砂型铸造工艺
发布时间:2024-10-08 分类:新闻 浏览量:1999
什么是砂铸造?
砂铸 ,也被称为砂型铸造,是一种历史悠久的铸造工艺方法,其应用范围广泛,遍布全球各地。用粘土粘结砂(或其他材料如石膏、硅树脂等制成的砂型)作为造型材料来生产铸件的工艺方法。其原理是利用砂型的柔软和易于成型的特点,将熔化的金属倒入砂型中,待金属凝固后,破碎砂型以得到所需的铸件。应用在各种金属中,常见的有铝砂铸造,铁砂铸造,铜砂铸造,现在让位于中国的铝合金铸造工厂宁波贺鑫为大家详解下砂铸造工艺.
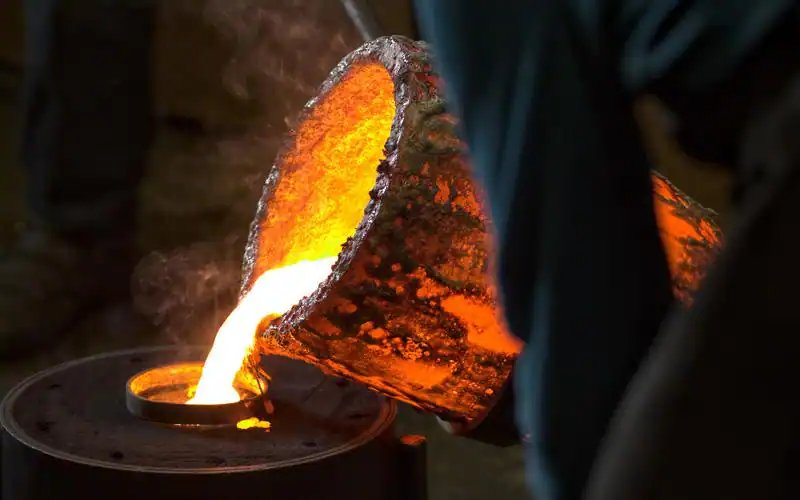
砂型铸造生产常规工艺流程
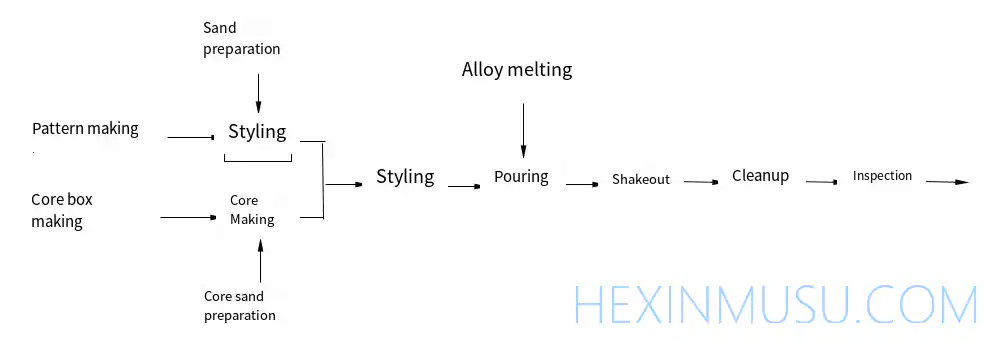
砂型铸造工艺
(1) 型砂和芯砂的制备
砂型铸造用的造型材料主要是用于制造砂型的型砂和用于制造砂芯的芯砂。通常型砂是由原砂(山砂或河砂)、粘土和水按一定比例混合而成,其中粘土约为9%,水约为6%,其余为原砂。有时还加入少量如煤粉、植物油、木屑等附加物以提高型砂和芯砂的性能。紧实后的型砂结构如图所示。
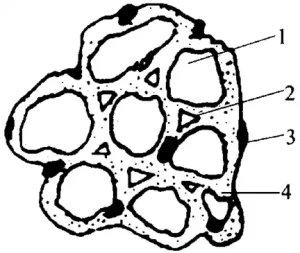
型砂结构示意图 1-砂粒 2-空隙
3-附加物 4-粘土膜
芯砂由于需求量少,一般用手工配制。
型芯所处的环境恶劣,所以芯砂性能要求比型砂高,同时芯砂的粘结剂(粘土、油类等)比型砂中的粘结剂的比重要大一些,所以其透气性不及型砂,制芯时要做出透气道(孔);为改善型芯的退让性,要加入木屑等附加物。
有些要求高的小型铸件往往采用油砂芯(桐油+砂子,经烘烤至黄褐色而成)。
(2)型砂的性能
型砂的质量直接影响铸件的质量,型砂质量差会使砂铸造产品产生气孔、砂眼、粘砂、夹砂等缺陷。良好的型砂应具备下列性能:
- ①透气性 型砂能让气体透过的性能称为透气性。高温金属液浇入铸型后,型内充满大量气体,这些气体必须由铸型内顺利排出去,否则将使铸件产生气孔、浇不足等缺陷。铸型的透气性受砂的粒度、粘土含量、水分含量及砂型紧实度等因素的影响。砂的粒度越细,粘土及水分含量越高,砂型紧实度越高,透气性则越差。
- ②强度 型砂抵抗外力破坏的能力称为强度。型砂必须具备足够高的强度才能在造型、搬运、合箱过程中不引起塌陷,浇注时也不会破坏铸型表面。型砂的强度也不宜过高,否则会因透气性、退让性的下降使铸件产生缺陷。
- ③耐火性 指型砂抵抗高温热作用的能力。耐火性差,铸件易产生粘砂。型砂中SiO2含量越多,型砂颗粒就越大,耐火性越好。
- ④可塑性 指型砂在外力作用下变形,去除外力后能完整地保持已有形状的能力。可塑性好,造型操作方便,制成的砂型形状准确、轮廓清晰。
- ⑤退让性 指铸件在冷凝时,型砂可被压缩的能力。退让性不好,铸件易产生内应力或开裂。型砂越紧实,退让性越差。在型砂中加入木屑等物可以提高退让性
在单件小批生产的砂铸造产品供应商的车间里,常用手捏法来粗略判断型砂的某些性能,如用手抓起一把型砂,紧捏时感到柔软容易变形;放开后砂团不松散、不粘手,并且手印清晰;把它折断时,断面平整均匀并没有碎裂现象,同时感到具有一定强度,就认为型砂具有了合适的性能要求,如图所示。
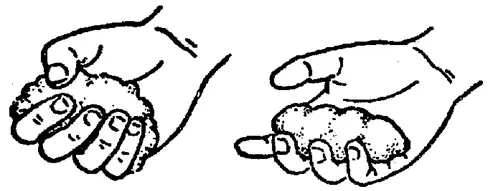
型砂湿度适当时 手放开后可看出
可用手捏成砂团 清晰的手纹
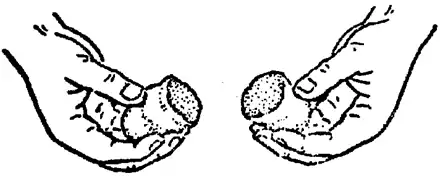
折断时断隙设有碎裂状
同时有足够的强度
(3)模具的组成
砂铸造产品的模具是根据零件形状用造型材料制成的,模具可以是砂型,也可以是金属型。砂型是由型砂(型芯砂)做造型材料制成的。它是用于浇注金属液,以获得形状、尺寸和质量符合要求的铸件。
模具一般由上型、下型、型芯、型腔和浇注系统组成,如右图所示。
模具组元间的接合面称为分型面。铸型中造型材料所包围的空腔部分,即形成铸件本体的空腔称为型腔。液态金属通过浇注系统流入并充满型腔,产生的气体从出气口等处排出砂型。
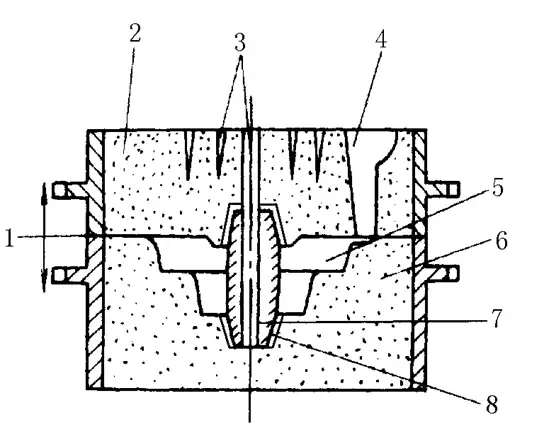
1-分型面 2-上型 3-出气孔4-浇注系统 5-型腔 6-下型
7-型芯 8-芯头芯座
(4)浇冒口系统
- 浇注系统 浇注系统是为金属液流入型腔而开设于铸型中的一系列通道。其作用是:
①平稳、迅速地注入金属液;
②阻止熔渣、砂粒等进入型腔;
③调节铸件各部分温度,补充金属液在冷却和凝固时的体积收缩。
正确地设置浇注系统,对保证铸件质量、降低金属的消耗量有重要的意义。若浇注系统不合理,铸件易产生冲砂、砂眼、渣孔、浇不到、气孔和缩孔等缺陷。典型的浇注系统由外浇口、直浇道、横浇道和内浇道四部分组成,如下图所示。
对形状简单的小铸件可以省略横浇道。
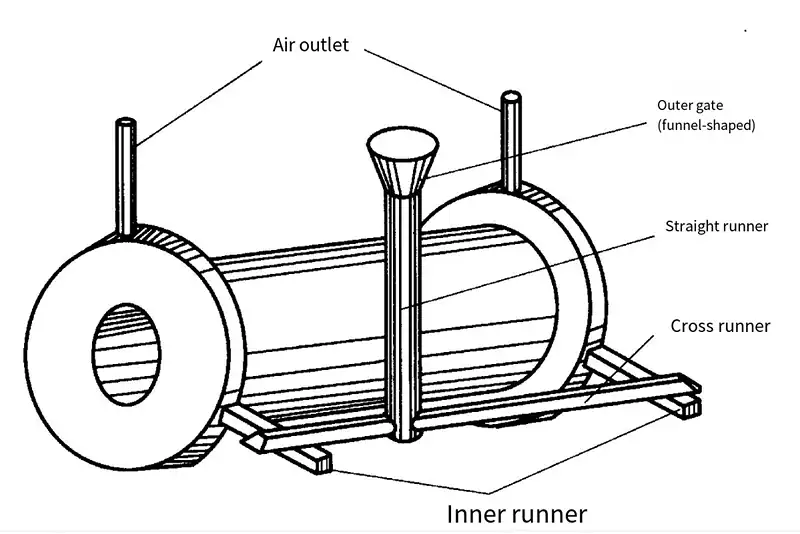
典型浇注系统
- ① 外浇口 其作用是容纳注入的金属液并缓解液态金属对砂型的冲击。小型铸件通常为漏斗状(称浇口杯),较大型铸件为盆状(称浇口盆)。
- ② 直浇道 它是连接外浇口与横浇道的垂直通道。改变直浇道的高度可以改变金属液的静压力大小和改变金属液的流动速度,从而改变液态金属的充型能力。如果直浇道的高度或直径太大,会使铸件产生浇不足的现象。为便于取出直浇道棒,直浇道一般做成上大下小的圆锥形。
- ③ 横浇道 它是将直浇道的金属液引入内浇道的水平通道,一般开设在砂型的分型面上,其截面形状一般是高梯形,并位于内浇道的上面。横浇道的主要作用是分配金属液进入内浇道和起挡渣作用。
- ④ 内浇道 它是直接与型腔相连,并能调节金属液流入型腔的方向和速度、调节铸件各部分的冷却速度。内浇道的截面形状一般是扁梯形和月牙形,也可为三角形。
- 冒口 常见的缩孔、缩松等缺陷是由于铸件冷却凝固时体积收缩而产生的。为防止缩孔和缩松,往往在铸件的顶部或厚实部位设置冒口。冒口是指在铸型内特设的空腔及注入该空腔的金属。冒口中的金属液可不断地补充铸件的收缩,从而使铸件避免出现缩孔、缩松。冒口是多余部分,清理时要切除掉。冒口除了补缩作用外,还有排气和集渣的作用。
(5)模样和芯盒的制造
模样是铸造生产中必要的工艺装备。对具有内腔的铸件,铸造时内腔由砂芯形成,因此还要制备造砂芯用的芯盒。制造模样和芯盒常用的材料有木材、金属和塑料。在单件、小批量生产时广泛采用木质模样和芯盒,在大批量生产时多采用金属或塑料模样、芯盒。金属模样与芯盒的使用寿命长达10万~30万次,塑料的使用寿命最多几万次,而木质的仅1000次左右。为了保证铸件质量,在设计和制造模样和芯盒时,必须先设计出铸造工艺图,然后根据工 艺图的形状和大小,制造模样和芯盒。见下图。
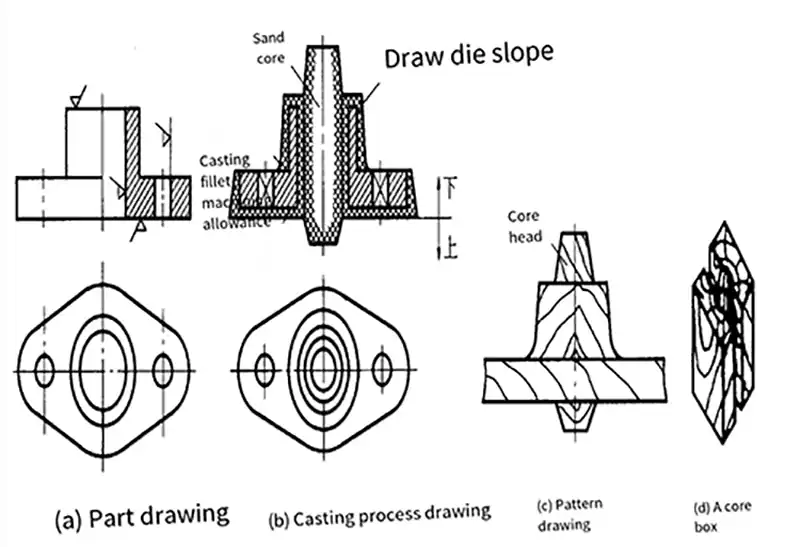
在设计工艺图时,要考虑下列一些问题:
- ① 分型面的选择 分型面是上、下砂型的分界面,选择分型面时必须使模样能从砂型中取出,并使造型方便和有利于保证铸件质量。
- ② 拔模斜度 为了易于从砂型中取出模样,凡垂直于分型面的表面,都做出0.5º~4º的拔模斜度
- ③ 加工余量 铸件需要加工的表面,均需留出适当的加工余量。
- ④ 收缩量 铸件冷却时要收缩,模样的尺寸应考虑铸件收缩的影响。通常用于铸铁件的要加大1%;铸钢件的加大1.5%~2%;铝合金件的加大1%~1.5%。
- ⑤铸造圆角 铸件上各表面的转折处,都要做成过渡性圆角,以利于造型及保证铸件质量。
- ⑥芯头 有砂芯的砂型,必须在模样上做出相应的芯头。
造型方法
造型方法的选择不仅要根据生产类型,而且还要根据工厂设备条件、铸件大小和复杂程度以及质量要求,进行踪合考虑。造型方法可分为手工和机器造型两大类。
手工造型主要用于单件小批生产,机器造型主要用于大批大量生产。
(1).手工造型
- (A) 整模造型的特点是:模样是整体结构,最大截面在模样一端为平面;分型面多为平面;操作简单。整模造型适用于形状简单的铸件,如盘、盖类。
- (B)分模造型的特点是:模样是分开的,模样的分开面(称为分型面)必须是模样的最大截面,以利于起模。分模造型过程与整模造型基本相似,不同的是造上型时增加放上模样和取上半模样两个操作。分模造型适用于形状复杂的铸件,如套筒、管子和阀体等。
- (C)活块模造型模样上可拆卸或能活动的部分叫活块。当模样上有妨碍起模的侧面伸出部分(如小凸台)时,常将该部分做成活块。起模时,先将模样主体取出,再将留在铸型内的活块单独取出,这种方法称为活块模造型。用钉子连接的活块模造型时,应注意先将活块四周的型砂塞紧,然后拔出钉子。
- (D)挖砂造型当铸件按结构特点需要采用分模造型,但由于条件限制(如模样太薄,制模困难)仍做成整模时,为便于起模,下型分型面需挖成曲面或有高低变化的阶梯形状(称不平分型面),这种方法叫挖砂造型。
- (F)三箱造型 用三个砂箱制造铸型的过程称为三箱造型。前述各种造型方法都是使用两个砂箱,操作简便、应用广泛。但有些铸件如两端截面尺寸大于中间截面时,需要用三个砂箱,从两个方向分别起模。
- (G)刮板造型尺寸大于500mm的旋转体铸件,如带轮、飞轮、大齿轮等单件生产时,为节省木材、模样加工时间及费用,可以采用刮板造型。刮板是一块和铸件截面形状相适应的木板。造型时将刮板绕着固定的中心轴旋转,在砂型中刮制出所需的型腔。
- (H) 假箱造型是利用预制的成形底板或假箱来代替挖砂造型中所挖去的型砂
- (I) 地坑造型直接在铸造车间的砂地上或砂坑内造型的方法称为地坑造型。大型铸件单件生产时,为节省砂箱,降低铸型高度,便于浇注操作,多采用地坑造型。地坑造型结构,造型时需考虑浇注时能顺利将地坑中的气体引出地面,常以焦炭、炉渣等透气物料垫底,并用铁管引出气体。
(2).机器造型
手工造型生产率低,铸件表面质量差,要求工人技术水平高,劳动强度大,因此在批量生产中,一般均采用机器造型。机器造型是把造型过程中的主要操作----紧砂与起模实现机械化。根据紧砂和起模方式不同,有气动微震压实造型、射压造型、高压造型、抛砂造型。
- (A)气动微震压实造型是采用振击(频率150~500次/分,振幅25—80mm)——压实——微振(频率700~1000次/分,振幅5~l0mm)紧实型砂的。这种造型机噪音较小,型砂紧实度均匀,生产率高。
- (B)射压造型其特点是利用压缩空气将型砂射入型腔进行初紧实,然后压实活塞将砂型再紧实,砂型推出后,前后两砂型之间的接触面为分型面。射压造型的铸件尺寸精确、表面粗糙度小、生产率高。每小时240-300型,常用于中、小型铸件的大批量生产。
- (C)高压造型是利用液压系统产生很高的压力来压实砂型。其特点是铸件尺寸精确、表面粗糙度小、生产率高。高压造型适用于形状较复杂的中、小型铸件,多品种、中等批量以上的生产。
- (D)抛砂造型是利用高速旋转的叶片将输送带输送过来的型砂高速抛下来紧实砂型。抛砂造型适应性强,不需要专用砂箱和模板,适用于大型铸件的单件小批生产。
制芯
为获得铸件的内腔或局部外形,用芯砂或其他材料制成的、安放在型腔内部的铸型组元称型芯。绝大部分型芯是用芯砂制成的。砂芯的质量主要依靠配制合格的芯砂及采用正确的造芯工艺来保证。
浇注时砂芯受高温液体金属的冲击和包围,因此除要求砂芯具有铸件内腔相应的形状外,还应具有较好的透气性、耐火性、退让性、强度等性能,故要选用杂质少的石英砂和用植物油、水玻璃等粘结剂来配制芯砂,并在砂芯内放入金属芯骨和扎出通气孔以提高强度和透气性。
形状简单的大、中型型芯,可用粘土砂来制造。但对形状复杂和性能要求很高的型芯来说,必须采用特殊粘结剂来配制,如采用油砂、合脂砂和树脂砂等。
另外,型芯砂还应具有一些特殊的性能,如吸湿性要低(以防止合箱后型芯返潮);发气要少(金属浇注后,型芯材料受热而产生的气体应尽量少);出砂性要好(以便于清理时取出型芯)。
型芯一般是用芯盒制成的,其开式芯盒制芯是常用的手工制芯方法,适用于圆形截面的较复杂型芯。
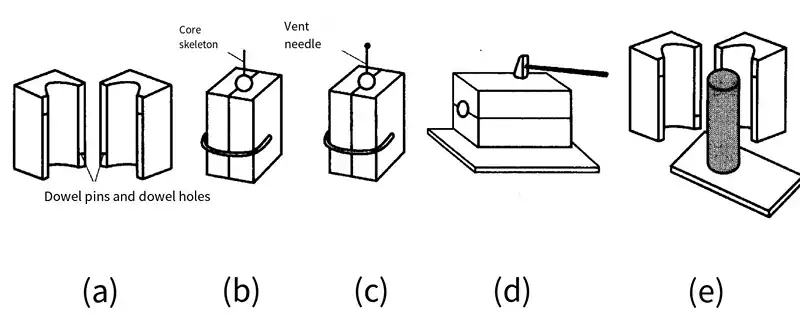
对开式芯盒制芯
(a)准备芯盒 (b)夹紧芯盒,分次加入芯砂、芯骨,舂砂 (c)刮平、扎通气孔 (d)松开夹子,轻敲芯盒 (e)打开芯盒,取出砂芯,上涂料
造型的基本操作
造型方法很多,但每种造型方法大都包括舂砂、起模、修型、合箱工序。
(1) 造型模样
用木材、金属或其它材料制成的铸件原形统称为模样,它是用来形成铸型的型腔。用木材制作的模样称为木模,用金属或塑料制成的模样称为金属模或塑料模。目前大多数工厂使用的是木模。模样的外形与铸件的外形相似,不同的是铸件上如有孔穴,在模样上不仅实心无孔,而且要在相应位置制作出芯头。
(2)造型前的准备工作
- ① 准备造型工具,选择平整的底板和大小适应的砂箱。砂箱选择过大,不仅消耗过多的型砂,而且浪费舂砂工时。砂箱选择过小,则木模周围的型砂舂不紧,在浇注的时候金属液容易从分型面即交界面间流出。通常,木模与砂箱内壁及顶部之间须留有30~100mm的距离,此距离称为吃砂量。吃砂量的具体数值视木模大小而定。
- ② 擦净木模,以免造型时型砂粘在木模上,造成起模时损坏型腔。
- ③ 安放木模时,应注意木模上的斜度方向,不要把它放错。
(3)舂砂
- ① 舂砂时必须分次加入型砂。对小砂箱每次加砂厚约50~70mm。加砂过多舂不紧,而加砂过少又费用工时。第一次加砂时须用手将木模周围的型砂按紧,以免木模在砂箱内的位置移动。然后用舂砂锤的尖头分次舂紧,最后改用舂砂锤的平头舂紧型砂的最上层。
- ② 舂砂应按一定的路线进行。切不可东一下、西一下乱舂,以免各部分松紧不一。
- ③ 舂砂用力大小应该适当。用力过大,砂型太紧,浇注时型腔内的气体跑不出来。用力过小,砂型太松易塌箱。同一砂型各部分的松紧是不同的,靠近砂箱内壁应舂紧,以免塌箱。靠近型腔部分,砂型应稍紧些,以承受液体金属的压力。远离型腔的砂层应适当松些,以利透气。
- ④ 舂砂时应避免舂砂锤撞击木模。一般舂砂锤与木模相距20~40mm,否则易损坏木模。
(4) 撒分型砂
在造上砂型之前,应在分型面上撒一层细粒无粘土的干砂(即分型砂),以防止上、下砂箱粘在一起开不了箱。撒分型砂时,手应距砂箱稍高,一边转圈、一边摆动,使分型砂经指缝缓慢而均匀散落下来,薄薄地复盖在分型面上。最后应将木模上的分型砂吹掉,以免在造上砂型使,分型砂粘到上砂型表面,而在浇注时被液体金属冲下来落入铸件中,使其产生缺陷。
(5)扎通气孔
除了保证型砂有良好的透气性外,还要在已舂紧和刮平的型砂上,用通气针扎出通气孔,以便浇注时气体易于逸出。通气孔要垂直而且均匀分布。
(6)开外浇口
外浇口应挖成60°的锥形,大端直径约60~80mm。浇口面应修光,与直浇道连接处应修成圆弧过渡,以引导液体金属平稳流入砂型。若外浇口挖得太浅而成碟形,则浇注液体金属时会四处飞溅伤人。
(7)做合箱线
若上、下砂箱没有定位销,则应在上、下砂型打开之前,在砂箱壁上作出合箱线。最简单的方法是在箱壁上涂上粉笔灰,然后用划针画出细线。需进炉烘烤的砂箱,则用砂泥粘敷在砂箱壁上,用墁刀袜平后,再刻出线条,称为打泥号。合箱线应位于砂箱壁上两直角边最远处,以保证x和y方向均能定位,并可限制砂型转动。两处合箱线的线数应不相等,以免合箱时弄错。做线完毕,即可开箱起模。
(8)起模
- ① 起模前要用水笔沾些水,刷在木模周围的型砂上,以防止起模时损坏砂型型腔。刷水时应一刷而过,不要使水笔停留在某一处,以免局部水分过多而在浇注时产生大量水蒸汽,使铸件产生气孔缺陷。
- ② 起模针位置要尽量与木模的重心铅锤线重合。起模前,要用小锤轻轻敲打起模针的下部,使木模松动,便于起模。
- ③ 起模时,慢慢将木模垂直提起,待木模即将全部起出时,然后快速取出。起模时注意不要偏斜和摆动。
(9) 修型
起模后,型腔如有损坏,应根据型腔形状和损坏程度,正确使用各种修型工具进行修补。如果型腔损坏较大,可将木模重新放入型腔进行修补,然后再起出。
(10)合箱
合箱是造型的最后一道工序,它对砂型的质量起着重要的作用。合箱前,应仔细检查砂型有无损坏和散砂,浇口是否修光等。如果要下型芯,应先检查型芯是否烘干,有无破损及通气孔是否堵塞等。型芯在砂型中的位置应该准确稳固,以免影响铸件准确度,并避免浇注时被液体金属冲偏。合箱时应注意使上砂箱保持水平下降,并应对准合箱线,防止错箱。合箱后最好用纸或木片盖住浇口,以免砂子或杂物落入浇口中。
铸件浇注位置和分型面的选择
铸件的浇注位置是指浇注时铸件在铸型内所处的位置。
分型面是指两半铸型相互接触的表面。
它们的选择原则主要是保证铸件质量和简化造型工艺。一般情况下,应先选择浇注位置后决定分型面,但在生产中由于浇注位置的选择和分型面的确定有时互相矛盾,必须综合分析各种方案的利弊,选择最佳方案。
(1) .浇注位置的选择原则
- (A)铸件的重要加工面应朝下 气孔、砂眼、夹渣、缩孔容易出现在上表面,而下部的金属液比较纯净,金属的组织比较致密。有时当重要加工面朝下有因难,则应尽量使其处在例面位置。
- (B)铸件的大平面应朝下 由于浇注时的热辐射作用,铸型型腔上表面的型砂容易拱起和开裂,使铸件上表面产生夹砂和夹杂缺陷,所以大平面应朝下。
- (C)铸件薄壁部分应放在下部 薄壁部分易产生浇不足和冷隔,故在下部可增加充型压力,提高金属充型能力。
- (D)应保证铸件实现定向凝固 对于合金收缩大、壁厚不均匀的铸件,应使厚度大的部分置于铸件的最上方或分型面附近,以利于安放冒口,实现定向凝固
- (F)应便于型芯的固定、安装和排气并便于合型
(2).分型面的选择原则
- (A)分型面应选择在模样的最大截面处,以便于取模,挖砂造型时尤其要注意。
- (B)应尽量减少分型面数目,成批量生产时应避免采用三箱造型
- (C)应使铸件全部或大部分在同一砂型内,以减少错箱、飞边和毛刺,提高铸件的精度。
- (D)应尽量减少型芯和活块的数量可以简化造型、造芯工艺,提高生产率。
工艺参数的选择
(1)加工余量
铸件上需要切削加工的表面,应预先留出一定的加工余量,其大小取决于铸造合金的种类、造型方法、铸件大小及加工面在铸型中的位置等诸多因素。铸钢件表面粗糙,变形大,加工余量大;非铁合金表面较光洁,加工余量小;机器造型精度高,加工余量可选小些;单件小批生产时影响因素较多,加工余量要加大;铸件越大、越复杂,加工余量越大;铸型中铸件的顶面比底面和侧面的加工余量大。
单件小批量生产的小铸铁件的加工余量为4.5~5.5mm;小型有色金属铸件加工余量为3mm;灰铸铁件的加工余量值可参阅JB2854—80。
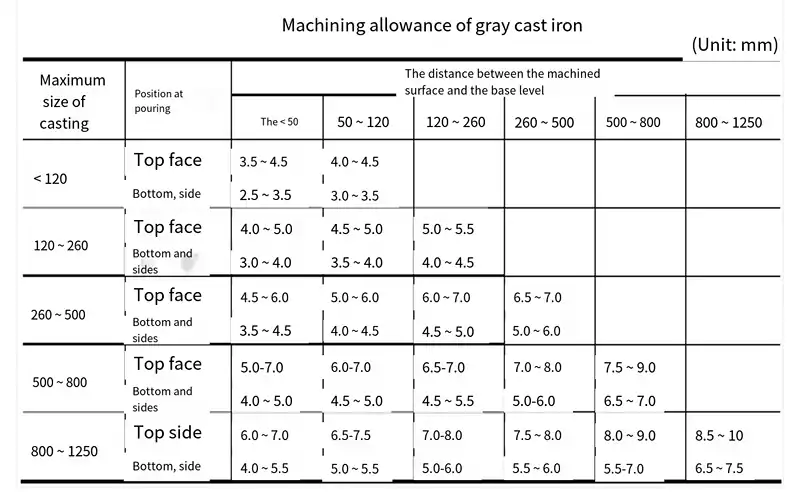
此外,铸钢件上直径小于ф35mm和铸铁件上直径小于ф25mm的孔一般不铸出,留待机械加工更经济方便。对于机器造型的小件,不铸出的孔可以更小些。对于不要求加工的特殊形状、机械加工困难的孔、槽,则必须铸出。
(2)起模斜度
为了使校样便于从铸型中取出,垂直于分型面的立壁上所加的斜度为起模斜度。模样越高,斜度取值越小,内壁斜度比外壁斜度大。手工造型比机器造型的斜度大。模样矮时(≤100mm)为3º左右,模样高时(101~160mm)为0.5°~1°。
(3)铸造圆角
为了防止铸件在壁的连接和拐角处产生应力和裂纹,防止铸型的尖角损坏和产生砂眼,在设计铸件时铸件壁的连接和拐角部分应设计成四角。
(4)型芯头
为了保证型芯在铸型中的定位、固定和排气,模样和型芯都要设计出型芯头。
芯头是型芯的外伸部分,落入铸型的芯座内,起定位和支承型芯的作用。
芯头的形状取决于型芯的型式,芯头必须有足够的高度(h)或长度(l)及合适的斜度,才能使型芯方便、准确和牢固地固定在铸型中,以免型芯在浇注时飘浮、偏斜和移动
(5)收缩余量
由于铸件在浇注后的冷却收缩,制作模样时要加上这部分收缩尺寸。一般灰铸铁的收缩余量为0.8%——1.0%,铸钢为l.8%——2.2%,铸造铝合金为1.0%——1.5%。收缩余量的大小除了与合金种类有关外,还与铸造工艺、铸件在收缩时的受阻情况等有关。
合金种类 | 铸造收缩率 | ||
自由收缩 | 受阻收缩 | ||
灰 铸 铁 | 中小型铸件 | 1.0 | 0.9 |
中大型铸件 | 0.9 | 0.8 | |
特大型铸件 | 0.8 | 0.7 | |
球墨铸铁 | 1.0 | 0.8 | |
碳钢和低合金钢 | 1.6~2.0 | 1.3~1.7 | |
锡青铜 | 1.4 | 1.2 | |
无锡青铜 | 2.0~2.2 | 1.6~1.8 | |
硅黄铜 | 1.7~1.8 | 1.6~1.7 | |
铝硅合金 | 1.0~1.2 | 0.8~1.0 |
砂铸造的优缺点
翻砂铸造优点
- 制造成本低:砂型铸造使用的原材料(如砂、黏土等)成本较低,且制造工艺相对简单,因此制造成本相对较低。
- 制造灵活性高:砂型铸造可以生产各种不同形状和尺寸的铸件,从几克到几吨的零件都能轻松生产,适用性非常强。
- 制造周期短:砂型铸造的工艺流程相对简单,所需烘干和硬化时间较短,因此制造周期相对较短。
- 原材料来源广泛:砂型铸造的原材料来源广泛,砂、黏土等都可以作为造型材料,且价格便宜。
翻砂铸造缺点
- 铸件表面质量一般:砂型铸造的铸件表面质量可能存在一些缺陷,如砂眼、砂洞、粘砂等。
- 砂芯易坍塌:在砂型铸造中,制造复杂形状的铸件可能需要使用砂芯。砂芯容易变形和坍塌,导致不良品率较高。
- 生产效率较低:砂型铸造的生产效率相对较低,因为每个砂型都需要手工制作,铸型只能一次性使用。
- 能耗高且污染排放较严重:砂型铸造在生产过程中能耗较高,且可能产生一定的污染排放,如粉尘、废气等。这可能对环境和工人健康造成一定影响。