de moules pour le moulage sous pression de l'aluminium : un guide pratique du processus à l'optimisation
Temps de publication:2025-02-15 Trier par:Le blog Nombre de vues:746
En tant qu'ingénieur principal de Ningbo Hexin, profondément engagé dans l'industrie du moulage depuis plus de 20 ans, je suis bien conscient de l'importance de l'aluminium. moule de coulée sous pression La position centrale dans l'industrie manufacturière. Qu'il s'agisse de pièces automobiles, de produits électroniques 3C ou de composants aérospatiaux, le processus de moulage sous pression de l'aluminium de haute efficacité et de précision est inséparable de la conception du moule du support subtil. Cet article sera combiné avec l'expérience pratique, l'analyse systématique des points de conception du moule de moulage sous pression de l'aluminium, les tendances technologiques et la stratégie d'optimisation, pour que les collègues de l'industrie puissent fournir un guide pratique.
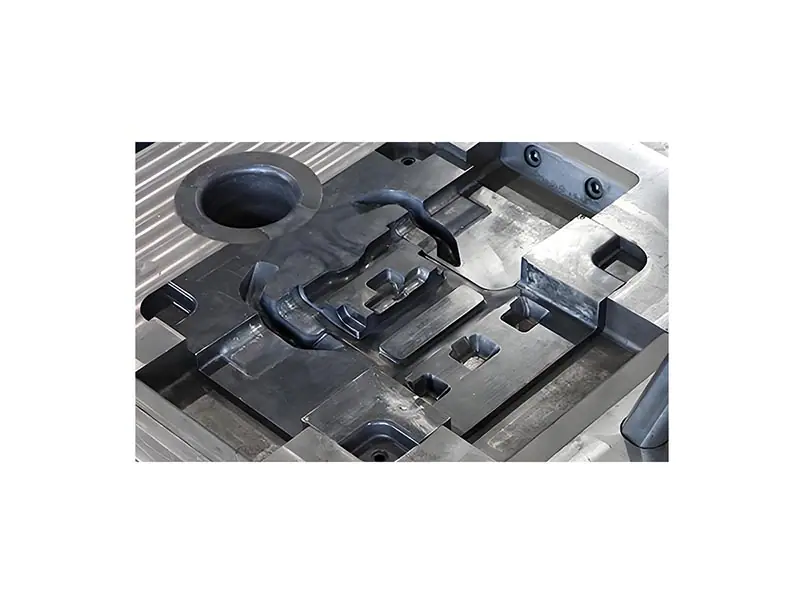
La valeur fondamentale d'une filière de moulage sous pression d'aluminium : pourquoi elle est la clé du succès ou de l'échec du processus
Le moule de coulée sous pression n'est pas seulement le "modèle" de la formation des métaux, mais aussi l'efficacité de la production et la qualité des produits.facteur déterminantL'importance du programme est triple. Cette importance se reflète dans trois domaines :
- Précision exacte
La conception de la cavité du moule détermine directement la tolérance dimensionnelle (généralement ±0,1 mm) et l'état de surface (Ra 1,6~3,2μm) de la pièce moulée. Par exemple, dans le moulage sous pression de blocs moteurs automobiles, la conception du système de refroidissement du moule, si elle n'est pas raisonnable, entraînera une contraction locale inégale, déclenchant une porosité ou une déformation. - Efficacité élevée de la production
Un ensemble de moules multi-cavités optimisés peut augmenter l'efficacité de la production de plus de 300%. Si l'on prend l'exemple d'un projet de coque de moteur de véhicule à énergie nouvelle, l'adoption d'un moule à 4 cavités a permis de faire passer la production horaire de 15 à 60 pièces, tandis que le taux de rendement est resté stable à plus de 98%. - Avantage en termes de coûts
La durée de vie des moules a un impact direct sur le coût par pièce. En utilisant de l'acier H13 pour le travail à chaud des moules, la durée de vie du moule peut être augmentée de 100 000 à 500 000 moules par un traitement de surface TD (méthode de diffusion thermique), ce qui réduit considérablement le coût de partage.
Les cinq principaux types de moules de coulée sous pression en aluminium et la stratégie de sélection
Type de moule | Scénarios applicables | cycle des coûts | Caractéristiques techniques |
---|---|---|---|
Moule pour prototypes | Validation de petits lots (<500 pièces) | Faible coût/2-3 semaines | Impression 3D +usinageprocessus composite |
Outillage rapide | Production pilote (500-5000 pièces) | Coût moyen/4-6 semaines | Fabrication additive par revêtement laser |
Moule unitaire | Multi-espèces et petits lots | Conception modulaire | Changement rapide des inserts de la cavité |
Moule de production | Volume élevé (>100 000 pièces) | Coût élevé/8-12 semaines | Structure à glissières multiples + système de refroidissement ponctuel |
Moule à découper | Ébavurage et séparation des patins | nécessaire pour | Servomoteur hydraulique + guidage de précision |
Suggestions de sélection: :
- Moulage sous pression(HPDC)La priorité est donnée aux moules de production équipés de systèmes d'aspiration afin de réduire les trous d'air ;
- Pièces complexes à parois minces(L'outillage rapide est recommandé, combiné à des techniques locales de moulage en coquille ;
- Production flexible multi-variétésDes moules unitaires peuvent être utilisés pour réduire le temps de changement à moins de 30 minutes.
Les six règles d'or de la conception des moules pour le moulage sous pression de l'aluminium
- Optimisation des lignes fractales
Le plan de joint doit éviter les surfaces fonctionnelles critiques. Par exemple, le radiateur d'une station de base 5G utilise des surfaces courbes pour produire des bavures sur des surfaces sans contact, ce qui réduit les coûts de post-traitement. - Conception hydrodynamique des systèmes de canaux d'écoulement
adoptionCarotte transversale conique(Entrée 8 mm → Sortie 4 mm), ainsi qu'un angle d'ouverture intérieur de 30°, permettent un remplissage en douceur du liquide d'aluminium et évitent l'oxydation causée par un flux turbulent. - Contrôle du bilan thermique des systèmes de refroidissement
La partie centrale est recouverte d'inserts en cuivre au béryllium (conductivité thermique de 210 W/mK), et le contrôle du gradient de température est assuré par le thermostat du moule (250°C dans la zone de la porte → 180°C à la fin), ce qui réduit le temps de refroidissement de 20%. - Calcul scientifique de l'inclinaison de démoulage
En fonction du retrait de l'alliage (environ 0,6% pour ADC12) et des exigences de surface, l'inclinaison de la paroi extérieure est de 1°~1,5°, passant à 2°~3° pour les pièces à cavité profonde. Par exemple, la structure de la cavité profonde d'une coque de drone utilise une pente de 3°, et la résistance à l'éjection est réduite de 40%. - Disposition précise des réservoirs d'évacuation et de trop-plein
Un réservoir de débordement en escalier (profondeur 0,3 mm→ 0,8 mm) est placé dans la zone de remplissage final, et avec la soupape à vide (vide ≤ 50mbar), la porosité peut être contrôlée en dessous de 0,5%. - Sélection avancée des matériaux de moulage
- Pièces régulières : acier H13 (dureté 48-52 HRC)
- Exigences élevées en matière de résistance à l'usure : acier DIEVAR (avec ajouts de cobalt et de molybdène)
- Scènes résistantes à la corrosion : STAVAX ESR (poli miroir à Ra 0,05μm)
Technologie de pointe dans l'industrie : la numérisation et l'intelligence favorisent l'amélioration des moules
- Itérations de conception fondées sur des simulations d'IA
Avec le logiciel AnyCasting/MAGMA, l'ensemble du processus de simulation du remplissage, de la solidification et de la contrainte peut être achevé en 48 heures, et le risque de rétrécissement peut être prédit à l'avance. Dans le cadre d'un projet de coque de boîte de vitesses, la position de la porte a été optimisée par simulation, ce qui a permis de diviser par trois le nombre d'essais de moulage. - Voies d'eau de refroidissement conformes imprimées en 3D
L'utilisation de la technologie SLM (Selected Zone Laser Melting) pour la fabrication de voies navigables façonnées a permis de contrôler la différence de température du moule à ±5°C, réduisant ainsi considérablement les nœuds thermiques. Après l'application d'un moule pour abat-jour à LED, le temps de cycle a été réduit de 18%. - Système de surveillance des moules basé sur l'internet des objets (IoT)
Des capteurs de température et de pression sont implantés à des endroits clés du moule pour surveiller l'état de la surface de la cavité en temps réel. Lorsqu'une fluctuation anormale de la force de serrage (>5%) est détectée, un avertissement est automatiquement déclenché afin d'éviter les défauts du lot.
Étude de cas : Optimisation du moule du bac à batterie pour un véhicule à énergie nouvelle
défi: :
- Dimensions du produit 1200×800mm, épaisseur moyenne des parois 2,5mm, étanchéité à l'air ≤ 0,5Pa-m³/s requise.
- Le rendement initial n'est que de 65%, les principaux défauts étant la ségrégation à froid et la déformation.
prescription: :
- Trajectoire de remplissage équilibrée avec alimentation tangentielle des doubles portes
- Noyau du moule implanté avec 12 ensembles de tubes de refroidissement pulsés pour un contrôle dynamique de la température
- Système d'éjection avec ressorts à gaz d'azote pour une force de déclenchement équilibrée
axé sur les résultats: :
- Rendement amélioré à 92%
- Réduction du temps de production de 180 à 140 secondes
- Durée de vie du moule supérieure à 300 000 cycles de moulage
Foire aux questions (FAQ)
Q1:Comment évaluer la force technique des fournisseurs de moules ?
- Paramètres clés : valeurs Cpk pour les cas antérieurs (≥1,33), capacité d'analyse CAE, exhaustivité des rapports sur les moules d'essai.
Q2 : Comment choisir le revêtement de surface d'un moule ?
- Conventionnel : revêtement CrN (dureté 2200 HV)
- Très résistant à l'usure : AlCrN (résistance à la température de 900°C)
- Amélioration de la libération : revêtement diamanté DLC
Q3 : Quelles sont les meilleures pratiques en matière d'entretien des moules ?
- Tous les jours : vérifier la lubrification des cosses (utiliser de la graisse haute température NLGI grade 2)
- Tous les 5 000 moules : l'électroérosion répare les fissures mineures
- Tous les 50 000 cycles de moulage : traitement de trempe intégral (550°C x 2h)
remarques finales
La conception d'un moule pour le moulage sous pression de l'aluminium est une combinaison de science et d'art, qui nécessite des calculs techniques rigoureux et s'appuie sur une riche expérience pratique. Avec la pénétration profonde de la technologie numérique, l'industrie du moule entre dans le nouveau paradigme "conception intelligente - fabrication de précision - maintenance prédictive". En tant que praticien, la seule façon de prendre la tête du jeu triangulaire coût, efficacité et qualité est de continuer à embrasser l'innovation.
Pour des solutions de moules sur mesure ou des conseils techniques. Bienvenue au contact Ningbo Hersin Casting Team - Avec 20 ans d'expérience, nous donnons à vos produits une précision et des performances ultimes.