机加工基础知识
发布时间:2025-02-27 分类:新闻 浏览量:150
机械加工
机械 加工 作为现代制造业的核心技术,通过车床、铣床、磨床等专业设备对金属、塑料等工件进行切削、磨削、钻孔等多道工序,精确调控零件的几何形状、结构尺寸与表面光洁度,确保从汽车发动机部件到航空航天精密零件的全领域制造需求。随着数控技术与自动化生产线的深度整合,加工流程实现了从传统人工操作向智能化编程控制的转型升级,在提升加工效率的同时有效控制生产成本。严格遵循国际标准的质量控制体系,通过实时监测刀具磨损状态与加工参数优化,保障批量生产中的工艺稳定性。当前工业4.0趋势下,机械加工正朝着柔性化生产与数字化管理方向演进,为复杂零部件的定制化需求提供可靠解决方案。
数控加工
数控加工依托计算机编程精确控制机床运动轨迹,通过自动化执行车削、铣削、镗孔等精密加工工序,将金属、工程塑料等原材料高效转化为符合设计规范的复杂零部件。其核心优势在于数字化指令驱动的高重复精度与多轴联动能力,可适应从医疗器械微型元件到能源装备大型结构件的全尺度制造需求。现代智能工厂通过集成CAM编程系统与在线检测装置,实现加工参数动态优化与刀具寿命智能预测,在提升航空航天、汽车模具等高端领域加工效率的同时,确保批量生产中的尺寸一致性。随着物联网技术与数字孪生模型的深度应用,数控加工正加速向云端协同制造与自适应工艺调整方向演进,为智能制造生态提供关键技术支撑。
机加工的分类
车削加工
通过车床主轴驱动工件旋转,结合刀具的径向/轴向进给运动,专精于轴类、盘套类等回转体零件的内外圆加工,在汽车传动轴、液压缸筒等批量生产中展现高效切削优势,可处理碳钢、 铝合金 到高温合金的多种材料,数控车床更可实现螺纹车削与偏心结构的精密加工。
铣削加工
运用立式/卧式铣床的多刃刀具旋转切削,胜任复杂型腔、三维曲面的成型加工,从模具镶块的分型面到机器人关节的连接槽皆为其典型应用场景,五轴联动数控铣削技术突破空间角度限制,在叶轮、螺旋桨等异形件加工领域具有不可替代性。
磨削加工
采用砂轮微粒进行微米级材料去除,是淬硬钢、陶瓷等超硬材料获得镜面精度的终极工艺,精密主轴制造中的轴承滚道与医疗器械人工关节的表面处理均依赖此技术,通过在线测量系统与恒温车间的环境控制,确保亚微米级尺寸稳定性。
钻孔、铰孔、攻丝等加工
涵盖从基础通孔加工到精密螺纹成型的完整孔系解决方案,深孔钻削技术满足枪钻、油气管道等特殊长径比需求,复合刀具的应用使钻铰攻工序一次装夹完成,大幅提升发动机缸体、液压阀块等多孔系零件的加工效率。也常用于 压铸模具 制造。
机加工设备
车床
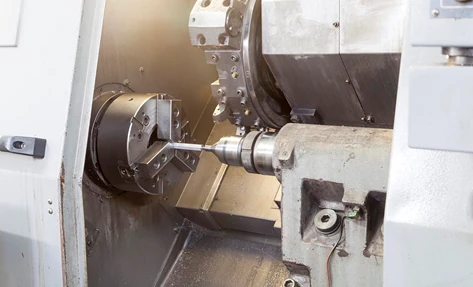
作为回转体加工的核心装备,车床通过主轴驱动棒料或盘类工件高速旋转,配合刀塔的径向/轴向复合进给运动,精准完成外圆车削、端面切削及螺纹加工。现代数控车床集成动力刀具与Y轴功能,可对不锈钢、钛合金等难切削材料进行车铣复合加工,广泛应用于汽车凸轮轴、液压阀芯等精密零件的批量生产,其双主轴设计更可实现自动化连续加工。
铣床
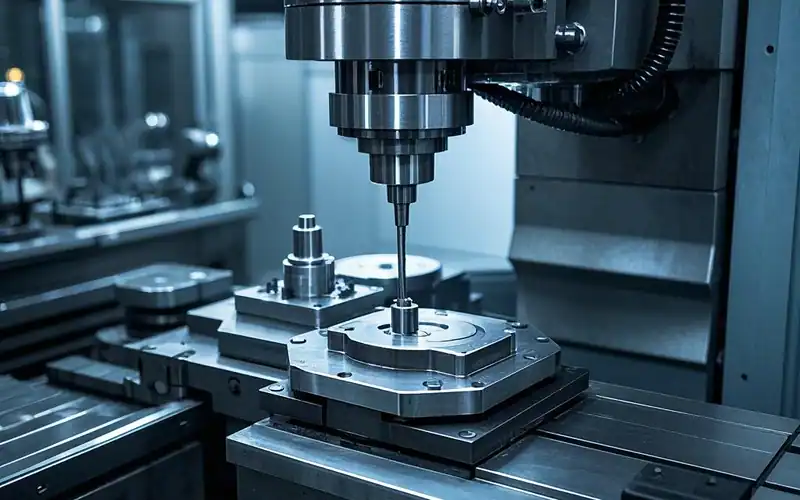
凭借多轴联动的空间加工能力,铣床借助立式/卧式主轴驱动面铣刀、球头刀等刀具实现复杂型面成型,五轴数控铣床通过工作台摆动突破空间角度限制,在航空发动机叶片、注塑模具镶件的三维曲面加工中展现不可替代性。配备自动换刀系统的加工中心,可一次性完成铝合金框架件从粗加工到精铣的完整工艺流程。
钻床
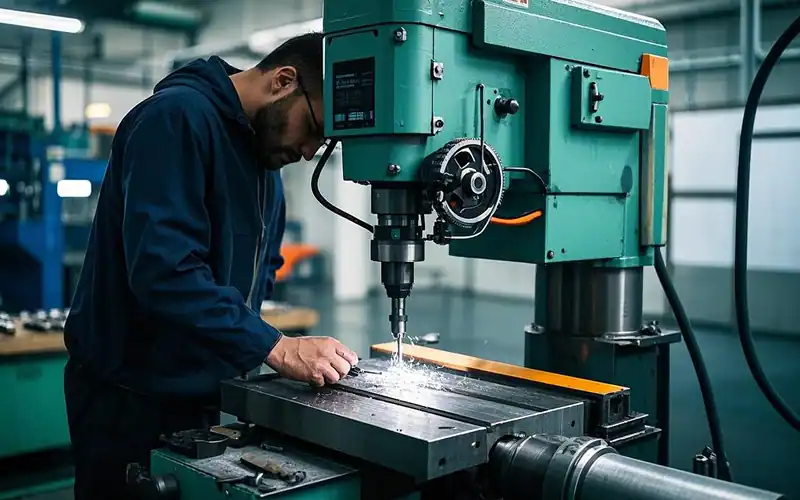
深孔加工领域的专业解决方案提供者,钻床通过高速主轴驱动麻花钻、深孔钻等刀具实现精准孔系加工,枪钻技术配合高压冷却系统可完成长径比超过30:1的深孔钻削。智能钻削中心集成铰孔、镗孔工艺模块,满足能源设备管板、汽车变速箱壳体等多规格孔系的高效加工需求,配备激光对刀仪实现钻头磨损实时补偿。
磨床
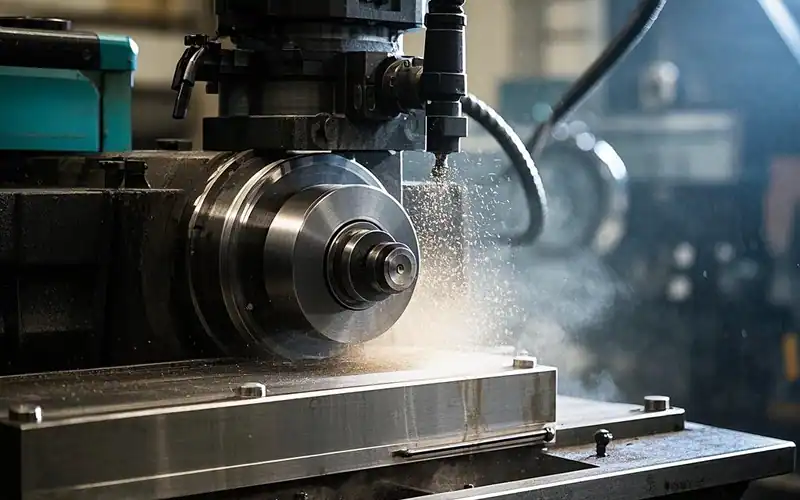
精密制造的最后一道质量防线,磨床采用CBN砂轮或金刚石砂轮对淬硬钢、硬质合金等超硬材料进行纳米级精度修整,数控成型磨床通过闭环反馈系统可稳定保持轴承滚道、丝杠螺纹的微米级轮廓精度。配备在线测量系统的无心磨床,为光学仪器导柱、液压阀芯等大批量高精度零件提供全自动磨削方案,恒温车间的环境控制确保加工稳定性。
其他机加工设备
数控机床
作为智能制造的核心载体,数控机床通过多轴联动与CAM编程系统的无缝对接,将复杂零件的三维建模数据直接转化为精密加工指令,在航空航天钛合金结构件、医疗器械植入体的多工序集成加工中展现技术优势。配备自适应控制系统的智能机床可实时感知切削力波动与刀具磨损状态,结合工业物联网平台实现加工参数的云端优化迭代,为汽车模具、光学器件等精密制造领域提供柔性化生产解决方案。
激光切割机
依托高功率光纤激光器与振镜定位技术,激光切割机以非接触式加工实现不锈钢、铝合金等金属板材的微米级精密切割,其智能监控系统可自动识别碳钢氧化层并调整焦点位置,在新能源汽车电池托盘、电子元件散热片的加工中显著提升效率。万瓦级激光切割设备突破厚板切割瓶颈,配合自动上下料机械臂,为工程机械、船舶制造行业提供全天候连续作业能力,热影响区控制技术有效保障精密零件的后续焊接质量。
水切割机
采用超高压水射流混合石榴砂的冷态切割工艺,水切割机凭借无热变形的独特优势,在碳纤维复合材料、大理石异形装饰件的加工中保持材料原生性能。五轴动态切割头通过空间角度补偿技术,实现涡轮叶片陶瓷涂层、食品级塑料容器的三维轮廓精准分离,其环保特性彻底消除传统切割产生的粉尘污染,在医疗耗材、建筑幕墙行业的高标准加工场景中成为首选工艺。
机加工工艺
切削原理
切削原理:切削运动是刀具与工件之间的相对运动,包括主运动和进给运动。
切削速度:切削速度是指刀具切削刃上选定点相对于工件待加工表面在主运动方向上的瞬时速度。
切削深度:切削深度是指待加工表面与己加工表面之间的垂直距离。
切削刀具
刀具材料:常用的刀具材料包括高速钢、硬质合金、陶瓷和超硬材料等。
刀具几何参数:刀具的几何参数包括前角、后角、主偏角、刃倾角等,对切削力、切削热、耐用度和工件表面质量等方面都有影响。
刀具的刃磨:刀具的刃磨包括砂轮的选择、刃磨工艺和刃磨质量的检测等。
切削液
切削液的作用:切削液的作用包括冷却、润滑、清洗和防锈等。
切削液的种类:切削液的种类包括乳化液、合成液和切削油等。
切削液的选用:切削液的选用应根据加工要求、工件材料和刀具材料等因素进行选择。
机加工工艺流程
毛坯准备
基于零件力学性能要求,通过铸造、锻造或3D打印制备近净成形毛坯,针对钛合金航空结构件采用热等静压工艺消除内部缺陷,铝合金压铸毛坯需经X射线探伤确保气孔率<0.2%。智能制造车间通过MES系统自动匹配毛坯批次与加工订单,实现从原料入库到粗加工的全流程追溯。
工件定位
运用六点定位原理设计模块化夹具系统,液压膨胀芯轴确保薄壁筒类零件0.005mm径向跳动精度,五面体真空吸盘为异形复合材料提供无损装夹方案。针对新能源汽车电机壳体加工,采用激光扫描与自适应夹紧力控制技术,补偿毛坯尺寸波动对定位基准的影响。
刀具准备
基于切削仿真数据预判刀具寿命,PVD涂层硬质合金刀具应对高温合金断续切削,金刚石镀膜钻头实现碳纤维复合材料无毛刺加工。智能刀库通过RFID芯片自动识别刀具参数,在加工中心换刀过程中同步校准刀具补偿值,确保汽车模具型腔加工的尺寸一致性。
切削加工
多轴联动数控机床执行全序加工策略,车铣复合中心对航空发动机机匣一次装夹完成内外型面加工,微润滑技术使Inconel 718材料的切削效率提升40%。五轴加工中心通过摆线铣削工艺将深槽加工刀具寿命延长3倍,配合在线测量系统实时修正刀具路径偏差。
工件检测
三坐标测量机(CMM)构建数字化检测闭环,蓝光扫描仪捕捉涡轮叶片叶型轮廓偏差,工业CT无损检测铝合金铸件内部缩孔。SPC系统统计分析关键尺寸CPK值,AI视觉检测表面缺陷识别精度达99.7%,检测数据自动上传QMS系统生成电子化质量档案。
机加工质量控制
机加工误差分析
原始误差:与机床、夹具、刀具和工件本身有关,如制造和装配误差。
加工误差:由于加工过程中各种因素引起的误差,如切削力、切削热、刀具磨损等。
检测误差:在测量过程中由于测量设备、测量方法、测量环境等因素引起的误差。
质量控制方法
预防控制:通过设计和工艺控制减少误差,提高产品质量。
过程控制:通过实时监测和调整加工过程,确保产品质量稳定。
成品检验:对成品进行检验和测试,确保产品符合规定要求。
机加工表面质量
表面粗糙度:表面微观不平度的高度,影响零件的耐磨性和疲劳强度。
表面波纹度:表面波纹的形状和尺寸,影响零件的疲劳强度和密封性。
表面加工纹理:表面加工留下的痕迹和纹理,影响零件的外观和配合精度。
机加工尺寸精度控制
加工尺寸精度:加工后零件的实际尺寸与规定尺寸的符合程度。
定位精度:加工过程中工件相对于机床的定位精度,影响零件的装配精度。
重复定位精度:机床在相同条件下重复定位的精度,反映机床的稳定性和可靠性。
开始定制机加工零件
宁波贺鑫为复杂零部件提供一站式数控加工解决方案,提供从快速原型到批量生产的全周期精密机加工服务,依托五轴联动加工中心、车铣复合设备集群及瑞士宝美超精密机床,专精于汽车零部件等产品生产。立即上传图纸至智能报价系统,获取含DFM优化方案与刀具损耗分析的精算报告。联系我们
加工设备安全操作规程
设备启动前检查
验证液压系统压力稳定性(20-25MPa)与气压管路密封性,使用红外热像仪检测主轴电机绕组温度异常,核对数控系统软限位与硬限位双重保护设置。针对五轴加工中心需额外校验转台锁紧机构,激光干涉仪检测导轨定位精度误差≤0.02mm,确保碳钢工件夹持时磁性吸盘的剩磁强度≤5高斯。
设备操作规程
严格执行SOP参数设定规范:铸铁粗铣切削速度限制在150-220m/min,硬质合金刀具进给率按ap=2mm×ae=35mm梯度调整。加工钛合金时必须启动微量润滑(MQL)系统并监测切削区烟雾浓度,操作人员需穿戴抗冲击面罩与阻燃服,遇主轴过载报警立即触发紧急制动按钮。
设备停机后保养
闭环清理切削液槽金属碎屑并检测pH值(8.5-9.2),使用超声波清洗机去除刀柄锥面微米级油膜残留。每月执行滚珠丝杠反向间隙补偿(C3级精度丝杠补偿量≤0.015mm),通过振动频谱分析预判主轴轴承寿命,润滑脂加注量精确至±0.5ml。
机加工事故案例分析
事故案例一
某汽配厂数控车床主轴过热起火:操作员违规关闭冷却液进行不锈钢连续车削,切削温度突破900℃引燃油雾。事故后强制加装热成像监测系统,并在PLC中植入切削热力学模型,实现温度-转速联动控制。
事故案例二
龙门铣床防护门联锁失效致残:设备改造时屏蔽安全光栅信号,铁屑飞溅击穿5mm亚克力挡板。整改方案升级为IP67防护等级的压力感应地垫与双回路光栅,触发响应时间≤0.3秒。
机加工发展趋势与挑战
机加工技术发展趋势
- 数字孪生驱动:机床状态实时映射云端,加工误差预测准确率达99.2%
- 复合加工革命:车铣镗磨一体化设备减少装夹次数,叶轮加工周期缩短60%
- 绿色制造:氢能源切削技术替代乳化液,碳足迹降低45%
机加工产业面临的挑战
- 高技能人才断层:五轴编程技师缺口达37%,需AR远程指导系统补位
- 超硬材料加工瓶颈:碳化硅镜面加工刀具寿命仅15分钟,亟待等离子辅助切削技术突破
- 数据安全风险:CNC系统漏洞导致G代码被篡改,需区块链加密传输
机加工技术发展前景展望
量子测量技术将尺寸检测精度推进至纳米级,AI自进化算法使切削参数动态优化效率提升300%。到2030年,基于脑机接口的机床手势控制、零排放干式加工中心将成为高端制造标配,微型工厂模式重构航空航天供应链。