Moulage et usinage : comment choisir ?
Temps de publication:2025-03-19 Trier par:Le blog Nombre de vues:316
En tant que membre de l'équipe technique de Ningbo Hexin Casting, je suis spécialisé dans le moulage à haute pression,coulée à basse pressionetcoulée gravitationnelle Je travaille dans le domaine de l'aluminium et des matériaux en aluminium depuis plus de 20 ans et j'ai dirigé le développement de centaines de projets à l'échelle industrielle. Lorsque des clients me posent la question "Comment choisir entre le moulage et l'usinage", ma réponse est toujours la suivante : "Il n'y a pas d'avantage ou d'inconvénient absolu, mais seulement la combinaison de technologies la plus adaptée à la situation". À partir des principes techniques, de l'expérience pratique et des tendances de l'industrie en trois dimensions, voici une analyse approfondie des principales différences entre les deux technologies et de la logique du choix.
Qu'est-ce que le casting ?
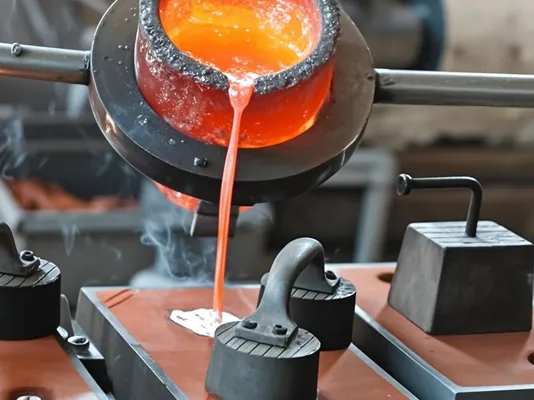
Le moulage consiste à faire fondre le métal, à fabriquer des pièces moulées et à verser le métal fondu dans la pièce moulée, à le solidifier pour obtenir une certaine forme et une certaine performance de la méthode de formage par moulage. Le moulage et d'autres procédés de formage de pièces, comparés au faible coût de production, à la flexibilité du procédé, sont presque indépendants de la taille et de la forme de la structure de la pièce, de la complexité des limitations, etc.
En tant que moteur important de la civilisation humaine, l'histoire de la technologie de la fonte peut être retracée jusqu'à l'Europe ancienne, en 4000 avant J.-C. Des moulages en or mis au jour sur le site de Varna, en Bulgarie, ont révélé les premiers balbutiements de la fonte des métaux. À la même époque, les artisans de Mésopotamie utilisaient déjà des alliages de cuivre pour couler des outils, et les rituels de bronze des dynasties Xia et Shang en Chine ont même démontré la sagesse de la fonte orientale avec la méthode de la coulée en deux parties, qui a permis de dépasser la technologie de la fonte du fer mille ans plus tôt qu'en Europe. Les échanges technologiques entre les civilisations ont favorisé l'itération de l'artisanat : les méthodes égyptiennes de la cire perdue ont façonné des statues exquises, la dynastie chinoise des Song, Tian Gong Kai Wu, a systématiquement documenté le moulage de l'argile, et le monde islamique a intégré le moulage dans la fabrication d'instruments de précision.
La révolution industrielle du XVIIIe siècle a marqué un tournant dans l'histoire du moulage, la méthode de fabrication de la fonte au coke et la combinaison de la machine de moulage sous pression à vapeur, de sorte que les pièces en fonte ont pu être produites à grande échelle, ce qui a permis de soutenir les chemins de fer, les machines textiles et la construction d'autres systèmes industriels. Le moulage moderne s'oriente davantage vers le domaine de la haute technologie, le moulage sous pression d'alliages d'aluminium et de magnésium du 20e siècle a stimulé l'industrie aéronautique, la technologie d'impression 3D sur sable a permis de briser les limites des processus traditionnels. Aujourd'hui, la production annuelle mondiale de pièces moulées dépasse les 100 millions de tonnes, couvrant les secteurs de l'automobile, de l'énergie, de la médecine et d'autres domaines clés. La Chine, l'un des berceaux de la fonderie, est aujourd'hui le leader du secteur avec une production mondiale de 401 tonnes, et grâce à la technologie de fonderie verte et intelligente, elle reste à la pointe de l'innovation. Cette technologie vieille de 8 000 ans est en train de remodeler les fondements de la fabrication moderne avec les concepts de numérisation et de durabilité.
Comment fonctionne le casting ?
Le moulage est une technique industrielle qui consiste à injecter du métal en fusion dans une cavité de moule spécifique et à le laisser refroidir et se solidifier pour obtenir une forme prédéterminée. Le processus de noyautage est divisé en cinq étapes principales : tout d'abord, un moule séparable est conçu en fonction de la structure de la pièce ; le moulage au sable traditionnel utilise du sable de quartz et un liant pour créer une cavité avec un système de coulée, tandis que le moulage à la cire perdue utilise des coquilles en céramique ou des moules en cire ; ensuite, la matière première est fondue dans un four à haute température jusqu'à ce qu'elle atteigne l'état liquide.aluminium Le métal doit être chauffé à plus de 700°C, ou 1400-1500°C pour la fonte, et des éléments d'alliage sont ajoutés pour ajuster les propriétés. La phase de coulée nécessite un contrôle précis du débit et de la température du métal afin d'éviter les défauts de porosité ou de ségrégation à froid, et la technologie moderne de moulage sous vide améliore l'intégrité du moule grâce à des environnements de pression négative.
Le processus de solidification détermine la qualité interne de la pièce moulée, les ingénieurs régulent la direction de la croissance des grains par la conception du système de refroidissement, et les grandes pièces moulées telles que les blocs de moteurs diesel marins utilisent souvent la technologie de solidification séquentielle pour éliminer les trous de retrait. Après le démoulage, le nettoyage au sable, la découpe de la carotte et d'autres traitements, les machines-outils à commande numérique pour l'usinage de précision des pièces clés, les pièces aérospatiales ont également besoin d'une détection des défauts internes par rayons X. Le moulage contemporain a été intégré à l'innovation numérique, la technologie d'impression 3D du sable peut être le moulage direct de canaux d'huile complexes, le logiciel de simulation peut prédire la trajectoire du flux de métal à l'avance, et le moulage vert à travers l'ancien système de régénération du sable pour augmenter le taux d'utilisation des déchets de 95%, mettant en évidence la profondeur de l'intégration de la fabrication intelligente et du développement durable.
Avantages de la coulée
Pour les composants complexesLa conception de moules permet de réaliser des pièces métalliques avec des structures creuses, des surfaces courbes ou des contours irréguliers, ce qui permet de résoudre des problèmes géométriques complexes difficiles à résoudre avec d'autres procédés.
Large compatibilité avec les matériauxLes métaux et les alliages peuvent être traités, y compris les déchets recyclés ou les matières premières de faible pureté, en veillant simplement à ce que la température de fusion soit adaptée à la résistance thermique du moule.
Avantage d'échelle en termes de coûtsAprès un investissement unique dans le moule, un grand nombre de pièces identiques peuvent être produites à l'infini, et le coût par pièce diminue considérablement avec l'augmentation de la taille des lots.
Grande adaptabilité à la tailleLe moulage en sable permet de fabriquer des pièces de grande taille, tandis que les technologies telles que le moulage sous pression conviennent au moulage de pièces de précision de petite et moyenne taille.
Capacité d'intégration de matériaux multiplesLes produits de cette catégorie sont les suivants : le moulage direct de pièces structurelles composites (par exemple, des douilles renforcées) en prépositionnant des inserts métalliques ou non-métalliques dans le moule.
Inconvénients de la coulée
Risque de défauts internesLes fluctuations des paramètres du processus ou les problèmes liés aux matériaux peuvent facilement entraîner des défauts tels que la porosité, le retrait, la ségrégation à froid, etc. qui nécessitent un contrôle strict de la qualité.
Forte dépendance à l'égard de la main-d'œuvreLe processus de moulage traditionnel implique de multiples opérations manuelles telles que la préparation du moule, la coulée et le nettoyage, avec un faible degré d'automatisation.
charge environnementaleLa fusion des métaux libère des gaz et des poussières nocifs, et l'élimination incorrecte des déchets de sable et de scories risque de polluer l'environnement ; il faut donc prévoir des installations de protection de l'environnement.
Qu'est-ce que l'usinage ?
usinage(L'usinage est une technologie de base pour le moulage de précision des métaux, des plastiques et d'autres matériaux par découpage physique, et il est largement utilisé dans des aspects clés de la fabrication moderne. Le processus utilise des équipements tels que des tours, des fraiseuses, des machines-outils à commande numérique, etc., ainsi que des perceuses, des outils de coupe ou des meules, pour éliminer les surépaisseurs avec une précision de l'ordre du millimètre, voire du micromètre, et transformer l'ébauche en une pièce qui répond aux exigences de la conception. Dans le secteur automobile, le trou du vilebrequin du bloc moteur doit être tourné et alésé par de multiples processus pour garantir la concentricité ; le secteur aérospatial s'appuie sur des machines-outils CNC à cinq axes pour découper les surfaces complexes des cadres en alliage de titane, avec des tolérances pouvant être contrôlées à ±0,005 mm. Par rapport au moulage ou à l'impression 3D, l'usinage permet d'obtenir une finition de surface plus élevée, la rectification de précision peut faire en sorte que le chemin de roulement atteigne un effet miroir Ra0,1μm, tout en traitant l'acier trempé et d'autres matériaux super-durs. Cependant, la coupe traditionnelle entraîne une perte de matériau de 30%. Ces dernières années, la technologie d'usinage écologique, grâce à la micro-lubrification et à la coupe à grande vitesse, augmente l'efficacité de 40%, et le système CNC intelligent peut automatiquement optimiser la trajectoire de l'outil afin de réduire la consommation d'énergie et les coûts. Des clous miniatures pour les dispositifs médicaux aux broches pour les éoliennes, l'usinage continue à répondre aux besoins de production industrialisée d'équipements haut de gamme et de dispositifs de précision avec les caractéristiques précises de la "fabrication soustractive".
Avantages de l'usinage
haute précisionLa technologie CNC multi-axes permet d'obtenir une précision de l'ordre du micron, ce qui est particulièrement adapté aux pièces complexes soumises à des exigences dimensionnelles strictes, telles que les pales de turbines et les implants médicaux.
Réponse rapide aux demandes de petits lotsLes machines d'usinage : pas besoin de développer un outillage complexe, l'usinage se fait directement à partir du fichier de conception, ce qui réduit considérablement le temps de cycle pour le prototypage et la production à petite échelle.
Répétabilité stableLa production en série : s'appuyer sur des programmes CNC et des parcours d'outils standardisés pour garantir des dimensions de pièces et une qualité de surface constantes.
production automatiséeLe système CNC automatise l'ensemble du processus, réduit les interventions manuelles, diminue les erreurs de manipulation et améliore l'efficacité du fonctionnement continu de l'équipement.
Large gamme de matériaux adaptablesCompatible avec les métaux, les plastiques techniques, les céramiques et les composites pour répondre aux divers besoins des différentes industries en matière de propriétés des matériaux.
Inconvénients de l'usinage
Traitement structurel interne limitéLes caractéristiques internes complexes telles que les trous profonds et les cavités nécessitent des changements d'outils multiples ou un outillage personnalisé, ce qui rend l'usinage beaucoup plus difficile et coûteux.
Taille limitée par l'équipement: En raison des limites de la course de la machine et de la rigidité de la broche, il est difficile d'obtenir un usinage de précision globale pour les pièces lourdes ou surdimensionnées.
Faible utilisation des ressourcesLe processus de découpe génère de grandes quantités de copeaux ou de poussières métalliques et présente un taux de perte de matière première plus élevé que la fabrication additive ou les processus de forme proche de la forme nette.
Usinage et moulage : types et technologies
Type de traitement
moulinL'utilisation d'un outil rotatif à cannelures multiples permet de couper la pièce à usiner le long de plusieurs axes. Il convient à l'usinage de surfaces planes et incurvées et de structures tridimensionnelles complexes, et est largement utilisé dans la fabrication de cavités de moules et de pièces façonnées.
tournerLa machine est conçue pour l'usinage de pièces rotatives (arbres, disques et douilles) grâce à la rotation de la pièce et à l'avance linéaire de la fraise, ce qui permet l'usinage extérieur, intérieur et fileté.
forageLe foret hélicoïdal est utilisé pour tourner et pénétrer dans le matériau afin de former un trou rond. Il permet de réaliser des trous débouchants, des trous borgnes et des trous en escalier, et est couramment utilisé pour la production par lots de trous de positionnement pour l'assemblage de pièces.
durciMicrocoupage de la surface de la pièce à l'aide d'une meule tournant à grande vitesse afin d'améliorer la précision dimensionnelle et la finition. Convient à l'affûtage des arêtes d'outils et à l'usinage de haute précision des chemins de roulement.
ennuyeuxL'alésage : l'expansion du diamètre intérieur des trous pré-percés par des outils d'alésage à bord unique, en contrôlant précisément la coaxialité et la cylindricité des trous, principalement utilisé pour l'usinage de précision des cavités internes telles que les blocs moteurs et les corps de vannes hydrauliques.
brocheL'utilisation de broches à dents multiétagées pour former des rainures de clavettes, des cannelures ou des alésages façonnés en une seule passe, avec une efficacité élevée et une qualité de surface stable, convient à la production en série d'engrenages et d'accouplements.
érosion du filLe découpage de matériaux conducteurs d'électricité selon le principe de la corrosion galvanique permet le traitement de contours complexes de métaux très durs, et convient particulièrement au poinçonnage de précision de moules et au formage d'aubes de moteurs aérospatiaux.
rabotageLes machines-outils à mouvement alternatif linéaire coupent le plan ou la rainure, conviennent aux grandes machines-outils pour l'usinage du rail de guidage et du plan de la plaque de base, leur fonctionnement est simple mais leur efficacité est faible.
EDMIl permet de traiter les micro-trous, les cavités complexes et les moules en carbure en utilisant la décharge par impulsion pour corroder les matériaux conducteurs, ce qui permet de dépasser les limites de dureté de la découpe traditionnelle.
Chaque procédé est appliqué en combinaison en fonction des caractéristiques de l'outil, de la trajectoire et de l'adéquation du matériau. Ensemble, ils couvrent les besoins de l'ensemble de la chaîne industrielle, de l'ébauche à l'ultrafinition.
Type de moulage
moulage en sableLa fonte : L'utilisation de sable siliceux, d'argile ou d'un liant en résine pour réaliser un moulage unique ou semi-permanent, à travers le modèle de gaufrage pour former la cavité, convient à la fonte, à l'acier moulé et à d'autres productions diversifiées de métaux à point de fusion élevé, couramment utilisés dans la fabrication de blocs moteurs, de soupapes et d'autres composants structuraux.
moulage sous pressionSpécialisé dans la production de masse de pièces de précision à parois minces en métaux non ferreux tels que l'aluminium, le zinc et le magnésium, largement utilisées dans les composants automobiles, les boîtiers électroniques et d'autres produits présentant des exigences élevées en matière d'état de surface, il est en mesure d'offrir des services de qualité à ses clients.
moulage à la cire perdueLe moule en cire est utilisé pour remplacer le modèle solide, enveloppé d'un revêtement réfractaire multicouche pour former une coquille en céramique, et injecté dans le métal liquide après fonte du moule en cire, ce qui permet de reproduire la structure complexe et fine des pales de turbine, des œuvres d'art, etc., et convient particulièrement à la personnalisation en petites quantités de pièces en alliage à haute température dans le domaine de l'aviation et de l'aérospatiale.
coulée centrifugeIl s'agit d'un composant à symétrie de rotation, comme les tubes sans soudure et les moyeux, qui est utilisé dans la production de tuyaux et de bagues de roulement, car la force centrifuge fait adhérer uniformément le métal liquide à la paroi intérieure du moule rotatif, combinant ainsi la densification du matériau et l'efficacité de la production.
coulée à basse pressionLe métal liquide est injecté en douceur dans le moule fermé par pression pneumatique, ce qui réduit les turbulences et l'oxydation et permet de former des pièces creuses telles que des moyeux de roue et des culasses en aluminium, qui nécessitent une grande étanchéité, avec les avantages de la stabilité du processus et de l'utilisation des matériaux.
moulage en coquille (TCM)Le modèle en mousse est utilisé pour remplacer le moule traditionnel, le modèle est gazéifié et rempli de métal liquide pendant la coulée, et peut être intégré pour former des pièces moulées avec des cavités intérieures complexes, ce qui convient à la production de pièces uniques ou de petits lots de machines minières, de boîtiers de pompes et de vannes, etc.
coulée continueLe métal liquide est solidifié en continu et étiré à travers un cristalliseur refroidi à l'eau pour produire directement des barres, des plaques ou des profilés, ce qui améliore considérablement l'efficacité du formage de l'acier, des alliages de cuivre et d'autres matériaux, et devient un processus essentiel pour la production à grande échelle dans l'industrie métallurgique.
Chaque technologie de moulage est adaptée et appliquée en fonction des caractéristiques du moule, de la fluidité du métal et des besoins de production, formant ainsi une gamme complète de capacités de fabrication allant des pièces d'art aux composants industriels.
La principale différence entre l'usinage et le moulage
Caractéristiques de la pièce
L'usinage s'appuie sur des fraises, des forets, des outils de tournage et d'autres outils de coupe pour former directement les pièces, tandis que le moulage doit construire l'espace de formation par la création de modèles, la préparation des moules et d'autres processus préalables, la chaîne d'outils couvrant l'ensemble du processus, de la sculpture du moule en cire à la préparation du sable.
Contrôle de précision
L'usinage permet d'atteindre une précision de l'ordre du micron grâce à des systèmes à commande numérique et est particulièrement efficace pour la finition des surfaces et les détails géométriques complexes ; les pièces moulées sont affectées par la précision du moule, le retrait du métal et d'autres facteurs, et doivent améliorer la cohérence dimensionnelle à l'aide de procédés de moulage sous pression de précision ou de moulage à la cire perdue.
Compatibilité des matériaux
Les matériaux de moulage sont limités par le point de fusion et la fluidité ; le moulage en sable convient à la fonte, à l'acier moulé et à d'autres métaux à point de fusion élevé ; le moulage sous pression se concentre sur l'aluminium, le zinc et d'autres alliages à point de fusion bas ; l'usinage peut traiter des métaux, des plastiques techniques, des céramiques et d'autres matériaux diversifiés, la dureté de la gamme étant plus large.
complexité de la conception
L'usinage permet de mouler des arêtes vives, des structures à parois minces et des trous et rainures de précision, mais il y a un angle mort dans le traitement des cavités profondes, des courbes internes et d'autres structures fermées ; la fonderie peut être moulée en une seule pièce avec des cavités internes, des lignes courbes et des pièces complexes (par exemple, des blocs moteurs), mais la netteté des détails est faible.
Adaptation à l'échelle de production
Le moulage présente un avantage en termes de coûts pour la production de masse, les moules pouvant être rapidement copiés après un investissement unique ; l'usinage sans moules, par le biais du programme, peut être ajusté pour répondre aux besoins de petites quantités ou aux exigences personnalisées d'une seule pièce, ce qui offre une grande flexibilité.
Performance partielle
Les pièces usinées sans défauts de solidification ont des propriétés mécaniques plus uniformes ; les pièces moulées par solidification directionnelle, traitement thermique et autres processus pour optimiser la structure du grain, peuvent être proches de la résistance du matériau brut, mais il peut y avoir des pores microscopiques ou des inclusions.
Efficacité du prototypage
L'usinage est basé sur la coupe directe à partir de modèles CAO et les prototypes sont réalisés en quelques heures ; les prototypes de moulage sont soumis à des délais plus longs en raison de la mise au point du moule et de la coulée du métal, mais le moulage à la cire perdue peut accélérer le processus grâce à l'impression en 3D de modèles en cire.
Structure de coûts intégrée
Le coût du moule est élevé au début de la phase de moulage, ce qui convient à la mise à l'échelle pour diluer le coût d'une seule pièce ; l'usinage n'a pas de coût de moule, le coût de la perte de matière et des heures de travail augmente linéairement avec le volume du lot, ce qui convient mieux aux petites et moyennes échelles ou aux produits à forte valeur ajoutée.
Les deux types de processus se complètent dans la fabrication : le moulage concerne la formation par lots de composants complexes et l'usinage permet la correction finale des caractéristiques de précision ; ensemble, ils soutiennent la chaîne de fabrication complète, de l'ébauche au produit fini.
Où sont utilisés le moulage et l'usinage ?
Classification de l'industrie | Applications typiques de la coulée | Applications typiques pour l'usinage |
---|---|---|
la construction automobile | Blocs moteurs, carters de boîtes de vitesses, moyeux de roues, supports de suspension | Engrenages de transmission, segments de piston, tourillons de vilebrequin, étriers de frein |
aérospatiale | Enveloppes de turbines, aubes de moteurs, composants structurels de trains d'atterrissage | Cadres en titane, tuyères de carburant, pièces de précision des commandes de vol |
matériel médical | Sommiers médicaux, boîtiers d'appareils d'imagerie | Articulations artificielles, instruments chirurgicaux, micro-implants (par exemple, clous pour os) |
Energie et puissance | Boîtiers d'éoliennes, cuves sous pression de réacteurs nucléaires | Languette et rainure des pales de turbine, tiroirs hydrauliques, raccords de transmission |
Équipements industriels | Boîtiers de vannes, corps de pompes, bases de machines lourdes | Roulements de haute précision, vis, inserts pour moules, bras robotisés automatisés |
les communications électroniques | Dissipateur thermique pour station de base 5G, coque en alliage d'aluminium (moulage sous pression) | Connecteurs RF, dissipateurs de chaleur pour puces, boîtiers de micro-capteurs |
métro | Ébauches de disques de frein de train, attaches de rail | Usinage de boîtes d'essieu, coussinets de précision de bogies, pièces de systèmes de signalisation |
Construction navale | Pièces moulées pour hélices, chemises de cylindres de moteurs diesel marins | Système d'arbre de propulsion, engrenages de précision servo, raccords de conduites hydrauliques |
biens de consommation | ustensiles de cuisine en fonte, corps de serrure de porte, quincaillerie de salle de bains | Engrenages pour appareils ménagers intelligents, charnières de précision, cadres métalliques pour produits électroniques |
Bâtiment et infrastructure | Plaques d'égout municipales, nœuds de connexion de structures en acier, appuis de ponts | Fixations de coffrage de bâtiment, rails de guidage pour ascenseurs, accessoires de contreventement sismique |
Logique d'adaptation des processus: :
- couléemettent particulièrement l'accent surMoulage complexe en une seule piècePar exemple, des blocs moteurs avec des cavités internes, des boîtiers électroniques à parois minces moulés sous pression et des soupapes résistantes à la pression ;
- usinageconfocalComposants fonctionnels de précisionLes produits de cette catégorie sont : les chemins de roulement à grande vitesse, les implants médicaux de taille micrométrique, les canaux de précision pour le carburant d'aviation, etc.
Les deux types de processus sont souvent utilisés en tandem - le moulage pour obtenir des pièces brutes de forme presque nette, et l'usinage pour finir les zones critiques, afin d'obtenir ensemble un produit final de haute performance.
Que dois-je choisir ? Usinage ou moulage
Lorsque vous décidez d'utiliser l'usinage ou le moulage pour un projet de fabrication, vous devez procéder à une évaluation complète basée sur les caractéristiques de la conception, les objectifs de production et les conditions de ressources. Vous trouverez ci-dessous un examen approfondi des dimensions clés de la décision pour vous aider à adapter précisément votre processus à vos besoins.
1. échelle de production et évolutivité
- Sélectionner la fonteSi le projet nécessite une production de masse stable et à long terme (par exemple, des composants automobiles, des composants structurels pour les appareils électroménagers), le processus de moulage offre une réduction significative du coût par pièce à mesure que le volume de production augmente. La réutilisation des moules leur confère un avantage naturel dans la production à grande échelle, en particulier pour la reproduction rapide de produits standardisés.
- Sélectionner l'usinagePour les besoins de personnalisation de petites séries (par exemple, prototypage, pièces spécifiques à l'aérospatiale) ou les produits qui nécessitent des itérations de conception fréquentes, l'usinage élimine la nécessité de recourir à des outils coûteux, permet de répondre rapidement aux changements de commande et s'adapte avec souplesse à la production de petites et moyennes séries.
2. complexité structurelle des pièces
- Sélectionner la fonteSi la pièce présente des caractéristiques géométriques complexes telles que des cavités internes, des structures à parois minces, des voies d'écoulement multidirectionnelles, etc. (par exemple, un bloc moteur, un corps de soupape hydraulique), le moulage peut être réalisé en un seul passage dans la cavité du moule, ce qui évite les problèmes d'usinage en plusieurs processus, qui prennent beaucoup de temps.
- Sélectionner l'usinageSi la conception est axée sur des contours externes de précision, des réseaux de micro-trous ou des surfaces ultrafines (par exemple, bases de dispositifs optiques, implants médicaux), la précision de coupe de l'usinage permet un contrôle millimétrique des surfaces complexes et est particulièrement adaptée à la sculpture en profondeur de structures ouvertes.
3) Exigences en matière de précision et de cohérence
- Sélectionner la fonteLa précision dimensionnelle des pièces moulées dépend généralement de la qualité du moule et du contrôle du processus, et convient aux scénarios de précision moyenne (par exemple, raccords de tuyauterie, composants décoratifs). Pour les surfaces d'accouplement de haute précision, les coûts peuvent être réduits par un processus hybride de "moulage + finition partielle".
- Sélectionner l'usinageLorsque les pièces doivent respecter des tolérances de l'ordre du micron ou un ajustement serré (par exemple, les engrenages de précision, les cavités des dispositifs semi-conducteurs), l'usinage est en mesure de fournir des produits finis très cohérents grâce à la programmation numérique et à des équipements très rigides.
4. propriétés et compatibilité des matériaux
- Sélectionner la fontePour les métaux à bonne fluidité tels que les alliages d'aluminium, les alliages de zinc, la fonte, etc. Pour les matériaux recyclés (par exemple les lingots d'aluminium recyclés), le processus de coulée les fond et les remodèle efficacement, ce qui augmente considérablement l'utilisation des ressources.
- Sélectionner l'usinageCompatible avec un plus grand nombre de types de matériaux, y compris les alliages de haute dureté (alliages de titane, aciers trempés), les non-métaux (plastiques techniques, céramiques) et les composites. Particulièrement adapté à l'usinage de matériaux difficiles à mouler par fusion ou sensibles à la chaleur.
5. utilisation des matériaux et durabilité
- Sélectionner la fonteLa technologie de la forme quasi-nette minimise les déchets de matériaux et est particulièrement adaptée à l'usinage des métaux précieux ou rares. L'intensité carbone du moulage de l'aluminium recyclé ne représente qu'un tiers de celle de l'usinage de l'aluminium neuf, ce qui est conforme aux tendances de la fabrication écologique.
- Sélectionner l'usinageLes copeaux et rognures générés pendant le processus de coupe peuvent représenter une grande partie du poids de la matière première, et un système de recyclage des déchets est nécessaire pour réduire les coûts environnementaux.
6. la vitesse de production et les délais d'exécution
- Sélectionner la fonteL'étape de la mise au point du moule prend un certain temps, mais elle est extrêmement efficace lorsque la production en série est lancée, ce qui la rend adaptée aux projets à long délai de mise en œuvre et à production stable.
- Sélectionner l'usinageLe temps de cycle court entre le dessin et le produit fini le rend adapté aux commandes urgentes ou au prototypage itératif rapide, bénéficiant en particulier de l'agilité de la fabrication numérique.
7. comparaison des structures de coûts
- Postes de coûts essentiels pour la couléeLes coûts de conception et de fabrication du moule représentent la majeure partie de l'investissement initial, ce qui le rend adapté aux scénarios de dilution des coûts du volume de production.
- Postes de coûts essentiels pour l'usinageL'amortissement de l'équipement, l'usure des outils et les coûts de programmation de la main-d'œuvre dominent, ce qui convient aux petits lots de produits à forte valeur ajoutée.
8) Pratiques innovantes dans les processus hybrides
Pour la plupart des scénarios industriels, un processus unique ne répond souvent pas à tous les besoins.Stratégies recommandées: :
- Coulée + FinitionRéalisation de structures corporelles complexes par moulage, suivie d'une finition CNC des surfaces d'assemblage critiques (par exemple, boîtiers de boîtes de vitesses automobiles) ;
- Fabrication additive + découpeImpression 3D de pièces brutes de forme presque nette pour réduire les tolérances d'usinage (par exemple, les supports de forme pour l'aérospatiale).
Résumé : Des compromis dynamiques pour une prise de décision précise
- Scénarios de casting préférésLes produits de cette catégorie sont les suivants : grands volumes, structures internes complexes, sensibilité au coût des matériaux, orientation vers la fabrication écologique ;
- Scénarios d'usinage préférés: Petites tailles de lots, exigences élevées en matière de précision, usinage de matériaux durs, pression de livraison rapide ;
- La combinaison idéale des processus hybridesLes services d'assistance technique : Équilibrer l'efficacité et la précision pour obtenir la solution optimale en termes de coût et de performance.
L'expérience pratique de Ningbo Hexin montre que les cas de réussite découlent souvent de l'évaluation dynamique des dimensions susmentionnées. Il est recommandé aux entreprises de mettre en place un mécanisme d'examen des processus en collaboration avec plusieurs départements et de faire appel à des consultants techniques tiers si nécessaire, afin de s'assurer que la sélection des processus de chaque projet est scientifique, économique et durable.
problèmes courants
Q1 : Comment choisir le moulage ou l'usinage en fonction de la demande de production ?
Le choix du procédé doit être évalué en fonction du volume de production, de la complexité de la pièce, des caractéristiques du matériau et des exigences de précision - le moulage convient pour de grandes quantités de pièces structurelles complexes (telles que les blocs moteurs), peut être moulé à l'intérieur de la cavité mais la précision est limitée ; l'usinage convient pour de petites quantités de pièces de haute précision (telles que les engrenages de précision) et peut traiter une variété de matériaux, mais l'efficacité diminue en fonction de la complexité.
Q2 : Quel est le processus le plus rentable ?
Le coût du pré-moulage est élevé, mais le coût par pièce diminue avec le volume, ce qui convient à la production à grande échelle (par exemple, des millions de pièces de coques électroniques) ; l'usinage sans investissement dans le moule convient à la personnalisation de petites et moyennes séries (par exemple, les pièces aérospatiales), mais la perte de matériau fait augmenter le coût des technologies émergentes, telles que l'impression 3D sur sable, pour briser les frontières traditionnelles en matière de coûts.
Q3 : Comment la sélection des matériaux influe-t-elle sur les décisions relatives au processus ?
Le moulage est limité par la fluidité du métal (par exemple, le moulage sous pression de l'aluminium) et le point de fusion (par exemple, la fonte).moulage en sable), tandis que l'usinage peut couper des alliages très durs (par exemple, les alliages de titane) et des plastiques techniques, mais est susceptible de s'écailler sur des matériaux fragiles (par exemple, les céramiques) et nécessite des outils et des procédés spéciaux.
Q4 : Comment gérez-vous les pièces très complexes ?
La technologie de moulage par fusion permet de former en une seule pièce des cavités internes complexes (telles que les pales de turbines), l'usinage par CNC à cinq axes permet de découper des surfaces de précision (telles que les roues), mais la structure fermée nécessite une combinaison de processus : ébauches de moulage + finition par usinage (telle que l'alésage des cylindres), afin de parvenir à un équilibre entre la fonction et le coût.
Q5 : Quel est le procédé le plus respectueux de l'environnement ?
L'usinage doit faire face à la contamination des fluides de coupe et au recyclage des copeaux métalliques, mais les technologies vertes (coupe à sec, micro-lubrification) réduisent progressivement l'impact sur l'environnement, ce qui nécessite une optimisation de la production en boucle fermée.
Q6 : Est-il nécessaire de combiner deux processus ?
Les applications synergiques sont la norme : le moulage fournit des pièces brutes de forme presque nette (par exemple, les moulages d'engrenages) et l'usinage complète les caractéristiques de haute précision (par exemple, la rectification des dents) ; la fabrication additive + la finition CNC dépassent les limites traditionnelles pour répondre aux besoins ultra-complexes des pièces aérospatiales, et ainsi de suite.
Q7 : Lequel des deux est le plus rapide à choisir pour le prototypage ?
L'usinage permet d'obtenir des prototypes en métal ou en plastique en quelques heures grâce aux coupes directes de la CAO, tandis que le moulage associé à des modèles en cire imprimés en 3D réduit la durée du cycle de plusieurs semaines à quelques jours pour les prototypes fonctionnels qui nécessitent une vérification des propriétés des matériaux ou de la résistance de la structure.
Logique de baseLe moulage se concentre sur "l'efficacité du moulage", l'usinage se concentre sur "la précision et le contrôle", la sélection doit se faire autour des trois dimensions coût, temps, performance, la plupart des scènes doivent être complémentaires plutôt qu'alternatives.