铝合金重力铸造常见缺陷及预防措施
发布时间:2025-01-21 分类:新闻 浏览量:803
重力铸造 就是在铸造过程中,先凝固的金属液体因热胀冷缩产生体积收缩,需靠上部未凝固的金属液重力来补充,完成补缩的效果。重力铸造的凝固方式为顺序凝固,就是整个零件在凝固时按照一定的次序先后凝固,相对靠后的凝固位置可以补缩相对靠前的凝固位置,使最终的铸造缺陷都集中在最后的冷却部位(冒口、浇口位置),得到合格的生产铸件。重力铸造 铝合金 轮毂铸件的凝固顺序:
轮辋——辐条——中毂(斜面)——分流锥——浇口(冒口)
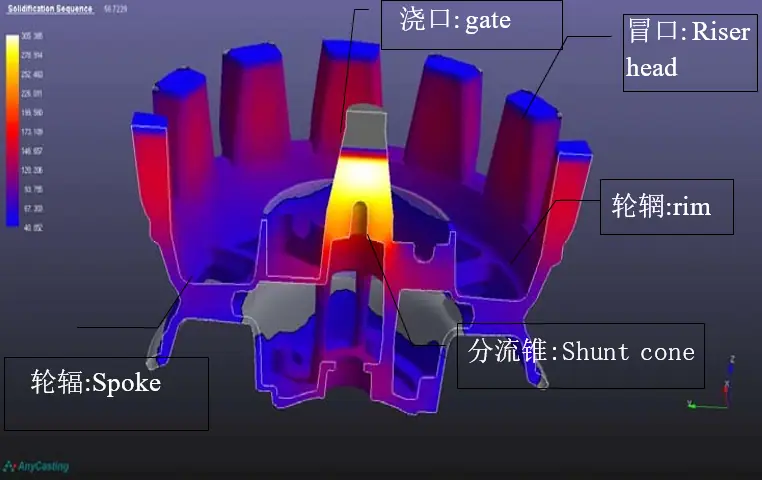
铸造工艺设计参数包括加工余量、工艺余量(冒口等补缩位置)、金属收缩量(收缩系数)和拔模斜度、冷却系统(用以保证铸件的顺序凝固)等。
当铸件的凝固顺序或工艺设计参数不满足产品需求时,就会产生铸造缺陷,铝合金铸件常见的铸造缺陷及预防措施有:
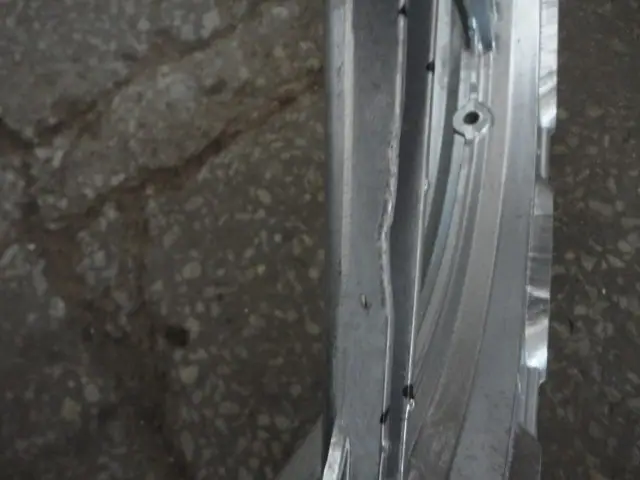
1.欠铸
特征:在铸件成形过程中,某些部位填充不完整。
形成原因:
a、铝液流动性不强,液体中含气量高、氧化皮较多;
b、浇注系统不良,内浇口截面太小;
c、模具排气条件不良,排气不畅、涂料过多、模温过高导致型腔内气压过高且不能顺利排出。
预防措施:1、提高铝液的流动性,尤其是精炼和扒渣,适当提高模温或浇铸温度(提高浇铸速度,调整壁厚余量、开设辅助筋通道);2、增大内浇口截面积;3、改善排气条件,根据不良现象结合模具实际情况,增加溢流槽和排气线,深凹型腔处增添排气塞,重新喷涂料,使涂料薄且均匀,并待涂料干燥后再合模生产。
2.裂纹
特征:毛坯被破坏或断开,开成细长纹路,呈不规则现状,有穿透和不穿透两种,在外力作用下呈发展趋势,冷、热裂纹的却别:冷裂纹处金属未被氧化,热裂纹处金属被氧化。
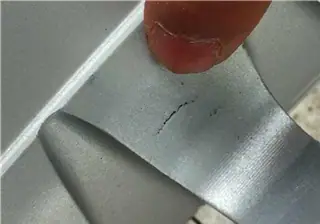
形成原因:
a、铸件结构欠合理,收缩受阻,铸造圆角小;
b、顶出装置发生偏移,受力不均;
c、模温过高或过低,开模过程中严重拉伤开裂;
d、合金中有害元素超标,伸长率下降;
e、排气不畅;
预防措施:1、改进铸件结构,减少模具壁厚差,增大裂纹部位的圆角或圆弧半径; 2、修正模具顶出系统及上、下模合模销、套,保证顶出平稳; 3、调整模温到正常温度,消除倒拉模和不平整现象,适当加大模具的扒模斜度; 4、控制好铝液成分,尤其是有害元素成分; 5、修整模具的排气系统,保证该部位模具排气通畅。
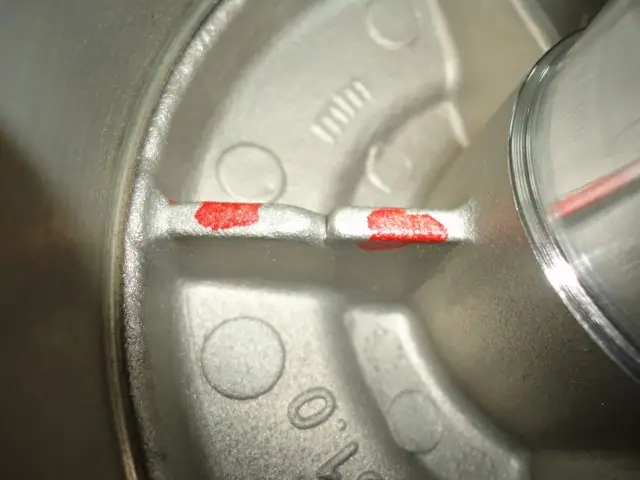
3.冷隔
特征:液流对接或搭接处有痕迹,其交接边缘圆滑,在外力作用下有继续发展的趋势。
形成原因:
a、铝液流动性差;
b、液体分股填充融合不良或流程太长,连接不上;
c、液体(模具)温度过低或排气不足;
预防措施:1、适当提高铝液温度和模具温度,检查调整铝液合金成分; 2、合理布置溢流槽,增加流道,缩短流程,使铝液充填充分; 3、提高浇铸速度或提高模具温度,改善模具排气系统。
4.气泡
特征:铸件表皮下,聚集气体膨胀所形成的气泡。
形成原因:
a、模具温度太高,铝液温度过高;
b、充型速度太快,金属液在充型过程中卷入气体。
c、涂料发气量大,喷涂过多,浇铸前未挥发完,气体被包裹在铸件表层;
d、排气不畅;
e、留模时间不够,开模过早。
预防措施:1、修正模具冷却工艺,冷却模温至正常工作温度;修正熔炼工艺,保证铝液温度正常; 2、减缓充型速度,避免涡流包气(可控制滤网的密度、厚度等); 3、选用发气量小得涂料,喷涂薄而均匀的涂料层,彻底干燥挥发后合模; 4、修正留模时间,保证充分凝固。
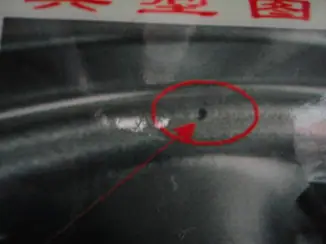
5.气孔(气、渣孔)
特征:卷入铸件内部的气体所形成的形状规则、表面较光滑的孔洞。
形成原因:
a、铝液进入型腔,发生正面冲击,产生漩涡; b、充型速度过快,产生滞流;
c、排气不畅; d、模具型腔位置过深; e、涂料过多,填充前未完全干燥挥发;
f、铝液精炼不良,未完全扒渣;
h、型腔内有杂物,过滤网不符合要求或放置不当; i、机械加工余量过大。
预防措施:1、采用有利于型腔内气体排出的导流形状,避免铝液先封闭分型面上的排溢系统; 2、降低铝液的充型速度(增加滤网密度等方式); 3、在型腔最后填充部位开设溢流槽和排气道,并避免被铝液封闭; 4、深腔安装排气塞,并采用镶拼结构增加排气; 5、用风枪清洁型腔,并重新喷涂料,保证涂料用量薄而均匀; 6、液态金属除气后,立即扒渣、浇注,不可停留过久,以防再吸气,另外,含铝的合金尽量不用供品炉熔炼; 7、在满足需求的情况下,合理调整产品加工余量。
6.缩孔
特征:铸件在冷凝过程中,由于内部补偿不足所造成的形状不规则,表面粗糙的孔洞。
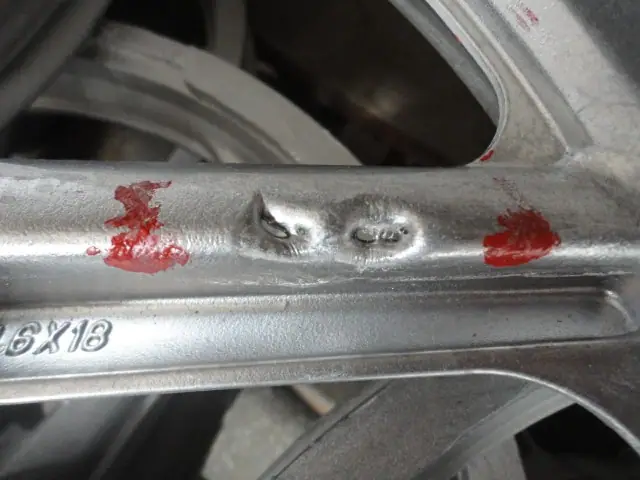
形成原因:
a、铝液温度过高;
b、铸件结构壁厚不均匀,产生热节;
c、内浇口较小;
d、模具局部温度偏高。
预防措施:1、在满足浇注要求的情况下,适当降低铝液温度; 2、改进铸件结构,消除金属积聚部位,缓慢过渡;若无法更改铸件结构时,对局部影响补缩的“冷节”部位,可在背后四周钻孔铣槽,然后填充绝热材料,以增大热阻,可调出合理的温度场; 3、对局部热结处应采取强制冷却(可采用局部镶嵌铜块等方式),以调出合理的补缩温度梯度; 4、增加暗冒口,以利于压力更好传递; 5、调整模具涂料厚度,控制模具局部温度。
7.花纹
特征:铸件表面呈光滑条纹,肉眼可见,但用手感觉不出,颜色与正常基本金属纹路不同,用砂纸稍擦即无。
形成原因:
a、充型速度太快;
b、涂料用量太多且不均;
预防措施:1、降低充型速度;2、涂料用量薄而均匀,遵循中间薄边缘厚的原则;
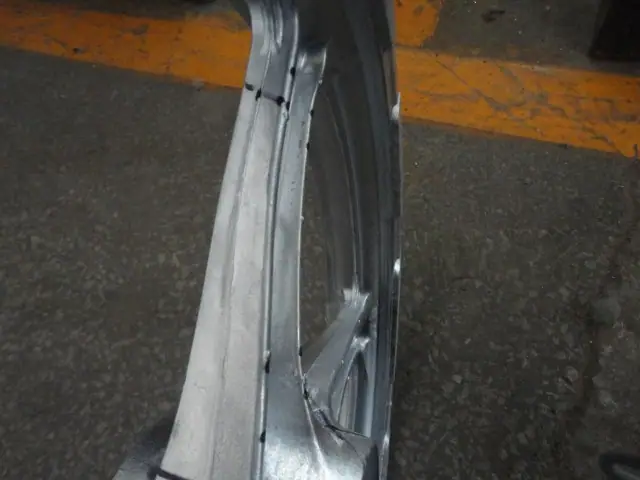
8.变形
特征:铸件几何形状与设计要求不符的整体变形。
形成原因:
a、铸件设计不良,引起不均匀收缩;
b、开模过早,铸件刚性不够;
c、模具扒模斜度过小,脱模困难;
d、取置铸件,操作不当;
e、铸件冷却过快,引起变形。
预防措施:1、改进铸件结构,使壁厚均匀; 2、确定最佳开模时间,增加铸件刚性; 3、加大铸件扒模斜度; 4、取放铸件时,应轻取轻放; 5、开模后,铸件应放置在空气中缓慢冷却。
9.缩松
特征:铝合金铸件缩松一般产生在内浇道附近、冒口根部厚大部位、轮辋壁、辐条的厚薄转接部位、具有大平面的薄壁部位。在铸坯未经过处理时断口为灰色,热处理后断口为灰白浅黄或灰黑色,在进行 X 光投射时,在 X 光底片上呈云雾状严重的呈丝网状,机加工部位在加工后呈小而分散的针孔。铸件的缩松可通过X 光、断口等检查方法发现。
形成原因:
a、冒口补缩作用差; b、炉料含气量太多; c、内浇道附近温度过高; d、砂型水分过多,砂芯未烘干;
e、模具涂料喷涂不当; f、铸件在铸型过程中充型时间不当;h、铝液温度过高,浇注速度过快。
预防措施:
1、从冒口部位补充铝液,改进浇口设计;2、 铝液的打渣、除气处理应充分彻底;3、 辐条缩松部位设置冷却系统或安放冷却环块(如模具镶嵌铜块等)等形式降低内浇道附近模具温度;4、 控制型砂水分,保证砂芯烘烤干燥; 5、选择合适的涂料,制定相应的涂料勾兑不理,改变涂料的喷涂方式(浇口越近涂料越薄),对相关人员进行专业培训;6、 改变铸件在铸型中的充型时间,调整工艺参数;7、 实时监测铝液温度,控制浇注速度(增加滤网或改变滤网的形状等方式)。
10.错模:
特征:铸件一部分与另一部分在分型面错开,发生相对偏移。
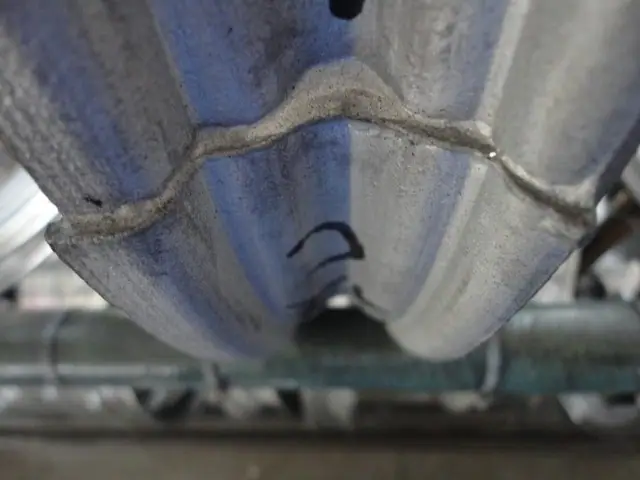
形成原因:
a、模具镶块位移(如四个滑块没有合模到位);
b、模具导向件磨损(模具合模销、套磨损);
c、模具制造、装配精度差。
预防措施:1、调整镶块,加以紧固; 2、更换导向部件; 3、修正模具,消除误差。
选择合适的重力压铸服务提供商
重力铸造是一种简单高效的金属铸造工艺,但它仍然需要一定的知识和经验。通过专业重力铸造技术,可以实现更高的精度和质量。因此,选择像宁波贺鑫这样的专业服务提供商来外包铸造需求是更明智的选择。
在宁波贺鑫,我们的工程师团队拥有多年重力铸造经验,能够为您的项目提供最合适的铸造工艺建议。作为一家ISO 9001:2015认证企业,我们配备了先进的铸造设备,确保生产出高品质的零件。通过我们的在线平台上传设计文件,您将在12小时内获得精准报价和技术分析,帮助您更高效地完成项目。
常见问题及回答
气孔缺陷的原因?
排气不畅、铝液精炼不良或浇注速度过快造成。
铝合金铸件出现花纹的原因?
花纹一般由于充型速度过快或涂料喷涂不均造成。
铝合金铸件出现裂纹的原因?
裂纹通常由于铸件结构设计不合理、模具温度不当或铝液中有害元素超标引起。
铝合金重力铸造中如何避免欠铸?
提高铝液的流动性(增加铝水温度,添加特定元素)、增大内浇口截面和改善模具排气条件(增加排期塞)