Analyse des causes du grenaillage de précontrainte et solutions recommandées pour les produits en alliage d'aluminium ADC12 coulés sous pression
Temps de publication:2025-04-07 Trier par:Le blog Nombre de vues:370
Ce document analyse systématiquement la coulée sous pressionaluminiumLes propriétés matérielles de l'ADC12 sont corrélées au processus de grenaillage, et une solution multidimensionnelle est proposée pour résoudre le problème de l'écaillage par grenaillage qui se pose fréquemment dans l'industrie. L'article élucide tout d'abord l'influence directe de la composition chimique de l'ADC12 sur les propriétés des matériaux, révélant la corrélation intrinsèque entre les fluctuations de la teneur en silicium, cuivre, magnésium et autres éléments, ainsi que la fluidité, la solidité et la résistance à la corrosion de l'alliage. Basé sur le principe du processus de grenaillage de précontrainte, l'article analyse l'effet quantitatif des variables principales telles que les paramètres de tir et la vitesse d'éjection sur l'effet du traitement de surface, et souligne qu'il existe des lacunes communes dans l'industrie actuelle qui se concentre uniquement sur l'adhésion mais néglige la normalisation de la qualité de la surface. Grâce à l'analyse du flux des moules, à l'optimisation des paramètres du processus et à la vérification expérimentale, nous avons construit de manière innovante un système d'amélioration de l'ensemble de la chaîne, du contrôle de la source des matériaux à la conception des moules et à la maintenance de l'équipement. La recherche ne fournit pas seulement une voie technique quantifiable pour l'amélioration de la qualité du grenaillage ADC12, mais envisage également la nouvelle direction de l'optimisation des processus basée sur la technologie big data AI, qui est d'une importance pratique pour la promotion de la réduction des coûts et de l'efficacité dans l'industrie du moulage sous pression.
Propriétés matérielles de l'alliage d'aluminium moulé sous pression ADC12
1) Composition chimique
Les principaux éléments et leurs rôles
L'ADC12 contient principalement du silicium (Si), du cuivre (Cu), du magnésium (Mg), du manganèse (Mn), du fer (Fe), du zinc (Zn), de l'aluminium (Al). Parmi ces éléments :
Silicium : la teneur est autorisée entre 9,5 et 11,5%, si elle est inférieure à 9,5%, il y aura une mauvaise fluidité de l'alliage et un remplissage incomplet du produit, si elle est supérieure à 11,5%, il sera facile d'avoir une ségrégation excessive ou de former des cristaux lamellaires avec le ferro-aluminium, ce qui déstabilisera l'organisation de l'alliage et rendra le produit lâche ;
Cuivre : la teneur est autorisée entre 1,5 et 3,5% ; si elle est inférieure à 1,5%, la résistance et la dureté du produit diminuent ; si elle est supérieure à 3,5%, la résistance à la corrosion diminue ;
Magnésium : teneur de 0,1 ~ 0,3%, si la teneur en magnésium est inférieure à 0,1%, il y aura une diminution de la résistance et de la dureté du produit, si elle est supérieure à 0,3%, cela entraînera des fissures thermiques et d'autres défauts dans les produits de moulage sous pression ;
Manganèse : teneur de 0,2 ~ 0,5%, si elle est inférieure à 0,2%, le grain de l'alliage est grossier, la résistance à la traction et la limite d'élasticité sont réduites, si elle est supérieure à 0,5%, la fragilité de l'alliage augmente, il est difficile de le traiter et il est facile de le fragiliser ;
Fer : teneur en 0,6~1,2% ; si elle est inférieure à 0,6%, il est facile de coller au moule, ce qui entraîne une déformation du produit ; si elle est supérieure à 1,2%, l'alliage devient cassant et se fissure ; (le fer et le silicium sont en même temps très élevés, ce qui facilite la formation de cristaux de silicium, de fer et d'aluminium, ce qui entraîne une corrosion intercristalline et une diminution de la résistance de l'alliage).
Zinc : teneur ≤ 1,2%, le zinc peut donc être absent de l'alliage ADC12 (difficile à éliminer lors de l'affinage d'autres alliages), et s'il est présent, il doit être inférieur à 1,2%.
En outre, le ratio d'adaptation du matériau de recharge est également très important. Si le matériau de recharge est trop important, le grain de cristallisation du produit sera plus grossier, et la résistance et la dureté du produit seront réduites.
En résumé, la composition chimique (teneur en pourcentage) d'un alliage détermine essentiellement ses propriétés mécaniques et régit également l'aspect et l'organisation cristalline interne du produit.
2、Propriétés physiques
Alliage d'aluminium ADC12Densité : environ 2,7 g/cm³.(math.) genrePoint de fusion 580~620°CIl est important de noter que les valeurs de ces propriétés physiques peuvent varier en fonction de facteurs tels que les différences de composition spécifiques et les processus de production.
ADC12'sCoefficient de dilatation thermiqueRelativement importante, cette caractéristique est quelque peu liée au processus de dynamitage.
3. propriétés mécaniques
Les indices de propriétés mécaniques de l'alliage d'aluminium ADC12 sont généralement les suivants :
Résistance à la traction : environ 228~296MPa ;
Limite d'élasticité : environ 140~170MPa ;
Dureté Brinell : environ 70~95HB.
Élongation : 1~3%
Les indicateurs de performance spécifiques peuvent également varier en fonction de facteurs tels que les différences de composition et les processus de production.
Aperçu du processus de grenaillage de précontrainte
1、Le principe du grenaillage de précontrainte
Mécanisme de fonctionnement de l'équipement de grenaillage
Le mécanisme de fonctionnement du grenaillage se compose des éléments principaux suivants :
Systèmes de stockage et de transport des projectiles : les projectiles sont généralement stockés dans des trémies spécifiques et transportés vers la grenailleuse au moyen d'un convoyeur (par exemple, un convoyeur à vis) ;
Grenailleuse : il s'agit de l'élément central de l'équipement de grenaillage ; la grenailleuse est équipée d'une turbine qui tourne à grande vitesse ; la turbine comporte un certain nombre de pales ; lorsque la turbine tourne à grande vitesse, les pales entraînent l'accélération du projectile et son éjection à grande vitesse ;
Système de transport des pièces : utilisé pour transporter les pièces à traiter vers la zone de grenaillage et les renvoyer une fois le traitement terminé, les méthodes de transport couramment utilisées sont le transporteur à chenilles, le transporteur à crochets, le transporteur à rouleaux, etc ;
Système de dépoussiérage : le processus de grenaillage produit une grande quantité de poussière et d'impuretés ; le système de dépoussiérage génère une pression négative grâce au ventilateur, la poussière est aspirée dans le dépoussiéreur pour être filtrée et purifiée, afin de garantir un environnement de travail propre et conforme aux exigences environnementales.
Le grenaillage est une technologie de traitement de surface dont le principe consiste principalement à utiliser une roue rotative à grande vitesse pour projeter un projectile (généralement de la grenaille d'acier, du fil d'acier coupé, etc.) sur la surface de la pièce à traiter à une vitesse très élevée ; au cours du processus de grenaillage, le projectile a un impact d'énergie cinétique important sur la surface de la pièce pour produire un fort impact et un effet de raclage, cet impact peut éliminer la surface de la pièce de l'oxyde, de la rouille, de la saleté et d'autres adhérences, et en même temps dans la surface de la pièce. En même temps, la surface de la pièce produit une contrainte de compression, ce qui renforce la surface. Améliorer la résistance à la fatigue et à la corrosion sous contrainte ; en particulier, la turbine de l'équipement de grenaillage est entraînée par un moteur qui tourne à grande vitesse, le projectile est accéléré par la turbine qui le projette dans une direction spécifique, lorsque le projectile frappe la surface de la pièce, la surface du matériau de la pièce subit une déformation plastique et tombe, ce qui permet d'obtenir un effet de nettoyage et de renforcement.
L'effet du grenaillage dépend du matériau du projectile, de sa forme, de sa taille, de sa vitesse, de l'angle de tir, ainsi que de la durée du grenaillage et de nombreux autres facteurs. Les différentes pièces et exigences de traitement doivent choisir les paramètres appropriés du processus de grenaillage, afin d'obtenir la qualité et l'efficacité de traitement souhaitées.
2. Paramètres du processus de grenaillage
Matériau de grenaillage et taille : pour le grenaillage de l'alliage d'aluminium ADC12, on utilise généralement de la grenaille d'acier inoxydable 304 ou de la grenaille de fil d'acier ; le diamètre de la grenaille est compris entre 0,2 et 0,6 mm ;
Vitesse de sablage : la vitesse de sablage utilisée pour les alliages d'aluminium ADC12 est généralement de 50~70 m/s ;
Angle de grenaillage : généralement 30~75 degrés ;
Durée du grenaillage : en fonction de la taille, de la forme et de l'état de surface de la pièce, généralement de 5 à 15 minutes ;
Débit de grenaille : en fonction de l'équipement de grenaillage et de la pièce à traiter, il est généralement compris entre 90 et 280 kg/min ;
Principe de réglage : dans la production réelle, les essais et l'inspection de la qualité permettent de déterminer les paramètres du processus de grenaillage les mieux adaptés à la pièce à traiter, afin d'obtenir l'effet de traitement de surface souhaité et d'éviter le décollement, les plis et d'autres problèmes ; l'obtention de l'effet de traitement de surface idéal avec les paramètres les plus petits est l'objectif suprême du réglage des paramètres de grenaillage, mais aussi l'un des moyens de maximiser les avantages.
3. Processus de grenaillage pour le moulage sous pression des produits en alliage d'aluminium ADC12 dans l'application de la situation actuelle.
Pratiques courantes dans le secteur
L'objectif du grenaillage des pièces est uniquement d'augmenter l'adhérence de la peinture au four ou des exigences de pulvérisation du plastique, l'utilisation de grosses billes de grenaille, le temps de grenaillage est plus court, les pièces dépouillées par grenaillage utilisent un traitement de sablage de reprise, aucune étude fine des causes des problèmes tels que la peau de grenaillage, ainsi que le développement de programmes d'amélioration ;
Exigences strictes concernant la qualité de la surface de la pièce après le grenaillage, telles que la différence de couleur (la norme est le blanc argenté), le dépouillement (pas de pièces irrégulières suspendues à la surface du produit), les rides (la surface du grenaillage présente des rides), la déformation et d'autres défauts dans la réception de la normalisation de la limite inférieure ; de sorte que le processus de moulage sous pression de toutes les causes des trous d'air du produit, de la laxité, de la ségrégation à froid, des marques d'écoulement (stagnation) et d'autres défauts dans l'analyse des causes, et le développement de mesures visant à améliorer la grenailleuse, certaines des caractéristiques de la mise à niveau et de l'optimisation continue. Certaines des fonctions de la grenailleuse pour la mise à niveau, l'optimisation continue, la recherche de la qualité de la surface de grenaillage pour atteindre l'objectif de 0 défaut.
Problèmes et défis
Les pièces de grenaillage en alliage d'aluminium ADC12 de haute qualité sont des billettes de coulée sous pression de haute qualité à la fin du traitement de l'équipement de grenaillage, si les pièces de grenaillage apparaissent des écorchures et d'autres problèmes, la fin de l'analyse inverse des raisons : l'équipement de grenaillage est-il intact ? → L'utilisation des particules de grenaillage est-elle appropriée ? → La durée, la vitesse et le débit du grenaillage sont-ils appropriés ? → La rectification de l'ébauche de moulage sous pression est-elle conforme aux exigences ? → L'ébauche de coulée sous pression présente-t-elle des défauts d'aspect (ségrégation à froid, marques d'écoulement, taches, pores, fissures, etc.) → La production de moulage sous pression, la machine de moulage sous pression et les équipements périphériques sont-ils intacts ? → Les paramètres du processus (pression d'éjection, vitesse d'éjection, température de coulée, concentration du revêtement et volume de pulvérisation, etc.) sont-ils optimaux ? →moule de coulée sous pressionLe système de coulée, le système de refroidissement, le mécanisme d'éjection, la finition de la cavité, la pente de démoulage, la dureté des parties de la cavité, le coin arrondi de la cavité, etc. → Le mécanisme mobile du moule de coulée sous pression fonctionne-t-il de manière stable et fiable ? → Les paramètres du processus de fusion (matériau du four, température de fusion, température d'affinage, rapport de dosage de l'agent d'affinage, pression et débit de l'azote, etc. → Les éléments chimiques de l'ADC12 sont-ils conformes aux exigences ?
Dans la production réelle, on peut analyser qu'il y a un problème dans un certain lien, mais lorsqu'on résout ce problème, il faut examiner globalement s'il entraînera d'autres problèmes, d'où la nécessité d'une communication et d'une collaboration au sein de l'équipe, d'une argumentation à multiples facettes et d'une vérification expérimentale multiple.
03.
Analyse des causes du grenaillage de produits en alliage d'aluminium moulé sous pression ADC12
1) Facteurs matériels Source-ADC12
Teneur en silicium (Si) ≥ 11,5% : Fer (Fe) ≥ 1,2%, ce qui entraîne une chimiosynthèse excessive, ainsi qu'une organisation lamellaire, une organisation superficielle lâche et un décollement sous l'impact du grenaillage et du grattage ;
Magnésium (Mg) ≥ 0,3% : manganèse (Mn) ≥ 0,5%, zinc (Zn) ≥ 1,2% ; produisent des surfaces dures et fragiles ou des surfaces fissurées, sous l'impact du grenaillage, un grave écaillage et un manque de matériau se produiront ;
Cuivre (Cu) ≤ 1,5% : La résistance et la dureté de la surface du produit sont insuffisantes, sous l'impact du grenaillage et du grattage, une déformation concave et un écaillage ou un plissement se produiront ;
Ratio du matériau de retour du four ≥ 50% : l'élimination du laitier de fusion et le dégazage sont très difficiles, les propriétés physiques et mécaniques seront réduites, les produits moulés sous pression sont difficiles à obtenir une bonne surface (la porosité et les impuretés présentes dans le produit remplissent la surface finale), le grenaillage est facile à dépecer.
2、Facteurs de conception des moules de coulée sous pression
Le rapport entre la section du canal de coulée droite et la section du canal de coulée transversale n'est pas approprié, la section totale du canal de coulée transversale est plus grande que la section du canal de coulée droite, dans le canal de coulée transversale à la pression négative du volume de gaz, le gaz dans la cavité du moule pour augmenter la charge du canal d'échappement, le gaz est facilement résiduel dans le produit, la formation de trous d'air, la distribution des trous d'air à la surface peu profonde du produit, le grenaillage sera écorché ou cloqué ;
Remplissage de la carotte à branches multiples, espacement trop important entre les carottes, deux carottes au milieu de la formation d'un reflux de gaz piégé ; deux ou plusieurs carottes de la direction de remplissage de la carotte, formation de turbulences, la surface du produit aura des trous d'air (communément appelé stagnation de la tumeur), par l'impact de la force de grenaillage, il sera écorché ;
Le moule est conçu pour faire circuler l'eau de refroidissement, atteindre la fin du remplissage de la carotte, ce qui fait que la température du moule est toujours basse, la surface superficielle du produit présente une ségrégation à froid, des marques d'écoulement, des marques de piqûre et d'autres conditions de relâchement, l'impact de la force de grenaillage, il y aura un écorchage sérieux ;
La conception du moule du canal d'échappement ne peut pas répondre à la demande d'échappement (vitesse d'échappement supérieure à 350 m / s), l'emplacement du canal de débordement n'est pas à la fin du remplissage ou de la position défectueuse, ce qui entraîne l'échappement et le laitier n'est pas lisse et l'air piégé, le produit de remplissage de la fin de l'emplacement de la couche superficielle peu profonde des trous d'air, l'impact de la force de grenaillage, le dépouillement ;
La section transversale de la carotte du moule et de la porte intérieure est trop petite, la pression de remplissage est bloquée, ce qui augmente les difficultés de transfert de pression, le produit est lâche - la résistance et la dureté ne sont pas à la hauteur des exigences de l'impact de la force de sablage, il sera écorché ou déformé.
3. Facteurs relatifs aux machines de coulée sous pression et aux équipements périphériques
L'erreur de parallélisme et de planéité (≤ 0,5) de la plaque de la machine de coulée sous pression est importante, le serrage n'est pas solide, ce qui entraîne l'écoulement de l'eau d'aluminium sur la surface de séparation, l'épuisement de la pression de coulée, la diminution de la résistance et de la dureté du produit, l'impact de la force de grenaillage, l'écaillage du produit.
Excentricité entre le centre d'éjection du mécanisme d'éjection et le centre du trou d'éjection de la plaque modèle fixe, entraînant la stagnation du poinçon d'éjection, l'épuisement de la pression, la réduction de la résistance et de la dureté du produit, l'impact de la force de grenaillage et l'écaillage du produit ;
Jeu excessif entre le poinçon et la coupelle de fusion, refoulement de l'eau d'aluminium pendant l'injection de compression, entraînant la stagnation du poinçon, l'épuisement de la pression, la diminution de la résistance et de la dureté du produit, l'impact de la force de grenaillage, l'écaillage du produit.
Le moulage sous pression autour de la machine à vide, l'obstruction de la soupape à vide, la défaillance du vide, le produit emprisonné dans le gaz, la surface du produit apparaissant comme une ségrégation froide, des marques d'écoulement, des piqûres et d'autres conditions lâches, l'impact de la force de grenaillage, il y aura un écaillage sérieux ;
Défaillance ponctuelle de la machine de refroidissement, pression insuffisante de l'eau de refroidissement, débit insuffisant, entraînant une surchauffe des parties du moule concentrant la chaleur, le produit devrait faire partie de la contraction thermique et de la couche d'oxyde, l'impact de la force de grenaillage, le produit s'écaille.
4、Facteurs de réglage du processus de moulage sous pression
Le réglage de la température du four de maintien est faible (≤ 640 ° C), facile à la précipitation du silicium, facile à remplir la mobilité du liquide d'aluminium est réduite, facile à remplir le produit n'est pas plein, la couche superficielle du produit de la ségrégation froide, traces d'écoulement, pockmarks et d'autres conditions lâches, par l'impact de grenaillage, sera une peau grave ;
Si la pression de coulée et la vitesse de remplissage sont faibles, la résistance et la dureté du produit diminuent, l'impact de la force de grenaillage, le produit s'écaille ;
L'emplacement du point de départ du remplissage à grande vitesse n'est pas réglé correctement : 1. l'emplacement du point de départ à grande vitesse avant la tasse de fusion de l'air sera impliqué dans la cavité, la charge d'échappement du canal d'échappement augmente, le gaz est difficile à évacuer, le remplissage de la fin produira des trous d'air, les trous d'air de la surface superficielle du produit par l'impact du grenaillage, l'écaillage ; 2. l'emplacement du point de départ à grande vitesse après l'aluminium liquide dans la cavité à un rythme lent, il sera rapidement refroidi, le produit sera la formation d'une couche intermédiaire (ségrégation froide), lâche, l'impact de la force de grenaillage, l'écaillage du produit ; 3. l'emplacement du point de départ à grande vitesse après le liquide d'aluminium dans la cavité, refroidira rapidement, le produit formera un sandwich (ségrégation froide), lâche, l'impact de la force de grenaillage. Pelage du produit ;
Si le temps de pulvérisation est trop long, la température du moule est basse (185~230°C) ou la chaleur est déséquilibrée, le produit présentera une ségrégation à froid, des marques d'écoulement, des marques de piqûre et d'autres conditions de relâchement, et l'impact de la force de grenaillage entraînera un écaillage grave ;
Le temps de prise d'eau froide au point de haute pression (norme pour la fin du délai d'injection de pression de 3 ~ 8 secondes) est trop long, ce qui entraîne une température locale basse (185 ~ 230 ° C) ou un déséquilibre thermique dans le moule, le produit apparaîtra une ségrégation froide, des marques d'écoulement, des marques d'empois et d'autres conditions lâches, par l'impact de la force de grenaillage, il y aura un décollement sérieux ;
L'heure de début et de fin du vide de la machine à vide n'est pas réglée correctement, ce qui entraîne une défaillance du vide, le gaz piégé dans la cavité, la couche superficielle du produit des trous d'air par l'impact de la force de grenaillage, sera un écorchement grave ;
5, facteur de rectification des ébauches de moulage sous pression
Les bords volants des flans de moulage sous pression et des matériaux multiples ne sont pas nettoyés et polis, et la peau volante résiduelle après le grenaillage - écaillage ;
Le ponçage excessif des ébauches de moulage sous pression, la surface de l'ébauche de la couche dense de ponçage, l'impact de la force de grenaillage, la peau.
6, facteurs relatifs à la taille des particules de grenaille
Le diamètre des pastilles de sablage achetées n'est pas uniforme et est plus grand que le diamètre défini par le processus, ce qui entraîne une augmentation de la force de sablage, qui a pour effet de décoller le produit ;
7. Facteurs de réglage des paramètres du processus de grenaillage
Si la vitesse de grenaillage est trop élevée, la force d'impact augmente, ce qui entraîne un écaillage du produit ;
Si le temps de grenaillage est trop long, le raclage par impact continu entraîne le décollement de la couche dense du produit et l'écaillage du produit ;
Si le débit du projectile de grenaillage est trop important, l'impact du raclage augmente, ce qui entraîne le décollement de la couche dense du produit et l'écaillage du produit.
8. les facteurs environnementaux
L'environnement de sablage n'est pas ventilé et la température est élevée, ce qui entraîne un ramollissement de la surface du produit et un décollement du sablage.
Solutions recommandées pour le grenaillage de produits en alliage d'aluminium moulé sous pression ADC12.
1. les mesures d'amélioration matérielle
La composition chimique de la matière première achetée ADC12 est ramenée autant que possible aux valeurs intermédiaires autorisées ;
Les matériaux récupérés sont transformés en matériaux récupérés secondaires par un traitement graduel, utilisés avec de nouveaux matériaux, et la proportion de matériaux récupérés est réduite.
2. Mesures d'optimisation des rangées de moules de coulée sous pression et du système de refroidissement
L'analyse de l'écoulement du moule permet d'identifier le coin mort de remplissage de la carotte, les turbulences de l'air à pression négative, la fin de l'intersection et d'autres mauvais modes de remplissage, d'optimiser le mode de remplissage de la carotte, de réduire le reflux du coin mort, de réduire le volume d'air à pression négative, d'augmenter les réglages de débordement et d'échappement ;
Grâce à l'analyse du flux du moule, trouver la partie du laitier d'oxydation, le nœud thermique, ajouter le dispositif de refroidissement du point de moulage (mécanisme), de sorte que l'équilibre thermique du moule s'améliore.
3. Inspection et entretien des machines de coulée sous pression et des équipements périphériques
Pression du système de la machine de coulée sous pression ;
Force de serrage dans les machines de moulage sous pression - forces équilibrées sur les quatre colonnes de Göring ;
Précision de la pression, de la vitesse et de la position du poinçon dans le système d'éjection de la machine de moulage sous pression ;
Compresseur d'air, machine à vide, refroidisseur par points à haute pression, four de maintien, machine de pulvérisation, etc.
4、Optimisation des paramètres du processus de moulage sous pression
Réglage de la température du four de maintien 660°C±10°C
Point de départ de la haute vitesse de moulage sous pression dans le point de départ théorique de la haute vitesse sur la base de 60 ~ 100 mm à l'avance, les ébauches de production de moulage sous pression testées sont envoyées au grenaillage pour vérifier la meilleure position ;
La pression de coulée est fonction de l'épaisseur moyenne de la paroi du produit, la valeur recommandée étant la limite supérieure (1 ~ 3mm - pression de coulée 45 ~ 60MPa ; 3 ~ 6mm - pression de coulée 60 ~ 80MPa ; 6-10mm - pression de coulée 80 ~ 110MPa).
5、Le nettoyage et le polissage des ébauches de moulage sous pression sont des éléments essentiels de la mise à niveau standard.
Les normes de nettoyage et de polissage des ébauches de moulage sous pression, doivent être polies et nettoyées après que l'échantillon a été soumis à la vérification par grenaillage, pas de décollement des bords, polissage et nettoyage de l'échantillon standard à sceller, à libérer, et strictement selon l'échantillon pour polir et nettoyer les ébauches de moulage sous pression.
6. Entretien de la grenailleuse par contrôle ponctuel
La grenailleuse doit respecter les réglages pour chaque paramètre du processus ;
Les données affichées sur le moniteur de la grenailleuse doivent être exactes.
7, la sélection des particules de grenaille et la colocalisation des nouvelles et des anciennes particules
Les pastilles de grenaille doivent être tamisées à l'aide d'un tamis spécial ; si leur diamètre est supérieur aux exigences du processus, les pastilles tamisées par le fournisseur de pastilles doivent être rebroyées avant d'être utilisées et doivent être à nouveau tamisées ; la proportion de nouvelles pastilles ajoutées ne doit pas être supérieure à 60%.
8. le durcissement des paramètres du processus de grenaillage
Les paramètres du processus de grenaillage doivent d'abord être établis en fonction d'une vitesse relativement faible et d'un flux de projectiles de grenaillage, la durée du grenaillage étant aussi courte que possible, après la vérification du tir d'essai, pour confirmer que le produit est conforme à la qualité du grenaillage (pas de peau, pas de différence de couleur), afin de consolider les paramètres du processus.
9、Temperature control of the blasting environment (contrôle de la température de l'environnement de sablage)
L'environnement de sablage doit être sec et ventilé, et la température ne doit pas dépasser 30°C.
Cas de validation expérimentale
ADC12 Die Casting - Motor Shell Blank Shot Peeling Liste des problèmes
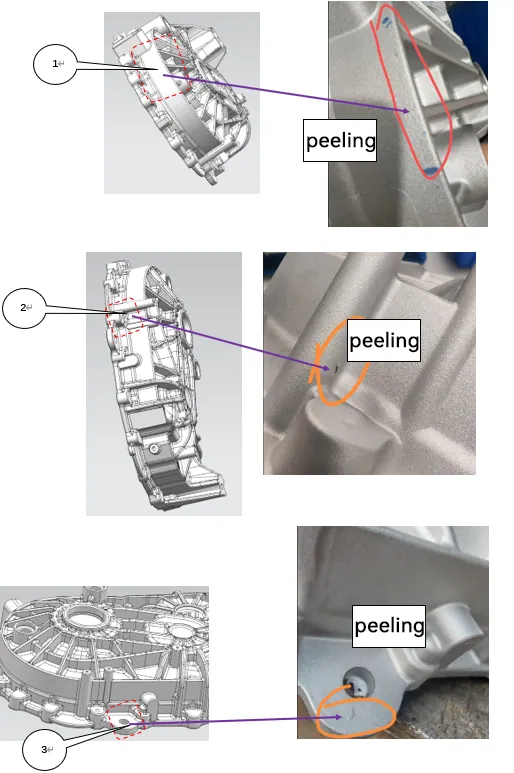
1. l'analyse des causes de chaque partie écorchée
La position ① ② ③ est la fin du remplissage, le gaz d'échappement n'est pas lisse et la pression de remplissage est faible, ce qui est la principale raison, suivie par une température de coulée de l'aluminium basse ; la position ② montre que le temps de grenaillage est trop long, la surface du phénomène de rides, en substance, la résistance et la dureté du produit sont inégales et faibles (billettes de coulée sous pression à proximité du pelage avec ségrégation à froid et marques d'écoulement).
2、Développer des mesures d'amélioration pour chaque zone écorchée.
(1) Déboucher le canal d'échappement et l'approfondir de 0,05 mm.
(2) Optimisation des paramètres du processus de moulage sous pression ~ deux accumulateurs rapides pour ajouter de l'azote (de 11,5MPa à 12MPa), augmentation de la pression de stockage de l'énergie (de 13,5MPa à 14,5MPa) ; augmentation du réglage de la température du four de maintien (de 645°C à 660°C) ;
(3) Optimisation des paramètres du processus de grenaillage ~ réduction du temps de grenaillage (de 6 minutes à 5 minutes pour le grenaillage d'un seul côté sur les suspensions exposées).
3. les mesures de mise en œuvre des tâches de l'équipe
(1) L'équipe de réparation des moules répare la plaque d'échappement du moule, la profondeur de l'échappement étant de 0,05 mm.
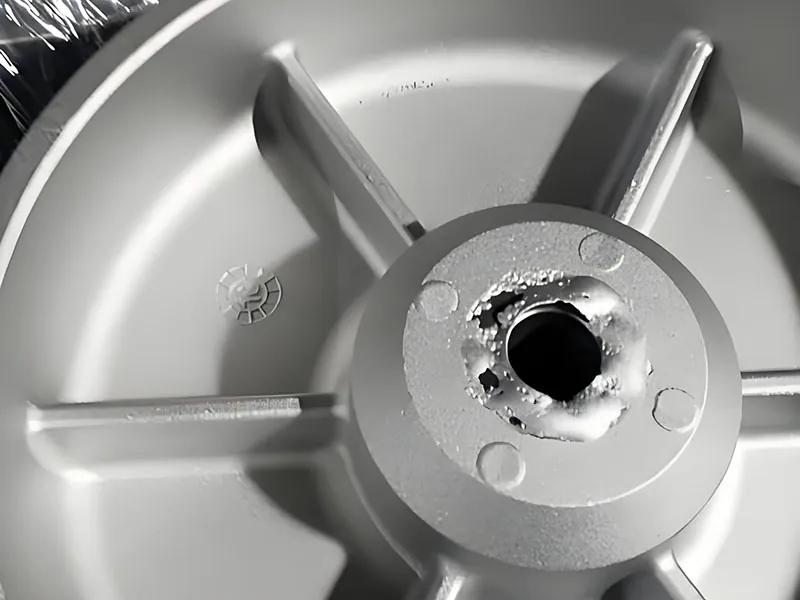
(2) le groupe de processus de moulage sous pression, conformément aux mesures d'amélioration, réinitialise les paramètres de la deuxième pression de stockage rapide de 14,5 MPa, la température du four de maintien est réglée à 660 ° C ;.
(3) L'équipe chargée du processus de coulée sous pression a réinitialisé le temps de soufflage à 5 minutes.
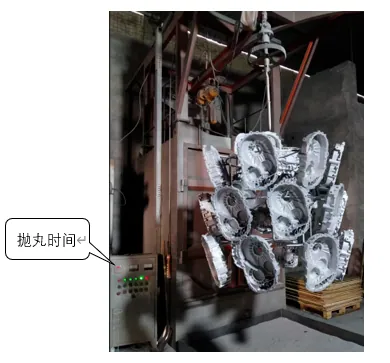
4. mise en œuvre et test des mesures
Après la mise en œuvre des mesures d'amélioration, il a été vérifié par grenaillage et jugé qualifié par l'inspection du département de la qualité, comme le montre la figure ci-dessous :
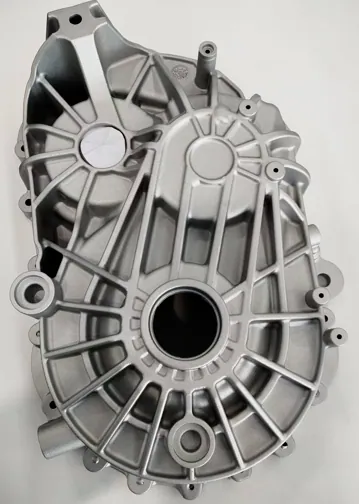
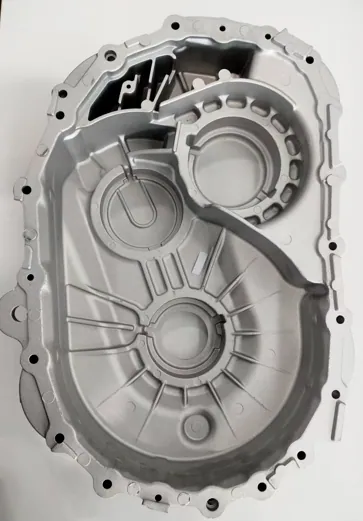
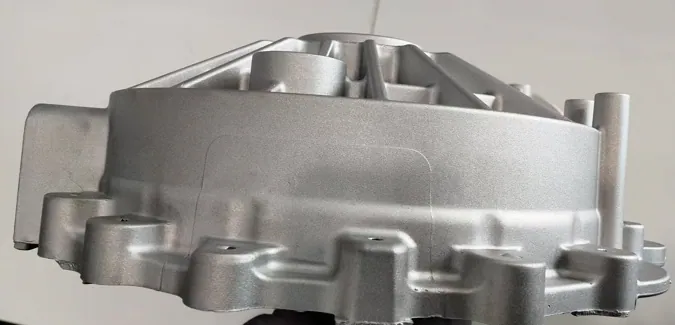
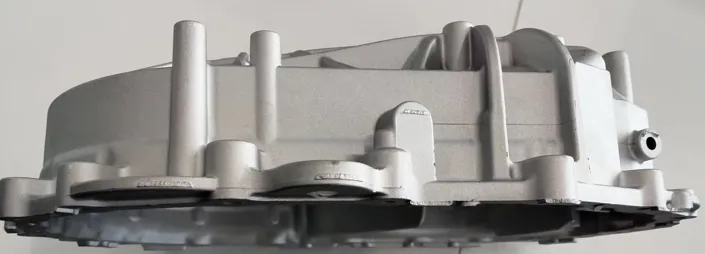
Synthèse des résultats des améliorations
En utilisant la méthode d'élimination pour trouver la cause exacte du grenaillage de précontrainte, puis en formulant des mesures correspondantes pour résoudre le problème du grenaillage de précontrainte des produits en alliage ADC12 à un faible coût expérimental, ce résultat est la poursuite de l'industrie de la coulée sous pression, mais aussi l'objectif.
Conclusions et perspectives
1) Conclusions de l'étude
L'analyse de la composition chimique, des propriétés physiques et des propriétés mécaniques de l'alliage d'aluminium ADC12, l'analyse du processus de moulage sous pression permettent de s'assurer que la résistance et la dureté des produits en alliage d'aluminium ADC12 sont conformes aux conditions nécessaires, la compréhension des grains de grenaille, l'analyse du processus de grenaillage permettent d'analyser le processus de grenaillage sur le produit avec la force d'impact et de grattage. La résistance et la dureté de l'alliage d'aluminium ADC12 ne répondent pas aux normes, le grenaillage est facile à écorcher ; si les particules de grenaille, le flux du projectile de grenaille, le temps de grenaillage sont trop longs, les produits en alliage ADC12 par grenaillage sont également faciles à écorcher, il est donc nécessaire de trouver un équilibre entre les deux.
Comme mentionné dans le cas ci-dessus, la résistance et la dureté du produit n'étaient pas conformes aux normes, et la résistance et la dureté ont été améliorées, et le temps de grenaillage était trop long, et le temps de grenaillage a été raccourci grâce à des améliorations, et finalement nous avons obtenu des produits qualifiés de grenaillage pour l'alliage ADC12.
2. les lacunes et les perspectives de la recherche
Lacunes du processus de recherche : en raison du petit nombre d'expériences et de la difficulté à détecter la résistance locale du produit, il n'a pas été possible de trouver la résistance et la dureté du produit adapté au grenaillage sans écorcher le point critique (données), ce qui n'a pas permis d'atteindre le coût le plus bas de la résistance et de la dureté du produit en alliage ADC12 et de l'impact du grenaillage et de la force de raclage de l'équilibre.
Perspectives pour l'orientation future de la recherche : avec le développement de la technologie big data AI, je pense que la même industrie résoudra le problème du grenaillage de précontrainte de l'alliage ADC12 de manière plus approfondie, dépensera moins d'argent et récoltera plus d'avantages.
problèmes courants
- Q : Quels sont les avantages de l'ADC12 en termes de performances de moulage ?
A : Excellente fluidité, facilité de moulage de pièces de précision complexes, forte résistance à la corrosion, adapté à la production de masse. - Q : Comment puis-je éviter les peelings de décapage ?
R : Un contrôle complet de la composition des matériaux, de la conception de l'échappement du moule, des paramètres du processus de moulage sous pression (par exemple, température, pression) et des paramètres de grenaillage est nécessaire. - Q : Comment les paramètres du processus de sablage sont-ils définis ?
A : Le matériau de la grenaille (comme la grenaille d'acier inoxydable), la vitesse (50 ~ 70 m / s), le temps (5 ~ 15 minutes) doivent être ajustés en fonction des caractéristiques de la pièce à usiner. - Q : Quels sont les défauts les plus courants après le grenaillage ADC12 ?
R : Décollement, plissement, déformation, etc., principalement dus à une composition excessive du matériau, à une mauvaise conception du moule ou à des paramètres de sablage inadéquats. - Q : Quelles sont les orientations pour l'optimisation des moules ?
R : Améliorer la conception de la carotte en analysant le flux du moule, augmenter le canal d'échappement et le canal de débordement pour éviter les trous d'air et la ségrégation par le froid. - Q : Comment le processus de moulage sous pression est-il ajusté ?
A : Augmenter la température du four de maintien (660°C ± 10°C) pour optimiser la pression de coulée et la vitesse de remplissage afin de garantir un produit dense. - Q : Comment les grains de grenaille sont-ils sélectionnés ?
R : Utilisez des granulés en acier inoxydable d'un diamètre de 0,2 à 0,6 mm, passez-les au crible pour éliminer les particules trop grosses et mélangez proportionnellement les nouveaux et les anciens granulés. - Q : Quelles sont les meilleures pratiques pour définir les paramètres de dynamitage ?
R : Les paramètres initiaux sont réglés sur une vitesse faible, un temps court et un faible débit de grenaille, puis ajustés progressivement jusqu'à ce qu'il n'y ait pas d'écorchures et que la qualité de la surface soit atteinte.