数控车床发展史:从基础车削到复杂零件制造的技术革命
发布时间:2025-02-24 分类:新闻 浏览量:611
作为工业文明的活化石,数控车床的演变史映射着人类对精密制造的永恒追求。从公元前1300年埃及工匠用绳索驱动的木质旋床,到21世纪搭载AI算法的五轴智能机床,这项技术始终在重新定义“精度”的边界——工业革命时期蒸汽动力车床将加工误差压缩至0.1mm,而现代数控系统通过光栅尺闭环控制已实现0.001mm的微观把控。尤其在高性能铝合金部件制造领域,数控车床的多轴协同能力彻底改变了传统工艺:以新能源汽车电机壳体为例,其散热齿片与轴承位的复合加工,在集成Y轴动力刀塔的数控系统中可一次性完成,相较传统分序加工效率提升400%,且将同轴度误差控制在5μm以内,这种技术跃迁不仅重构了生产流程,更推动了轻量化设计的工程极限。
数控机床的发展历程
数控机床是用数字代码形式的信息(程序指令),控制刀具按给定的工作程序、运动速度和轨迹进行自动加工的机床,简称数控机床。
时间节点 | 发展事件 | 技术特点 |
1952年 | 美国帕森斯公司与麻省理工学院合作试制出世界上第一台三坐标联动、利用脉冲乘法器原理工作的立式数控铣床 | 数控技术的初步探索,采用电子管控制 |
1954年 | 美国本迪克斯公司生产了世界上第一台工业用数控机床 | 数控机床的工业化应用开始,标志着数控技术的初步成熟 |
1959年 | 数控系统发展到第二代,采用晶体管控制 | 相比电子管,晶体管具有更高的可靠性和稳定性 |
1965年 | 数控系统发展到第三代,采用小规模集成电路控制 | 集成电路的应用提高了数控系统的性能和可靠性 |
1970年 | 第四代数控系统出现,小型计算机开始用于数控系统 | 计算机技术的应用使数控系统具有更高的智能化和自动化水平 |
1974年 | 第五代数控系统出现,微处理器开始用于数控系统 | 微处理器的应用使数控系统更加灵活和高效 |
1970年代末至1980年代初 | 美国、德国、日本等国在数控机床领域取得显著进展,推出了一系列高性能的数控机床 | 数控机床技术逐渐成熟,应用领域不断扩大 |
1980年代 | 日本数控机床产量超过美国,成为世界最大的数控机床生产国 | 日本在数控机床领域的技术创新和质量控制使其在全球市场上占据领先地位 |
1990年代至今 | 数控机床技术持续发展,各国纷纷推出高性能、高精度的数控机床 | 数控机床在控制、精度、自动化、灵活性等方面不断提升,广泛应用于航空航天、汽车、电子等高端制造领域 |
2020年代 | 中国数控机床产业发展迅速,技术突破显著,打破了国外的技术垄断 | 中国在高端数控机床领域取得了重要进展,国产数控机床的市场竞争力不断提升 |
早期手动车床
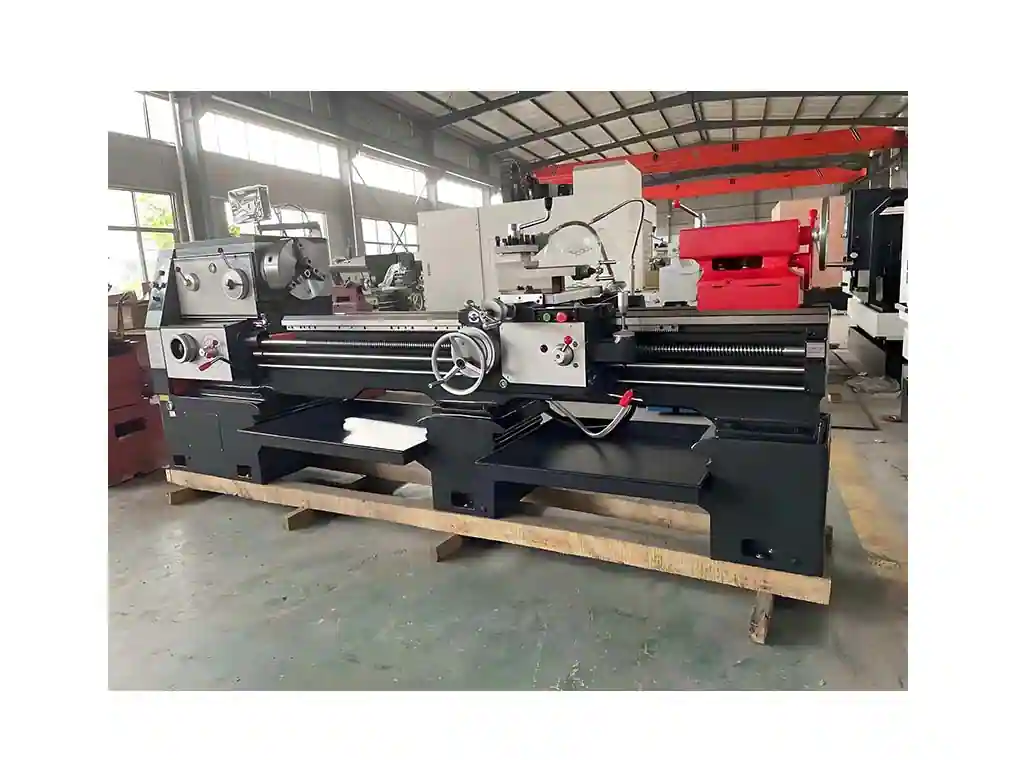
车床加工的本质,是旋转工件与线性刀具之间精妙的动态协同。这种制造技艺的源头,可追溯至公元前1300年的古埃及文明——工匠们用动物肌腱制成的绳索缠绕木料,通过往复拉动实现旋转切削,开创了人类最早的圆形构件加工方法。
工业革命时期,金属加工业的爆发性需求催生了车床技术的首次质变。蒸汽动力的引入,使皮带传动系统取代人力驱动,配合铸铁床身的抗震设计,让车床首次具备批量化生产标准件的能力。这一时期诞生的全齿轮传动系统,更是将加工精度推进到毫米级时代,为现代机械制造奠定了基石。
当下,数控技术的渗透彻底重构了车床的基因。操作者从体力劳动者转型为程序架构师,机床则演变为能自主执行复杂逻辑的智能终端。这种转型不仅使复杂曲面的加工周期缩短60%,更将尺寸精度稳定在微米量级,标志着制造业正式迈入数字化精密时代。
手动车床的基本设计和功能
手动车床作为机械加工的基石,其模块化设计至今仍是现代机床的灵感来源。从铸铁床身到精密传动系统,每个组件的协同作用诠释了机械工程的原始智慧,为数控技术的演进提供了底层逻辑。
床
手动车床的铸铁床身采用箱式结构设计,内部网格状加强筋显著提升抗扭刚度,其减振性能可吸收80%以上的切削震动。床身表面经精密磨削的V型导轨与平面导轨组合,确保拖板移动的直线精度控制在0.02mm/m以内,这种刚性基础使车床在加工高硬度合金时仍能保持稳定性,而经过时效处理的铸铁材质能有效抑制温升变形,保障长期加工的几何精度。
主轴箱
主轴箱作为动力中枢,内置六速齿轮变速系统,通过滑动齿轮组实现45-2000rpm的宽域转速调节。三爪自定心卡盘与弹性夹头的模块化设计,可快速切换Φ5-300mm工件的夹持方案,配合莫氏锥度主轴接口,确保工件径向跳动不超过0.03mm。变速手柄与离合器的联动设计,使操作者能在切削过程中无缝切换转速,适应从铝合金精车到不锈钢粗加工的多场景需求。
马车
复合拖板系统集成纵向/横向进给功能,纵向丝杠导程6mm/转,配合刻度盘实现0.02mm的微调精度。四工位转塔刀架支持快速换刀,15秒内完成车削、切槽、螺纹加工等多工序切换。通过挂轮箱的齿轮配比,可生成0.5-10mm的60种标准螺距,满足传动轴、丝杠等零件的精密螺纹加工需求,其重复定位精度达±0.01mm。
控制装置和协同系统
三手轮协同控制系统构成独特的人机交互范式:左手调节纵向进给量(0.05-0.3mm/r),右手控制横向切削深度(±0.01mm精度),脚踏板联动离合器实现主轴启停。走刀箱内的行星齿轮系将主轴运动分解为精确的进给传动比,而半螺母机构在螺纹加工时自动同步进给速率,这种机械逻辑设计使复杂加工流程转化为直观的手动操作。
刀架和润滑
可调式四方刀架支持刀具高度±2mm的精细调节,通过楔形锁紧机构确保切削过程的刚性。飞溅润滑系统为齿轮副持续供油,关键摩擦副设置8个手动注油点,复合润滑方案使设备在连续运转8小时后仍能维持稳定的摩擦系数。刀座的角度调节机构支持-5°至45°的刃倾角设定,满足锥面、球面等异形轮廓的加工需求。
手动车床操作的局限性详解
有限自动化
在加工汽车变速箱齿轮时,操作者需同步控制进给速率、切削深度和主轴转速,单件加工耗时长达50分钟,而数控设备仅需12分钟。这种高度依赖人工干预的模式,导致批量生产时效率损失达35%,且新手操作员的废品率比熟练工高出5倍。
精度的复杂性
加工柴油机喷油嘴壳体时,操作者的经验差异会导致关键孔径尺寸波动0.05-0.12mm。连续加工4小时后,床身热变形使尾座偏移0.03mm,而刀具磨损每20件累积0.1mm误差,这些变量使批量零件的一致性难以保障。
耗时的设置
某批次1000件的轴承座加工案例显示,传统车床换型需调整尾座位置(耗时25分钟)、重装夹具(15分钟)、试切校准(30分钟),准备时间占总工时的28%。相比之下,数控设备通过程序调用可在8分钟内完成全参数切换,凸显手动模式在大批量生产中的效率瓶颈。
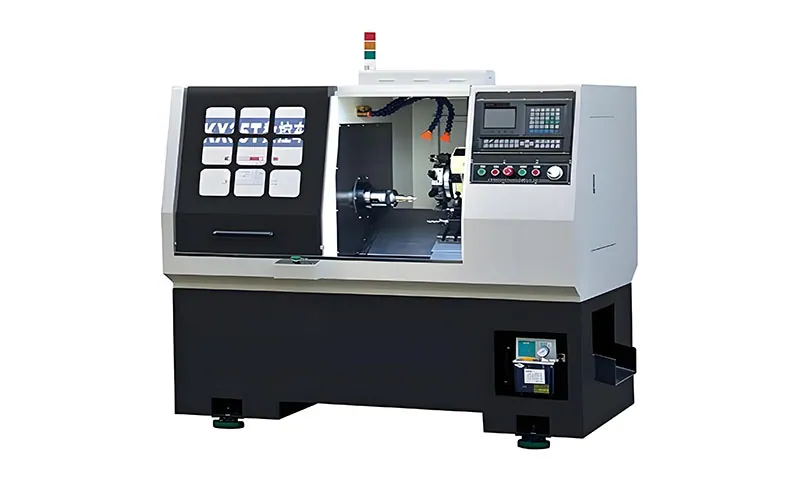
现代数控车床
作为智能制造体系的核心装备,现代数控车床通过数字技术与机械工程的深度融合,正在重新定义精密制造的边界。其技术演进不仅体现在硬件升级,更在于智能控制系统的突破性发展。
控制系统
现代数控车床搭载的数字控制系统如同设备的中枢神经,通过高速数据总线实时协调主轴、进给轴与辅助装置的协同运作。系统内置的误差补偿模块能自动修正机械传动间隙与热变形带来的微量偏差,配合光栅尺闭环反馈机制,将定位精度稳定在微米级范畴。这种数字化控制逻辑彻底改变了传统加工中依赖人工经验的操作模式,使复杂曲面的轮廓精度达到头发丝直径的1/10水平。
用户友好的编程接口
智能化人机交互界面革新了加工程序的创建方式,三维仿真模块可直观显示刀具路径与材料去除过程。操作者通过拖拽式编程功能快速生成G代码,系统自动优化切削参数组合,甚至能识别图纸特征推荐加工策略。触控屏与语音指令的融合设计,使设备调试效率提升60%,大幅降低了对编程专业技能的依赖门槛。
自适应控制算法
机床的智能内核通过多传感器网络实时采集切削力、振动频谱与温度变化数据,动态调整进给速率与主轴负载。在加工航空钛合金部件时,算法能识别材料硬点并自动降低切削深度,避免刀具崩刃。这种自我优化的能力使设备在连续加工中始终保持峰值效率,将刀具寿命延长30%以上,同时保障表面粗糙度稳定在Ra0.8μm以内。
更先进的加工能力
五轴联动技术打破了传统机床的运动维度限制,通过B轴摆头与C轴转台的协同,实现涡轮叶片等复杂零件的完整加工。动力刀塔集成铣削主轴的设计,允许在车削过程中同步完成交叉孔与端面特征的加工,消除二次装夹误差。多任务处理能力使原本需要3台设备完成的工序集中在一台机床上,将生产周期压缩40%。
集成自动化技术
模块化自动换刀系统配备40工位刀库,能在0.8秒内完成刀具切换,并通过RFID芯片自动核对刀具参数。智能冷却系统根据加工材料特性调节切削液喷射角度与流量,铝合金加工时采用微量润滑技术将冷却液消耗降低85%。设备内置的工件检测探头在加工间隙自动测量关键尺寸,实时反馈数据至控制系统进行补偿修正,形成完整的质量闭环管理。
手工车床 vs 数控车床 核心对比
对比维度 | 手工车床 | 数控车床 |
---|---|---|
加工精度 | ±0.05~0.1mm(依赖操作者技能) | ±0.005~0.01mm(光栅尺闭环控制) |
生产效率 | 单件耗时高(如加工阶梯轴需30分钟) | 批量生产快(同零件加工仅需5分钟) |
操作复杂度 | 需熟练技师(3年以上经验) | 编程后自动运行(基础操作培训1周可上岗) |
初期成本 | ¥3万~10万(入门级设备) | ¥20万~200万(五轴机型) |
柔性生产能力 | 适合单件/小批量(换型调整需1~2小时) | 支持大批量/复杂件(换程序仅需5分钟) |
典型应用 | 模具维修、教学实训、工艺品制作 | 航空航天零件、汽车零部件、医疗器械 |
能耗比 | 平均功耗3~5kW·h(无待机损耗) | 平均功耗10~30kW·h(含冷却/换刀系统) |
维护成本 | 年维护费¥0.5万~1万(机械部件易更换) | 年维护费¥3万~10万(需专业工程师保养) |
优劣势深度解析
手工车床优势
- 低成本灵活生产
- 适合初创企业:采购成本仅为数控设备的1/10
- 快速响应变更:调整刀具路径无需编程(如加工异形青铜件)
- 技术传承价值
- 培养机械直觉:操作者能直观感受切削力与材料特性
- 宁波某技校统计:手工车床实训使学员刀具选择准确率提升40%
数控车床优势
- 复杂零件加工能力
- 五轴联动:可加工涡轮叶片(曲面精度±0.005mm)
- 车铣复合:同步完成钻孔/攻丝(如加工汽车转向节节省3道工序)
- 生产一致性保障
- 批量加工2000件时,尺寸波动<0.01mm
- 某医疗器械厂数据:数控加工骨钉螺纹合格率99.7%,手工仅82%
选型建议
需求场景 | 推荐设备 | 理由 |
---|---|---|
教学/原型开发(预算有限) | 手工车床 | 低成本试错,培养基础技能 |
小批量多品种(<100件) | 经济型数控车床 | 通过程序复用降低单件成本 |
大批量精密件(>1000件) | 高端数控车床 | 自动化生产+质量追溯系统,综合成本降低40% |
超复杂零件(如航空件) | 五轴车铣中心 | 一次装夹完成多面加工,避免基准误差 |
数控车床的多元化应用场景
作为现代制造业的核心装备,数控车床凭借其高精度、高柔性的特点,已渗透到工业生产的各个关键领域。从微米级精密零件到大型复杂构件的加工,其技术优势正在重塑全球制造业格局。
复杂几何零件制造
在航空航天领域,五轴联动数控车床可一次性完成涡轮叶片(如图1)的叶根榫槽与气膜冷却孔加工,将传统工艺的12道工序缩减至3道,叶片轮廓精度达±0.005mm。某型号航空发动机高压压气机盘的加工案例显示,采用车铣复合技术后,生产周期从72小时压缩至18小时,且跳动误差控制在5μm以内。
精密模具制造
宁波压铸模具产业集群中,数控车床承担着关键模芯的精密加工任务。加工新能源汽车电机壳体模具时,通过热流道系统的多角度深孔车削(深径比达15:1),将模具寿命提升至50万模次。精密螺纹加工模块可生成0.2mm微细螺距,满足微型连接器的成型需求。
汽车零部件量产
- 发动机系统:曲轴轴颈的阶梯式车削,圆度误差≤0.003mm
- 传动系统:变速箱齿轮坯的硬车加工(HRC60),替代传统磨削工艺
- 电动化部件:电机转子的高速动平衡加工,转速达8000rpm时振幅<0.01mm
4. 医疗器械制造
人工关节的钛合金车削采用微量润滑技术,表面粗糙度Ra0.2μm满足植入要求。骨科螺钉的微细螺纹加工(M0.6×0.125)通过C轴分度实现0.01°定位精度,确保螺纹啮合可靠性。
5. 能源装备加工
核电站主泵叶轮的Inconel 718高温合金加工,通过自适应控制算法动态调节切削参数,将刀具寿命延长40%。风电轴承套圈的断续车削采用振动抑制技术,将加工效率提升3倍。
行业应用数据对比
应用领域 | 典型零件 | 精度要求 | 效率提升幅度 |
---|---|---|---|
航空航天 | 涡轮叶片 | ±0.005mm | 300% |
汽车制造 | 曲轴轴颈 | 圆度0.003mm | 150% |
医疗器械 | 人工关节 | Ra0.2μm | 200% |
能源装备 | 核电叶轮 | 轮廓度0.01mm | 250% |
常见问题及解答
数控车床是如何实现从基础加工到复杂制造的跨越?
数控车床的演进历经三大技术革命:
- 机电一体化阶段(1950-1970):
- 采用穿孔带编程,实现简单轴类零件的自动化加工(精度±0.1mm)
- 典型案例:通用汽车用首台数控车床加工变速箱齿轮,效率提升200%
- 数字化控制阶段(1980-2000):
- 引入微处理器技术,支持圆弧插补与多轴联动(精度±0.02mm)
- 突破案例:波音747发动机涡轮盘的五轴加工,将生产周期从30天缩短至7天
- 智能化制造阶段(2010至今):
- 集成AI算法与物联网技术,如马扎克iSMART Factory实现0.0001mm级控制
- 宁波某压铸模具企业通过数字孪生技术,将试模次数从15次降至3次
数控车床如何兼顾效率与环保?
- 效率提升技术:
- 自动换刀系统(换刀时间≤0.8秒)使批量加工效率提升60%
- 高速切削技术(主轴转速30,000rpm)将铝合金加工周期压缩40%
- 可持续性创新:
- 微量润滑系统(MQL)减少90%切削液使用,年节省成本¥15万/台
- 能源回收模块将制动能量转化为电能再利用,功耗降低25%
- 某新能源汽车部件厂通过数控优化排料,材料利用率从68%提升至92%
现代数控车床能否通吃简单与复杂零件?
- 简单零件加工:
- 批量生产螺栓时,通过宏程序实现每分钟60件的稳定产出
- 阶梯轴加工误差控制在±0.005mm,优于传统车床5倍精度
- 复杂零件突破:
- 五轴车铣复合加工航空发动机机匣,一次装夹完成200个特征加工
- 医疗领域加工人工髋关节,球面精度达Ra0.1μm(相当于镜面效果)
- 宁波某企业用数控车床加工0.2mm薄壁铝合金壳体,变形量<0.03mm