Conception et fabrication de moules pour le moulage sous pression de l'aluminium
Temps de publication:2024-08-05 Trier par:Le blog Nombre de vues:1703
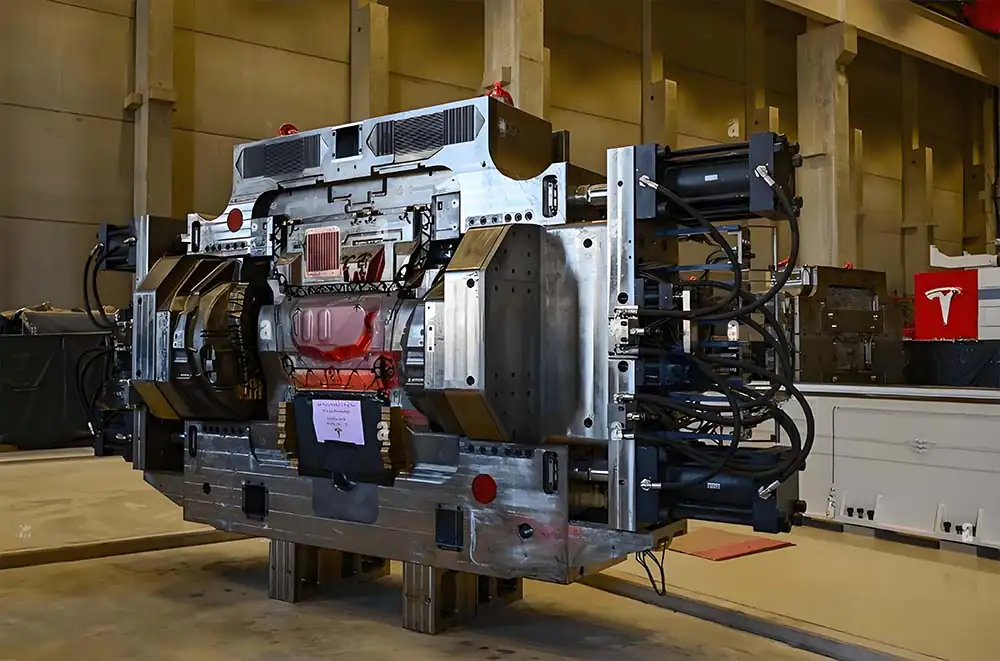
A. Introduction à la technologie du moulage sous pression
Le moulage sous pression, appelé aussi moulage sous pression, est l'utilisation d'une machine de moulage sous pression qui remplit l'alliage liquide fondu à une certaine vitesse en fonction de la structure de certaines pièces et des exigences du processus de conception et après la fabrication de précision de la cavité du moule, et l'alliage liquide fondu est maintenu sous une certaine pression, sous l'action de la cavité du moule, du refroidissement, de la solidification et de la mise en forme d'une sorte de technologie de moulage de précision à haute efficacité et à haut rendement.
B. Caractéristiques et champ d'application de la technologie de moulage sous pression
1, les caractéristiques de la technologie du moulage sous pression
La haute pression et la haute vitesse sont les deux principales caractéristiques du processus de moulage sous pression de métal liquide ou semi-liquide, mais la technologie de moulage sous pression et les autres méthodes de moulage constituent également la différence la plus fondamentale.
2、Le champ d'application de la technologie de moulage sous pression
La technologie du moulage sous pression est l'une des méthodes de formage des métaux les plus avancées et constitue un moyen efficace de réduire le nombre de copeaux et d'en éliminer. Actuellement, l'alliage utilisé pour le moulage sous pression ne se limite plus aux alliages de zinc, d'aluminium, de magnésium et de cuivre, mais s'étend progressivement à la fonte, à l'acier moulé et à d'autres alliages de fer pour produire des pièces moulées sous pression.
C. Tendance de développement de la technologie de moulage sous pression
L'utilisation de la technologie du moulage sous pression présente des avantages économiques positifs et évidents pour les entreprises. L'avenir du moulage sous pression
La technologie évolue dans le sens de :
(1) La technologie du moulage sous pression évolue dans le sens de l'intelligence.
(2) Recherche et développement de nouveaux matériaux pour le moulage sous pression afin de répondre aux besoins du progrès technologique industriel.
(3) Recherche et développement de nouveaux types d'équipements de moulage sous pression pour améliorer le niveau d'automatisation.
(4) Développement de nouvelles technologies de détection.
(5) Développement de nouvelles technologies de moulage sous pression et amélioration du processus de moulage sous pression.
(6) Amélioration de la durée de vie des moules de coulée sous pression, réduction des coûts de production pour résoudre le problème de la coulée sous pression des métaux ferreux, progressivement étendue à la fonte, à l'acier moulé et à d'autres alliages de fer pour produire des pièces moulées sous pression.
Conception de moules de coulée sous pression
A. Aperçu de la conception des moules de coulée sous pression
- Le moulage sous pression, le moule de moulage sous pression, la machine de moulage sous pression, l'alliage de moulage sous pression à travers les paramètres du processus de moulage sous pression de la coordination interconnectée, l'achèvement commun du processus de moulage sous pression de moulage sous pression. Le moule de coulée sous pression dans le processus de production de la coulée sous pression est le suivant :
- Déterminer le système de coulée, en particulier la position de la porte intérieure, la direction de l'infusion et la position du système de débordement, qui déterminent ensemble les conditions de remplissage du métal en fusion et les conditions de moulage ;
- ②, le moule de coulée sous pression est la reproduction de la coulée sous pression, il détermine la forme et la précision de la coulée sous pression ;
- ③, la qualité de la surface de formage du moule affecte directement la qualité de la surface de la pièce moulée sous pression et l'importance de la résistance au démoulage.
- ④, après le moulage sous pression, s'assurer que les pièces moulées sont dégagées en douceur du moule de moulage sous pression et qu'après avoir poussé le corps du moule, il ne doit pas y avoir de changement dans la position des pièces moulées.
- L'apparition de formes, de ruptures, etc ;
- ⑤. La résistance et la rigidité du moule pour supporter l'impact de la force d'injection et la vitesse de la porte intérieure sur le moule ;
- (vi) Contrôler et réguler l'échange de chaleur et l'équilibre thermique du moule pendant le processus de coulée sous pression ;
- (vii) Maximiser l'efficacité de moulage de la machine de coulée sous pression.
B. Principes de base de la conception des moules de coulée sous pression
(1) comprendre parfaitement l'utilisation du moulage sous pression et d'autres pièces structurelles de la relation d'assemblage, et en fonction des caractéristiques structurelles du moulage sous pression, l'utilisation des performances, dans la conception du moule pour faire la distinction entre le principal et le secondaire, en soulignant les points clés de la structure du moule ainsi que la combinaison avec le traitement du processus de moulage, le choix raisonnable de la surface de séparation du moule, le nombre de cavités et la disposition de la forme du moulage sous pression de la forme du lancement de la forme du côté de la forme de démoulage du moule.
(2) Comprendre la capacité de traitement réelle du moule du site, comme l'équipement existant et collaborer avec l'équipement de l'unité, ainsi que le niveau technique de l'opérateur, combiné à la conception réelle de la forme de la structure du moule en accord avec la capacité de traitement du site.
(3), le moule doit s'adapter à la production de moulage sous pression des différentes exigences du processus, choisir en fonction des exigences du processus de moulage sous pression le système de coulée et le système de débordement, en particulier l'emplacement de la porte intérieure, la vitesse de la porte intérieure et la direction du flux de liquide, doivent permettre au métal liquide de s'écouler en douceur et sans à-coups, et l'évacuation ordonnée du gaz de la cavité, afin d'obtenir un bon effet de remplissage et d'éviter la génération de défauts dans le moulage sous pression.
(4) Afin de garantir la stabilité de la qualité des pièces moulées sous pression et la sécurité de la production, les moules de moulage sous pression doivent présenter les caractéristiques suivantes :
①, structure simple, avancée et raisonnable, fonctionnement précis et fiable, procédure d'exploitation réduite.
②, facile à utiliser, sûr et rapide, facile à démonter les pièces d'usure, facile à entretenir, faible coût de fabrication.
(iii) Efficacité accrue du moulage sous pression, remplissage et ouverture rapides des moules, mécanisme de démoulage souple et fiable et degré élevé d'automatisation.
(5) Les pièces structurelles des moules doivent répondre aux exigences du processus d'usinage et du processus de traitement thermique. La sélection appropriée des matériaux, en particulier les pièces de moulage et les autres pièces en contact direct avec le métal liquide, doit être effectuée à partir d'un acier de haute qualité résistant à la chaleur et au traitement de durcissement, de manière à ce qu'il présente une résistance suffisante à la déformation thermique, une résistance à la fatigue, une dureté et d'autres propriétés mécaniques globales, ainsi que des propriétés de résistance à la corrosion.
(6), il convient de tenir pleinement compte des changements de température du moule sur les parties glissantes relatives de la précision de l'appariement provoquée par l'impact.
(7) La conception des moules doit être basée sur la faisabilité d'un examen complet de l'économie.
La structure générale du moule est simple, pratique et peu coûteuse.
②, il faut choisir une taille économique, pratique et adaptée à la précision.
(iii) Veiller à réduire la consommation de matériaux résiduels du système de coulée.
Outre les exigences de base de la conception normale, il convient d'accorder une attention particulière :
1. adopter une structure simple, raisonnable et avancée, pour que la pièce soit précise et fiable, et que la rigidité de la structure soit bonne, c'est-à-dire que le moule ait une épaisseur suffisante pour garantir une rigidité suffisante afin d'éviter que le moule ne se déforme et ne se fissure. Il est également nécessaire de considérer que le moule est facile à démonter et à changer, ce qui est propice à l'amélioration de la qualité de la production.
Prolonger la durée de vie du moule ;
2) Les pièces du moule doivent répondre aux exigences du processus d'usinage et du processus de traitement thermique. Il faut essayer d'éviter ou de réduire les angles vifs et les parois minces afin de faciliter le traitement thermique ultérieur et d'éviter la concentration des contraintes. Si la structure ne peut éviter les angles vifs, il convient de procéder à l'ébauche pour réserver un angle R suffisant, le traitement thermique après l'usinage en place pour éviter le risque de fissuration due au traitement thermique.
3. grandemoule de coulée sous pression(La surface projetée du plan de joint est supérieure à 1 mètre carré), il convient d'utiliser un système de guidage par colonne carrée afin d'éviter que la précision du guidage ne soit réduite en raison de la grande différence de dilatation thermique entre les moules mobiles et les moules fixes ;
4. Pour la conception du système de coulée, du système d'échappement et du système de refroidissement d'un grand moule de coulée sous pression complexe, il est préférable de procéder à une analyse des flux et à une analyse du bilan thermique. Comme nous le savons tous, le système de coulée est le métal liquide de la chambre de pression dans la cavité, il est étroitement lié au métal liquide dans les parties de la cavité, à la direction, à l'état de l'écoulement, et peut ajuster la vitesse de remplissage, le temps de remplissage, la température de la cavité et d'autres conditions de remplissage. Dans la production de moulage sous pression, le système de coulée sur la qualité du moulage sous pression, l'efficacité de l'opération de moulage sous pression, la durée de vie du moule (haute température, haute pression, métal liquide à haute vitesse sur la paroi de la cavité du moule, décapage, corrosion, etc.
et son importance ;
5. considérations relatives à la conception des portes intérieures :
Le liquide métallique à haute température qui pénètre dans la cavité par la porte intérieure ne doit pas pénétrer positivement dans la paroi et le noyau du modèle dynamique fixe, afin d'éviter l'érosion précoce, le collage du moule et la fissuration, etc. ; lors de l'adoption d'une porte intérieure multibrins, il faut envisager d'éviter les défauts de vortex, d'enveloppement de gaz et de scories oxydatives, etc. qui sont causés par l'impact du métal liquide dans la cavité à partir de quelques voies de convergence ; le choix de l'épaisseur de la porte intérieure est généralement formulé en fonction des données empiriques, et il est recommandé d'en choisir une plus grande dans les conditions de remplissage du moule pour éviter l'érosion précoce, le collage du moule, les piqûres et les fissures causés par une vitesse d'injection à pression excessive. En fonction du type de remplissage, il est préférable de choisir un moule plus grand afin d'éviter l'impact d'une compression et d'une vitesse d'injection trop importantes, qui entraîneront une érosion, un collage du moule, des piqûres et des fissures au début de la construction du moule ;
6. la conception des réservoirs de débordement et d'aération :
Le rôle du canal de débordement est d'accumuler le liquide métallique froid et le liquide métallique enveloppé de gaz qui pénètrent d'abord dans la cavité, ainsi que de réguler la température de chaque partie du moule afin d'améliorer l'équilibre thermique du moule, ce qui est propice à la prolongation de la durée de vie du moule. Généralement situé à la fin du processus de métal liquide, l'installation d'un réservoir de débordement approprié permet d'améliorer les conditions de remplissage et la qualité des pièces moulées. La rainure d'échappement est utilisée pour évacuer l'air et le gaz de volatilisation de la peinture de la cavité, dont l'emplacement est lié à l'emplacement de la porte intérieure et à la structure du produit. Afin de rendre l'injection de gaz dans la cavité aussi éloignée que possible du moulage sous pression de la décharge de métal liquide, la rainure d'échappement sera placée dans la dernière partie du remplissage de métal liquide. Le réservoir d'échappement est généralement combiné avec le réservoir de débordement, disposé à l'extrémité arrière du réservoir de débordement, afin de renforcer l'effet de débordement et d'échappement.
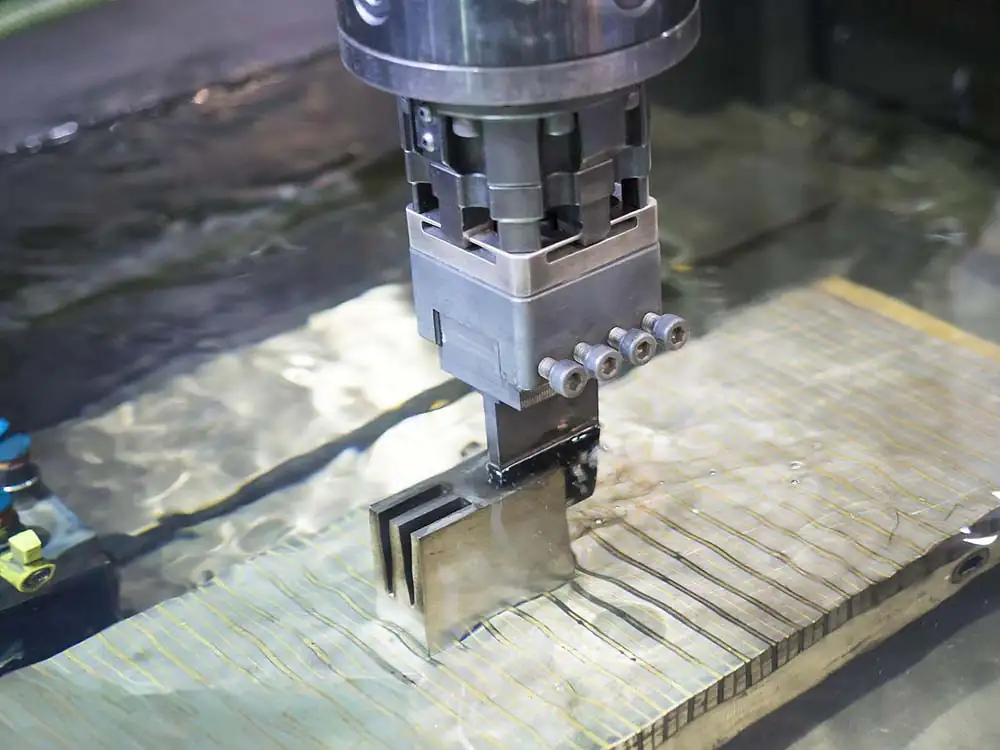
L'effet de l'usinage sur la défaillance des moules
Comme nous le savons tous, les moules de coulée sous pression ont un long cycle de fabrication et un usinage complexe, impliquant le tournage, la rectification, le fraisage, le perçage et le rabotage.usinageet l'usinage par décharge électrique (découpe au fil, EDM) et d'autres procédés. La qualité du traitement, en particulier la qualité du traitement de surface dans le processus de fabrication du moule et l'utilisation ultérieure du processus, affectera de manière significative la résistance à la rupture, la résistance à la fatigue, la résistance à la fatigue thermique et la résistance à l'usure, la résistance à la corrosion, etc. du moule. Une légère erreur de traitement peut entraîner une défaillance précoce du moule. Par exemple, les fissures et les fissures thermiques sont les suivantesaluminiumIl s'agit d'un phénomène de défaillance courant dans les moules de coulée sous pression, qui est causé par la fatigue thermique, la contrainte, la faible résistance et la rugosité de la surface du moule.
1, l'impact du traitement des coupes
Ces contraintes internes réduisent la résistance totale de la surface du module, entraînant un manque de résistance à la fatigue thermique, ce qui produira des fissures ou des craquelures dans les coins et une transition d'arc à faible rayon. Il convient donc d'éviter autant que possible les angles vifs. Les angles vifs et les coupes d'usinage peuvent provoquer une concentration de contraintes, sauf exigences particulières, sinon, il faut éviter les angles vifs et élargir complètement le rayon de courbure de l'arc, afin d'éviter ou de réduire la concentration de contraintes. Par exemple, si le rayon de l'arc R passe de 1 mm à 5 mm, la contrainte interne maximale est réduite d'environ 40%, ce qui améliore considérablement la ténacité du moule. Lorsque le rayon d'arc du module passe de 2 mm à 20 mm, la résistance aux chocs peut être multipliée par 4. De même, la taille de la rugosité de la surface du moule a un impact plus important sur la durée de vie du moule. L'existence de marques de couteau évidentes, de fissures, de coupures, etc., ces défauts de traitement entraîneront une concentration des contraintes et deviendront la cause première des fissures. Par conséquent, pour garantir la rugosité de la surface du moule, la surface de la cavité doit être meulée et polie afin d'éliminer les marques de coupe et autres défauts. Le processus de perçage du trou d'eau de refroidissement, si le perçage bidirectionnel est mal aligné, provoquera des fissures précoces à l'endroit concerné et des fuites d'eau. Après le forgeage et le recuit de l'embryon de moule, ou de l'embryon de moule, le noyau, après le traitement dans le four à air, le chauffage et la trempe, il y a généralement une certaine épaisseur de couche de décarburation, le traitement de coupe doit être la couche de décarburation entièrement enlevée. Sinon, la couche de décarburation résiduelle dans l'utilisation du moule réduira la résistance à la fatigue thermique de la surface du moule, ce qui entraînera la fissuration de la pièce.
2. l'effet du processus de broyage :
Après le traitement thermique des moules de coulée sous pression, les problèmes suivants peuvent survenir lors du meulage (y compris le serrage et le meulage à la meule) :
A. La fissuration est due à une meule trop dure, à une alimentation trop importante, à une vitesse de meulage trop élevée, à une contrainte de meulage trop importante, à un refroidissement insuffisant ou à une mauvaise sélection du liquide de refroidissement. En raison de la dureté de la meule, la chaleur de friction générée par la contrainte de traction est supérieure à la résistance à la rupture du matériau, ce qui entraîne l'apparition de fissures ;
B. Brûlures de meulage et ramollissement de la surface. La surface ramollie en contact avec le métal fondu coulé sous pression, en raison de sa résistance relativement faible et de sa résistance à la fatigue thermique également insuffisante, conduit facilement à la fissuration, à l'érosion et à la piqûre.
C, contrainte de meulage. Le meulage de la surface du moule entraîne une contrainte de meulage, réduisant la résistance de la surface du moule et la résistance à la fatigue thermique, conduisant à des fissures ou à des fissures dans le coin du moule et la transition de l'arc R, il peut être inférieur à la température de trempe de 20 ~ 30 ℃ pour un traitement de trempe, afin d'atteindre l'objectif d'élimination de la contrainte.
3. les effets du traitement des rejets
A. Produit une couche blanche durcie et brillante
L'usinage par décharge électrique (EDM et WEDM) des cavités des moules est généralement effectué après que le moule a été trempé afin de garantir la précision du moule. Pendant le processus d'usinage, en raison des températures élevées (jusqu'à des milliers de degrés Celsius, voire des dizaines de milliers de degrés Celsius) générées instantanément par une seule décharge, le métal à la surface du moule est rapidement fondu, vaporisé et évaporé. L'application d'un liquide de refroidissement rapide entraîne, à partir de la surface, dans l'ordre : une couche de resolidification (d'une épaisseur pouvant atteindre 0,2 mm lors d'une frappe grossière, une frappe fine pouvant atteindre 0,01 mm environ), une couche durcie par une nouvelle trempe (son épaisseur est généralement inférieure à 0,05 mm, le côté le plus superficiel de l'organisation de la trempe surchauffée, fragile et très sensible aux fissures), une couche adoucie par une trempe à haute température et l'organisation normale de la matrice. À l'intérieur de cette couche durcie, en particulier dans la couche de resolidification, on observe de nombreuses fissures fines, des fissures qui s'étendent même à la couche durcie par la trempe (souvent appelée couche blanche brillante ou couche métamorphique). Sa présence peut provoquer des accidents tels que des fissures ou des craquelures précoces du moule. (Par exemple, c'est souvent le cas pour les inserts de moules tels que les carters d'embrayage et les corps de boîtes de vitesses des automobiles). Il est donc nécessaire d'éliminer complètement cette couche de déformation par un meulage manuel, un meulage chimique ou un meulage électrolytique.
B, EDM rugosité de surface et résistance à la fatigue de la relation entre l'usinage par décharge électrique des paramètres de jauge électrique, matériaux d'électrode, par rapport à l'usinage, sa résistance à la fatigue est beaucoup plus faible. Coup rugueux, dans la largeur d'impulsion de 1050μ s lorsque sa résistance à la fatigue est d'environ 60% pour l'usinage.
C. Mesures de protection
Indépendamment de la profondeur de la couche blanche du traitement de décharge, pour les mauvaises conditions de travail des moules de coulée sous pression, cette couche blanche doit être éliminée (broyage) ; ajuster les paramètres du processus de décharge, de préférence un traitement de décharge grossier et fin en deux étapes, autant que possible utiliser des paramètres de processus à haute fréquence et à faible courant, contrôler la couche blanche d'environ 0,01 mm ; le traitement de décharge, en plus du ponçage pour éliminer la couche blanche, mais aussi doit être immédiatement effectué pendant une période de temps suffisamment longue pour le traitement secondaire de la couche blanche. La température de revenu est généralement plus élevée que la température de revenu final. La température de revenu est généralement inférieure à la température de revenu final de 20 ~ 30 ℃ ou 30 ~ 50 ℃, afin d'éliminer complètement la contrainte de traction sur la surface, d'améliorer la stabilité du revenu de la couche retrempée, de réduire la fragilité.
En général, les défauts de coupe, de meulage et d'usinage par décharge électrique sur la surface du moule réduisent la qualité de la surface du moule et provoquent une concentration des contraintes. Pour le moule de coulée sous pression dans des conditions de travail à haute température et à haute pression, sous l'effet d'une alternance de contraintes thermiques et de contraintes mécaniques, la surface du moule est susceptible de se fissurer, de se fissurer et de se corroder, ce qui entraîne une défaillance précoce du moule. (Bien entendu, la qualité de l'acier, la conception, le traitement thermique, l'utilisation, l'entretien et de nombreux autres facteurs ont également une incidence). Tous ces éléments méritent une grande attention de la part des ingénieurs chargés de la conception des moules, des artisans techniques, des opérateurs de production et des inspecteurs de la qualité. Proposer des exigences raisonnables en matière de qualité de la surface des moules, essayer d'éviter les angles aigus des pièces, les raccords de transition des arcs à faible rayon et les marques de couteau évidentes, contrôler les paramètres de la jauge électrique de l'usinage par décharge, éliminer la couche blanche et brillante, etc. Développer la norme d'acceptation de la rugosité de la coupe, de l'usinage par décharge électrique et de la rectification par serrage, et mettre en œuvre de manière stricte le système d'inspection pour chaque processus. Cela permettra d'éviter efficacement la défaillance précoce du moule causée par un traitement inadéquat et d'améliorer la durée de vie du moule.
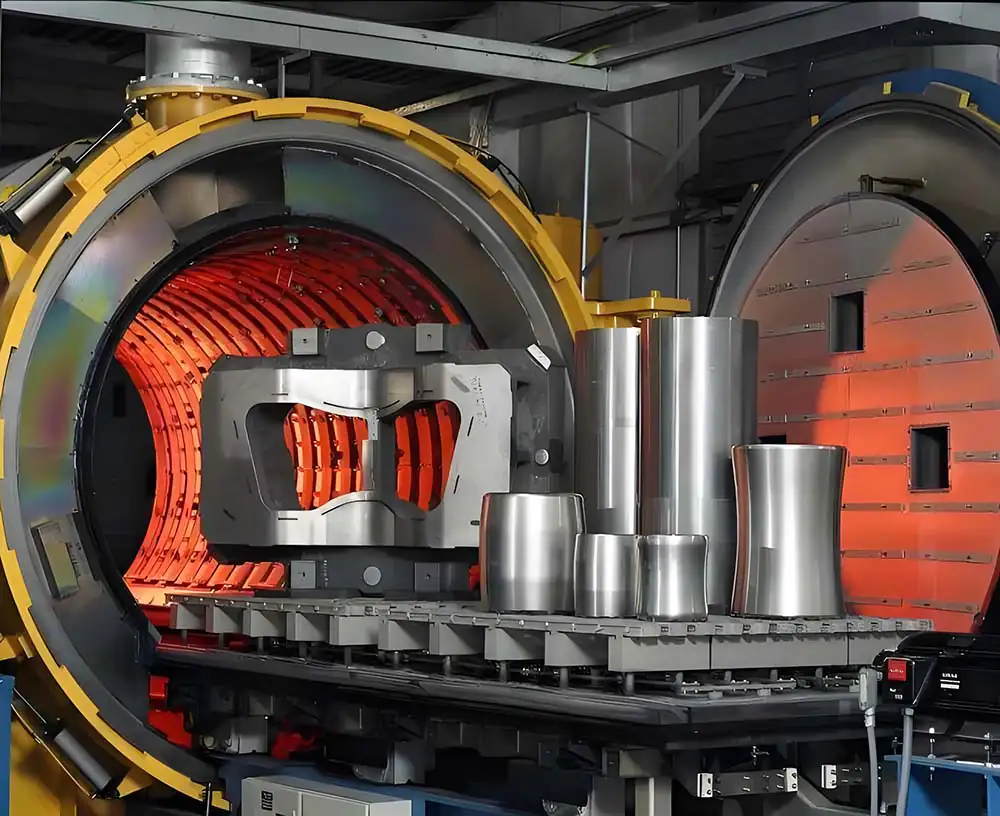
Précautions pour le traitement thermique des moules de coulée sous pression :
Le traitement thermique pour la durée de vie du moule de coulée sous pression a une grande influence, selon les informations pertinentes, en raison d'un traitement thermique inadéquat, la défaillance précoce du moule de coulée sous pression a représenté l'ensemble de l'accident du moule de coulée sous pression de 44% ou environ. La trempe de l'acier est la contrainte produite, en fait, c'est le processus de refroidissement de la contrainte thermique et du changement de phase lorsque la contrainte organisationnelle se superpose aux résultats, la trempe de l'acier dans un état de contrainte élevée et de faible ténacité, avec une dureté et une résistance élevées, plus fragile, en fait, ne peut pas être utilisée. La contrainte de trempe est la cause de la fissuration par déformation et entraîne une réduction de la résistance à la fatigue et de la ténacité. C'est pourquoi l'acier doit être trempé après la trempe pour éliminer les contraintes. Stabiliser l'organisation et améliorer la ténacité.
1、 Recuit de détente avant trempe du moule
En raison de l'usinage du moule pour produire une grande contrainte interne, afin d'éviter le traitement thermique avec la génération de l'itération de la contrainte interne, provoquant la déformation et la fissuration du moule, il est nécessaire que le moule dans l'usinage, la trempe avant un traitement de recuit de déstressage. Température de recuit 600 ~ 650 ℃, temps d'isolation en fonction de l'épaisseur de chaque 25mm, calcul de l'isolation 1 heure, isolation avec le refroidissement du four à 300 ℃ (également à froid à 500 ℃) hors de l'air refroidi.
2, le développement d'un processus de traitement thermique raisonnable
A. Le processus de trempe adopte un préchauffage en plusieurs étapes et un contrôle strict de la vitesse d'élévation de la température. L'acier de type 1.2343/44 appartient à la catégorie des aciers fortement alliés à teneur moyenne en carbone, et sa conductivité thermique est moins bonne que celle des aciers faiblement alliés. Par conséquent, le chauffage de trempe doit adopter un préchauffage en plusieurs étapes (2 à 3 étapes) pour 300°C, 650°C et 850°C. L'objectif est d'équilibrer les températures du cœur et de la surface de la pièce, afin de réduire les contraintes thermiques résultant de la différence de température. En même temps, son taux de chauffage doit être mis en œuvre lentement (100 à 200 ℃ / h), afin de réduire les contraintes thermiques générées pendant le processus de chauffage. Dans la phase de chauffage à haute température, on peut utiliser une vitesse de chauffage plus rapide (10 ~ 15 ℃ / h) pour raccourcir le temps de chauffage à haute température afin d'éviter le grossissement du grain ;
B. Prévention de la surchauffe des pièces à usiner
Si la température de l'étape de chauffage dépasse la température normale de trempe (y compris la défaillance de l'instrument ou le placement de la pièce à proximité de l'élément chauffant, etc.), avec l'augmentation de la température de trempe, la prolongation du temps de maintien, les grains sont généralement grossiers, l'organisation de la fragilité augmente, l'augmentation de l'austénite résiduelle, la transformation des carbures globulaires en carbures polygonaux, et un tissu en forme de maille apparaît, le moule est facile à fissurer lors de l'utilisation du processus ;
C. Sélection de l'agent chauffant et de l'agent refroidissant pour la trempe
Dans le monde d'aujourd'hui, les moules de précision complexes et de grande taille utilisent de plus en plus le traitement thermique sous vide ou sous atmosphère protectrice pour éviter la décarburation par oxydation de la surface des moules, en particulier le processus de trempe sous vide et à haute pression, refroidi à l'air, est largement utilisé. Toutefois, il convient de noter que la vitesse de refroidissement de l'air ne peut pas être trop faible, ce qui nécessite la taille de la pression d'azote est suffisante, nécessite généralement la pièce à partir de la température de trempe (1020 ~ 1050 ° C) froid à 538 ° C dans le processus de sa vitesse de refroidissement de surface supérieure ou égale à 28 ° C / min, il y a également une exigence pour la pièce à cœur de la vitesse de refroidissement de plus ou égale à 28 ° C / min. Si la plage de température, la vitesse de refroidissement est trop lente, la trempe de sa microstructure aura des carbures ou d'autres produits de transformation précipités le long des joints de grains, réduisant ainsi la ténacité de l'acier, augmentant la fragilité, la fissuration prématurée dans l'utilisation du processus. En plus de ces conditions, pour les grands moules de coulée sous pression particulièrement complexes, il est possible d'utiliser une trempe isotherme graduelle, ce qui permet de réduire efficacement la déformation du moule et d'éviter les fissures.
D. Processus de trempe
Tremper à temps après la trempe. La trempe de la pièce après refroidissement à 90 ~ 70 ℃ doit être trempée immédiatement, car la pièce après la trempe est dans un état de contrainte élevée, de faible plasticité, et peut facilement provoquer des fissures ; le revenu doit être suffisant. Grand moule de coulée sous pression complexe après la trempe, généralement trois trempes, chaque temps de trempe en fonction de l'épaisseur effective de la pièce tous les 25mm isolation 1 heure de calcul, mais pas moins de 4 heures. L'objectif est de réduire le stress de la transformation organisationnelle et de stabiliser la taille.
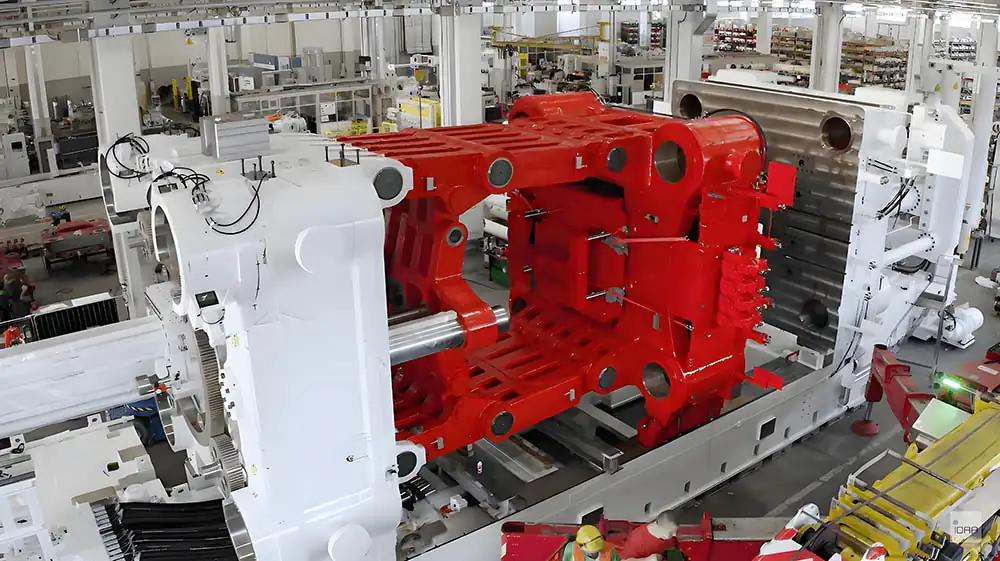
Considérations relatives à la production et à l'entretien des moules de coulée sous pression
1、 Bon préchauffage du moule
L'assemblage du moule après l'essai ou la production normale, doit préchauffer le moule et la température du moule doit être uniforme. La température de préchauffage des moules de coulée sous pression en alliage d'aluminium-magnésium est recommandée entre 250 et 320 ℃, la meilleure utilisation de la température du moule étant le préchauffage par la machine ; le préchauffage du moule à 300 ℃ améliore très rapidement sa résistance aux chocs, mais lorsque la température du moule est inférieure à 200 ℃, la résistance aux chocs du matériau diminue considérablement et la fragilité augmente ; après un bon préchauffage du moule, sa conductivité thermique est supérieure à celle d'un moule non préchauffé, soit près de 20% ; la température de coulée du moule et la température de surface du moule (température de préchauffage) sont très différentes, mais la différence est importante. La température de surface du moule (température de préchauffage) est d'autant plus grande que la différence est importante, que la contrainte thermique est élevée et que la fatigue thermique et la fissuration sont plus probables. Selon les informations de la rédaction de l'association japonaise de moulage sous pression, la température du moule passe de 250 ℃ à 350 ℃, c'est-à-dire que la différence entre la température de coulée et la température de surface du moule est réduite de 100 ℃, ce qui permet d'améliorer la durée de vie du moule de près de 10 fois.
2、 Formuler le processus de coulée correct
La température de coulée doit être raisonnable, pas trop élevée. Si la température de coulée est trop élevée, la fluidité est meilleure, mais le temps de condensation de la coulée est long, il est facile de produire des trous de retrait, des trous d'air, de réduire la dureté de la surface du moule, il y a un moule collant, ce qui produit des fissures. Ajuster la force de serrage de la machine de moulage sous pression, de manière à ce que la force du moule soit uniforme. Sélectionnez (ou réglez) correctement la vitesse et la pression de remplissage. Une vitesse de remplissage (vitesse d'éjection) trop élevée augmentera la surface de la cavité en raison de l'érosion et du risque d'endommagement du moule collant ; une vitesse de remplissage trop faible, bien que propice à l'évacuation des gaz, entraînera une détérioration des propriétés mécaniques et de la qualité de la surface de la pièce moulée. De même, l'augmentation de la pression de remplissage augmentera également la vitesse de remplissage de la buse. En résumé, il convient d'ajuster une valeur modérée.
3、 Fermer l'eau de refroidissement pendant la production
Lors de l'interruption de l'opération de coulée sous pression, n'oubliez pas de fermer l'eau de refroidissement, afin d'éviter que la température du moule ne baisse trop, ce qui, lors de la reprise de l'opération de coulée, affecterait la qualité des pièces coulées et la durée de vie du moule.
4、 Sélection d'un agent de démoulage approprié et d'une méthode de pulvérisation correcte
Le rôle principal de l'agent de démoulage est d'éviter l'adhérence du liquide métallique à la surface de la cavité et de garantir la séparation entre la pièce moulée et la paroi, ce qui prolonge la durée de vie du moule. L'agent de démoulage est composé d'eau, d'huile et, depuis quelques années, de poudre et de granulés. Exigences : l'agent de démoulage ne doit pas avoir d'effet négatif sur la qualité de la surface de la pièce moulée, ne doit pas dégager d'odeur de fumée et ne doit pas laisser de résidus. La concentration de l'agent de démoulage doit être appropriée, il faut le remuer souvent, ne jamais le laisser précipiter, sinon la cavité du moule sera extrêmement froide en raison des fissures dues à la fatigue thermique. La quantité pulvérisée doit être moindre, la pulvérisation doit être uniforme, la formation du film doit être fine. Une pulvérisation trop importante et trop épaisse entraînera un relâchement des pièces coulées, des scories, des boursouflures, des porosités et d'autres défauts. Si l'effet de pulvérisation de l'agent de démoulage à base d'eau n'est pas bon, vous devriez choisir un agent de démoulage à base d'huile ou un agent de démoulage à base de poudre. Toutefois, il doit être utilisé sous vide. Le démoulage est rapide, la productivité est élevée, la qualité est bonne et le moule produit moins de contraintes thermiques, ce qui contribue à prolonger la durée de vie du moule.
5. s'assurer que la qualité de l'alliage d'aluminium moulé garantit la composition de l'alliage d'aluminium ;
La fusion des alliages d'aluminium et le réservoir de stockage doivent être séparés. La fusion centrale doit contrôler strictement la teneur en gaz tels que les oxydes, éviter absolument les déchets et les matériaux de retour au four directement ajoutés au four de maintien, sinon ils contamineront la solution métallique, ce qui non seulement réduira sérieusement la qualité des pièces moulées, mais provoquera également facilement le collage et la corrosion du moule. La teneur en Fe de la solution d'alliage d'aluminium doit être contrôlée entre 0,7 ~ 1,3%, si elle est inférieure à 0,7%, il est facile de provoquer le phénomène de collage au moule, si elle est supérieure à 1,3%, il se forme un point dur dans le composé métallique, ce qui entraîne l'érosion.
6、 Mettre en place un bon système d'entretien des moules, de manière à ce qu'ils soient en bon état de fonctionnement :
A. Nettoyer et nettoyer le moule en temps voulu, éliminer les résidus de la cavité et le bord volant ; B. Remplacer ou réparer les pièces endommagées ; C. Traiter régulièrement le moule pour le soulager des contraintes : le premier traitement de soulagement des contraintes pour la mise en service initiale du moule doit utiliser environ 2000 ~ 5000 moules ; le deuxième traitement de soulagement des contraintes pour l'utilisation de 10.000 ~ 20.000 moules ; le reste de l'intervalle entre chaque traitement de soulagement des contraintes, le même que ci-dessus, le maximum ne peut pas dépasser 15.000 moules. D. Après un certain temps d'utilisation du moule, la dureté de la surface du moule diminue et le phénomène de collage des moules apparaît. La surface du moule doit être polie et un traitement de nitruration doit être effectué avec une épaisseur de couche de nitruration de 0,08-0,12 mm, ou un traitement composite de nitruration + oxydation, ce qui améliorera efficacement la durée de vie du moule.