铝挤压 vs 铝压铸有什么区别
发布时间:2025-04-23 分类:新闻 浏览量:20
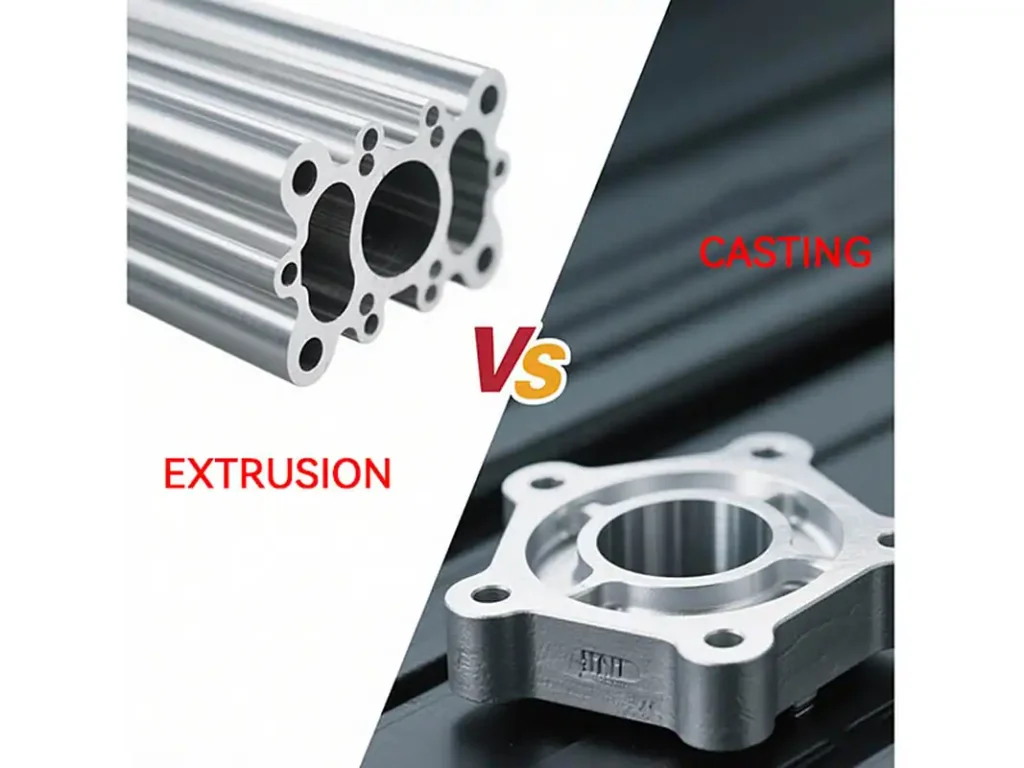
在工业制造领域,铝材因其轻量化、耐腐蚀和高强度特性,成为汽车、电子、建筑等行业的首选材料。然而,铝挤压(Aluminum Extrusion)与铝压铸(Aluminum Die Casting)两种工艺的核心差异,直接影响生产成本、结构精度和量产效率。作为深耕铝压铸领域20年的技术专家,宁波贺鑫压铸厂通过本文解析两大工艺的工程逻辑,并分享如何通过精密压铸技术为客户降本增效。
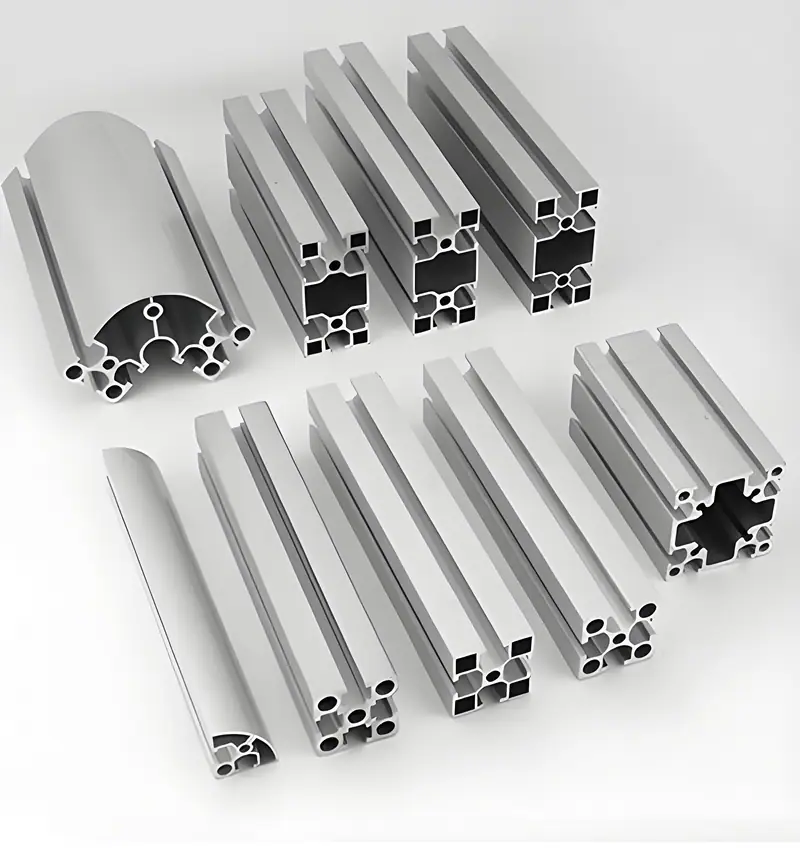
成型原理的本质对比
(材料流动方式的根本差异)
铝挤压工艺通过高达15000吨的液压压力,迫使加热至400-500℃的铝锭通过特制模具孔洞,这种连续的塑性变形过程类似"挤牙膏"原理。金属在固态下完成形状重塑,保持了铝材原有的晶粒结构连续性。相比之下,铝压铸采用680-720℃的液态铝汤,在800-1200bar高压下以30-100m/s的速度注入钢模腔体,通过急速冷却(冷却速率可达1000℃/秒)实现凝固成型。
这种物理状态的差异导致产品性能产生根本区别:挤压件具有各向异性力学特征,沿挤压方向强度提升20-30%;压铸件则因快速凝固形成细晶组织,但存在3-5%的孔隙率缺陷。从微观结构看,挤压铝材晶粒被拉长形成纤维状组织,压铸件呈现枝晶间共晶相的网状结构。
设备体系的工艺对决
(从熔炉到成品的全流程对比)
挤压生产线核心设备包含长棒加热炉、挤压筒、模具温控系统及牵引机,设备投资约200-500万美元。典型挤压速度为5-50米/分钟,模具寿命可达50-100吨产量。压铸系统则由熔炼炉、压射单元、合模机构组成,冷室压铸机锁模力范围800-5000吨,设备成本300-800万美元,模具寿命约10-20万模次。
在能源消耗方面,挤压吨铝耗电约500-800kWh,主要能耗集中在塑性变形过程;压铸吨铝耗电达800-1200kWh,其中60%能耗用于金属熔化和模具温控。环保表现上,挤压工艺的废料回收率可达95%以上,而压铸因汤口料和废品率(约5-15%)产生更多需回炉的废料。
产品特性的应用分析
(从智能手机到航天器的选择逻辑)
挤压工艺擅长生产截面恒定的线性构件,典型壁厚1.5-25mm,表面粗糙度Ra0.8-3.2μm。在建筑幕墙领域,6063-T5合金挤压型材占比超过80%;轨道交通车厢的整体挤压地板长度可达26米。压铸件则适合复杂三维造型,最小壁厚可达0.6mm,表面Ra1.6-6.3μm,汽车发动机缸体常用A380压铸,集成30余个功能结构于一体。
在力学性能方面,挤压T6态铝合金抗拉强度可达350MPa,适合结构承重件;压铸ADC12合金典型强度280MPa,更注重形状复杂性。新兴的真空压铸技术可将铸件延伸率提升至10%以上,正在改变传统压铸件脆性大的认知。
选择工艺时需综合考量:月产量5万件以下建议挤压(模具成本低至1万美元),大批量生产选压铸(虽然模具费达5-20万美元,但单件成本可降低60%)。对于需要阳极氧化的电子产品外壳,优先选用杂质含量更低的挤压6063合金;而汽车变速箱壳体因复杂油道设计,必然选择压铸工艺。随着混合动力技术的普及,集成化压铸车身件正引发汽车制造革命,特斯拉Model Y后底板采用6000吨压铸机,将70个零件整合为1个。