压铸铝合金ADC12产品抛丸起皮原因分析及解决方案推荐
发布时间:2025-04-07 分类:新闻 浏览量:371
本文系统解析了压铸铝合金ADC12的材料特性与抛丸工艺关联性,针对行业频发的抛丸起皮问题提出多维度解决方案。文章首先阐明ADC12化学成分对材料性能的直接影响,揭示硅、铜、镁等元素含量波动与合金流动性、强度及耐腐蚀性的内在关联。基于抛丸工艺原理,深入剖析弹丸参数、抛射速度等核心变量对表面处理效果的定量作用,指出当前行业存在仅关注附着力而忽视表面质量标准化的共性不足。通过模流分析、工艺参数优化及实验验证,创新性地构建从材料源头控制到模具设计、设备维护的全链条改进体系,结合电机壳体案例实证了排气道优化、储能压力调整等关键措施的有效性。研究不仅为ADC12抛丸质量提升提供可量化的技术路径,更展望了基于大数据AI技术的工艺优化新方向,对推动压铸行业降本增效具有实践指导意义。
压铸铝合金ADC12的材料特性
1、化学成份
主要元素及其作用
ADC12主要包含硅(Si)、铜(Cu)、镁(Mg)、锰(Mn)、铁(Fe)、锌(Zn)、铝(Al)。其中:
硅:含量允许在9.5~11.5%,如果低于9.5%,会出现合金流动性差,产品填充不完整,如果超过11.5%,则易出现过量偏析或和铁铝化合形成片状晶体,破坏合金组织的稳定,产品疏松;
铜:含量允许在1.5~3.5%,如果低于1.5%,会出现产品的强度及硬度下降,如果高于3.5%,会出现抗腐蚀能力下降;
镁:含量在0.1~0.3%,如果镁含量低于0.1%,会出现产品的强度及硬度下降,如果高于0.3%,会导致压铸时产品产生热裂等缺陷;
锰:含量在0.2~0.5%,如果低于0.2%,会出现合金的晶粒粗大,抗拉强度和屈服强度同时降低,如果高于0.5%,会出现合金的硬脆性增高,难以加工,易脆断;
铁:含量在0.6~1.2%,如果低于0.6%,易粘模,形成产品拉伤变形,如果高于1.2%,会出现合金因硬脆而开裂;(铁和硅同时超高,容易形成片状的硅-铁-铝晶体,造成晶间腐蚀,合金强度下降)
锌:含量≤1.2%,所以锌在ADC12合金里可以没有(在提炼其他合金时难以清除),如果有,必须小于1.2%。
另外回炉料的搭配比例也非常关键,如果回炉料过多,会造成产品结晶晶粒粗大,产品的强度及硬度降低。
综上所述,合金的化学成份(百分含量)基本决定了其机械性能,也制约着产品的外观及内部结晶组织结构。
2、物理性能
ADC12铝合金的密度大约为2.7克/厘米³,熔点为580~620°C;需要注意的是这些物理性质的值会因为具体的成分差异和生产工艺等因素而有所不同。
ADC12的热膨胀系数相对较大,这一特性与抛丸工艺存在一定关联。
3、力学性能
ADC12铝合金的力学性能指标通常如下:
抗拉强度:约228~296MPa;
屈服强度:约140~170MPa;
布氏硬度:约70~95HB;
延伸率:1~3%
具体的性能指标也会因成分差异和生产工艺等因素而有所不同。
抛丸工艺概述
1、抛丸原理
抛丸设备的工作机制
抛丸的工作机制主要包括以下几个部分:
弹丸储存与运输系统:弹丸通常存储在特定的料斗中,通过输送装置(如螺旋输送机)将弹丸输送到抛丸器内;
抛丸器:这是抛丸设备的核心部件,抛丸器内部有高速旋转的叶轮,叶轮上有多个叶片,当叶轮高速旋转时,叶片会带动弹丸加速并高速抛射出去;
工件输送系统:用于将待处理的工件输送到抛丸区域,并在处理完成后将其送出,常用的输送方式有履带式、吊钩式、辊道式等;
除尘系统:在抛丸过程中会产生大量的灰尘和杂质,除尘系统通过风机产生负压,将灰尘吸入除尘器进行过滤和净化,以保证工作环境的清洁和符合环保要求。
抛丸是一种表面处理技术,其原理主要是利用高速旋转的叶轮将弹丸(通常是钢丸,钢丝切丸等)以很高的速度抛射到被处理工件的表面;在抛丸过程中,弹丸具有较大的动能撞击工件表面时产生强烈的冲击和刮削作用,这种冲击能去除工件表面的氧化皮、锈蚀、污垢等附着物,同时在工件表面产生压应力,使表面得到强化。提高疲劳强度和抗应力腐蚀能力;具体来说,抛丸设备中的叶轮在电机的驱动下高速旋转,弹丸被叶轮加速后按特定的方向抛出,当弹丸撞击到工件表面时会造成工件表面的材料产生塑性变形和脱落,从而达到清理和强化的效果。
抛丸的效果取决于弹丸的材质,形状、尺寸、速度、抛射角度,以及抛丸时间等多种因素,不同的工件和处理需求需要选择合适的抛丸工艺参数,以达到理想的处理质量和效率。
2、抛丸工艺参数
抛丸丸粒材质及大小:用于ADC12铝合金的抛丸丸粒材料常用304不锈钢铸钢丸或钢丝切丸;其丸粒直径为0.2~0.6毫米;
抛丸速度:用于ADC12铝合金的抛丸速度通常为50~70米/秒;
抛丸角度:通常为30~75度;
抛丸时间:根据工件的大小,形状和表面状态,一般5~15分钟;
弹丸流量:根据抛丸设备和工件情况,通常在90~280千克/分钟;
设置原则:在实际生产中,应通过试验和质量检测来确定最适合被抛丸的工件的工艺参数,以获得理想的表面处理效果和避免起皮、起皱等问题,以最小的参数获得理想的表面处理效果是抛丸参数设置的最高追求,也是实现效益最大化的途径之一。
3、抛丸工艺在压铸铝合金ADC12产品中的应用现状
行业内常见的做法
对工件抛丸目的仅为了增加烤漆或喷塑要求的附着力,抛丸丸粒使用较粗大,抛丸时间较短,抛丸起皮工件采用返修打磨处理,没有精细探究抛丸起皮等问题产生原因,以及制定改善方案;
对工件抛丸后的表面质量进行严格要求,如色差(标准为银白色),起皮(未脱落悬浮于产品表面的不规则片体),起皱(抛丸表面呈皱纹),变形等缺陷进行接收下限标准化;从而对压铸过程凡是引起产品气孔,疏松,冷隔,流痕(滞留)等缺陷进行原因分析,并制定改善措施,对抛丸机的一些功能进行升级,持续优化,追求抛丸表面质量达到0缺陷目标。
存在的问题与挑战
优质合格的ADC12铝合金抛丸件是优质合格的压铸毛坯在经过抛丸设备的加工完成的,如果抛丸件出现起皮等问题,末位倒推分析原因:抛丸设备是否完好?→使用的抛丸丸粒是否合适?→设置的抛丸时间、速度、流量是否合适?→压铸毛坯打磨是否符合要求?→压铸毛坯是否有外观缺陷(冷隔、流痕、花斑、气孔、裂纹等)?→压铸生产时,压铸机及周边设备是否完好?→工艺参数(压射压力、压射速度、浇注温度、涂料浓度及喷涂量等)是否最优?→压铸模具浇排系统、冷却系统、顶出机构、型腔的光洁度、型腔的脱模斜度、型腔零件的硬度、型腔的圆角等)是否符合要求?→压铸模具的活动机构是否运行稳定可靠?→熔炼过程的工艺参数(回炉料搭配、熔化温度、精炼温度、精炼剂用量比例、氮气设置压力及流量等)是否最优?→ADC12化学元素是否符合要求?
在实际生产中,可能分析出某个环节出现了问题,但是在解决其问题时,必须综合考虑是否会带来其他问题,所以需要团队的沟通和协作,需要多方位论证与多次实验验证。
03.
压铸铝合金ADC12产品抛丸起皮原因分析
1、源头-ADC12材料因素
硅(Si)含量≥11.5%:铁(Fe)≥1.2%,产生化合过剩,以及片状组织,表面组织疏松,在抛丸的冲击力及刮削下,会发生起皮现象;
镁(Mg)≥0.3%:锰(Mn)≥0.5%,锌(Zn)≥1.2%;产生硬脆表面或裂纹表面,在抛丸的冲击力下,会发生严重脱皮缺料;
铜(Cu)≤1.5%:产品的表面强度和硬度不足,在抛丸的冲击力及刮削下,会发生凹陷变形及起皮或起皱;
回炉料比例≥50%:熔炼除渣和除气都非常困难,物理性能和机械性能会降低,压铸产品难以达到良好的表面(气孔和杂质呈现在产品填充末端表面),抛丸容易起皮。
2、压铸模具设计因素
模具直浇道截面与横浇道截面比例不当,横浇道总截面大于直浇道截面,在横浇道处产生负压卷气,气体进入模具型腔增大排气道负荷,气体易残留在产品中,形成气孔,气孔分布到产品浅表,抛丸会起皮或起泡;
多股分支浇道填充时,浇道的间距太大,两股浇道中间会形成回流困气;两股或多股浇道填充方向对冲,形成紊流,产品浅表会有气孔(俗称滞瘤),经抛丸力冲击,会起皮;
模具设计循环冷却水道时,到达了浇道填充末端,造成模具温度始终处于较低状态,产品浅表出现冷隔,流痕,麻面等疏松情况,经抛丸力冲击,会严重起皮;
模具设计的排气道不能满足排气需求(排气速度大于350米/秒),溢流槽位置不在填充末端或缺陷位置,造成排气和排渣不畅通及困气,产品填充末端位置出现浅表层气孔,抛丸力冲击,起皮;
模具横浇道及内浇口截面太小,填充压力受阻,增压力传递困难,产品疏松--强度和硬度不达要求,抛丸力冲击,会起皮或变形。
3、压铸机及周边设备因素
压铸机型板平行度及平面度(≤0.5)误差较大,锁模不牢固,造成分型面跑铝水,铸造压力耗损,产品强度及硬度下降,抛丸力冲击,产品起皮
压射机构的压射中心与定模型板压射孔中心偏心,造成压射冲头卡滞,压力耗损,产品强度及硬度下降,抛丸力冲击,产品起皮;
冲头与熔杯的配合间隙过大,压射时反跑铝水,造成冲头卡滞,压力耗损,产品强度及硬度下降,抛丸力冲击,产品起皮
压铸周边的真空机-真空阀堵塞,抽真空失效,产品困气,产品浅表出现冷隔,流痕,麻面等疏松情况,经抛丸力冲击,会严重起皮;
点冷却机失效,冷却水压力不足,流量不足,造成模具热集中部位过热,产品对应该部位出现热收缩和氧化皮起层,抛丸力冲击,产品起皮。
4、压铸工艺设置因素
保温炉温度设置偏低(≤640°C),易出现硅偏析,易出现铝液填充流动性降低,易出现产品填充不饱满,产品浅表层有冷隔,流痕,麻面等疏松情况,经抛丸力冲击,会严重起皮;
铸造压力以及填充速度设置偏低,产品强度及硬度下降,抛丸力冲击,产品起皮;
填充高速启动点位置设置不当:1.高速启动点位置较前,熔杯里的空气会卷入型腔,排气道排气负荷增大,气体难以排净,填充末端会产生气孔,产品浅表面气孔受抛丸冲击力,起皮;2.高速启动点位置较后,铝液慢速进入型腔,会迅速变冷,产品会形成夹层(冷隔)、疏松,抛丸力冲击,产品起皮;
喷涂时间设置过长,造成模具温度(185~230°C)偏低或热量不平衡,产品会出现冷隔,流痕,麻面等疏松情况,经抛丸力冲击,会严重起皮;
高压点冷设置通水时间(标准为压射结束延时3~8秒)过长,造成模具局部温度(185~230°C)偏低或热量不平衡,产品会出现冷隔,流痕,麻面等疏松情况,经抛丸力冲击,会严重起皮;
真空机抽真空启动时间及结束时间设置不当,造成抽真空失效,型腔困气,产品浅表层气孔经抛丸力冲击,会严重起皮;
5、压铸件毛坯打磨因素
压铸件毛坯的飞边及多料未清理打磨干净,抛丸后残留飞皮-起皮;
压铸件毛坯打磨过度,将毛坯表面致密层打磨掉了,抛丸力冲击,会起皮。
6、抛丸丸粒尺寸因素
购买的抛丸丸粒直径不一致,大于工艺设置直径尺寸,导致抛丸力增大,将产品冲击起皮;
7、抛丸工艺参数设置因素
设置抛丸速度过高,冲击力增大,导致产品起皮;
设置抛丸时间过长,连续冲击刮削,导致产品致密层剥落,产品起皮;
设置抛丸弹丸流量过大,冲击刮削增大,导致产品致密层剥落,产品起皮。
8、环境因素
抛丸环境不通风,温度偏高,导致产品表面软化,抛丸起皮。
针对压铸铝合金ADC12产品抛丸起皮问题的推荐解决方案
1、材料改进措施
采购的原材料ADC12化学成分尽量取允许的中间值;
回炉料分等级处理升级至二级回炉料,搭配新料使用,并降低回炉料比例。
2、压铸模具浇排及冷却系统的优化措施
通过模流分析,查找浇道填充死角、负压卷气紊流、末端交汇等不良填充模式,优化浇道的填充模式,减少死角回流,减少负压卷气,增加溢流排气设置;
通过模流分析,查找氧化夹渣部位、热节点,增设模具点冷装置(机构),使模具热平衡达到改善。
3、压铸机及周边设备的检查维护
压铸机的系统压力;
压铸机的锁模力——四根哥林柱受力均衡;
压铸机压射系统的压力、速度、冲头运行位置等的准确度;
空压机、真空机、高压点冷机、保温炉、喷雾机等。
4、压铸工艺参数的优化
保温炉温度设置660°C±10°C
压铸高速启点在理论高速启点基础上提前60~100mm,试压铸生产毛坯送抛丸走样验证,确定最佳位置;
铸造压力按产品平均壁厚推荐值取上限(1~3mm—铸造压力45~60MPa;3~6mm—铸造压力60~80MPa;6-10mm—铸造压力80~110MPa)。
5、压铸毛坯的清理打磨要领标准提升
压铸毛坯的清理打磨定标准时,必须将打磨清理后的样件拿去抛丸验证,没有飞边起皮,打磨清理的标准样件才能封存,发布,并且严格按样件进行打磨清理压铸毛坯。
6、抛丸机的点检维护
抛丸机必须满足各工艺参数的设置;
抛丸机的显示器显示的数据必须准确。
7、抛丸丸粒的精选及新旧搭配
抛丸丸粒必须用专用筛子进行筛选,大于工艺要求直径的丸粒筛选出来后需经丸粒供应商重新研磨后才能使用,且需重新筛选;新丸添加比例不超过60%。
8、抛丸工艺参数的固化
抛丸工艺参数需要先按比较低的抛丸速度和抛丸弹丸流量,抛丸时间尽可能短,经过试抛验证,确认产品符合抛丸质量(不起皮,无色差)才能固化工艺参数。
9、抛丸环境的温度控制
抛丸环境必须保持干燥通风,温度控制在30°C以内。
实验验证案例
ADC12压铸件—电机壳体毛坯抛丸起皮问题清单
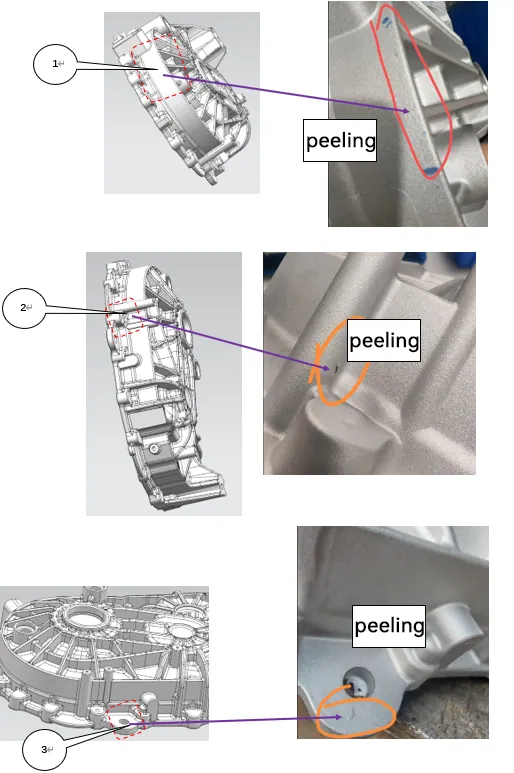
1、各起皮部位原因分析
起皮位置①②③都属于填充末端,排气不畅及填充压力偏小是主要原因,其次是铝液浇注温度偏低;位置②显示抛丸时间过长,表面兼有起皱的现象,实质上是产品的强度和硬度不均,且偏低(压铸件白坯在起皮附近有冷隔和流痕)。
2、针对各起皮部位制定改善措施
(1)疏通排气道,并将排气道加深0.05mm;
(2)优化压铸工艺参数~二快蓄能器添加氮气(由11.5MPa增加到12MPa),储能压力提高(由13.5MPa增大到14.5MPa);保温炉温度设置提高(由645°C提高到660°C);
(3)优化抛丸工艺参数~缩短抛丸时间(由外露挂单面抛丸6分钟缩短至5分钟)。
3、实施措施团队任务
(1)模修组修模具排气板,排气深度加深0.05mm
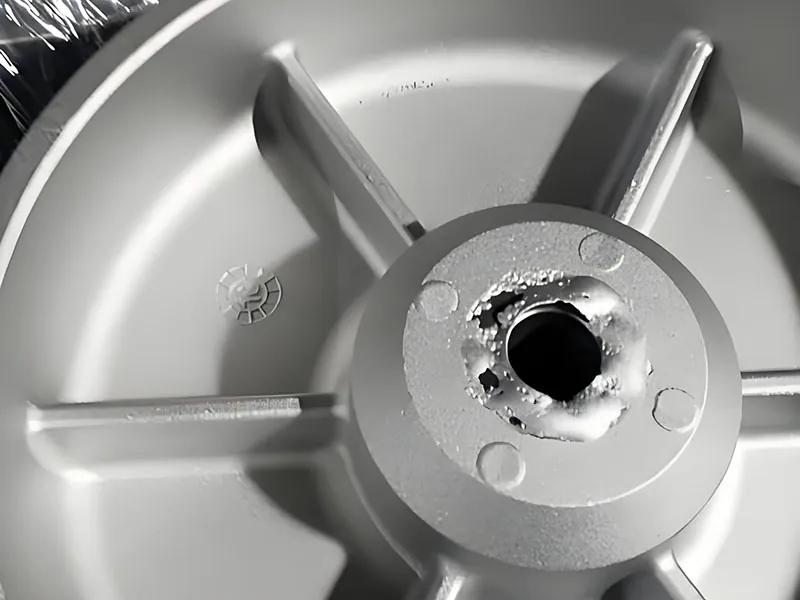
(2)压铸工艺组按改善措施重新设置参数二快储能压力14.5MPa,保温炉温度设置为660°C;
(3)压铸工艺组重新设置抛丸时间5分钟。
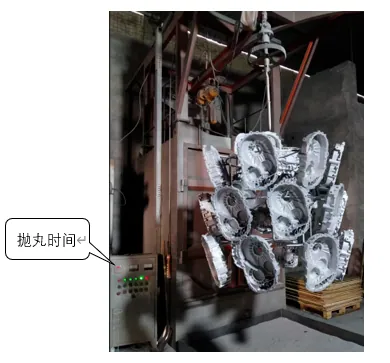
4、措施的落实与检测
落实改善措施后,经抛丸验证,品质部检测判定为合格,如下图所示:
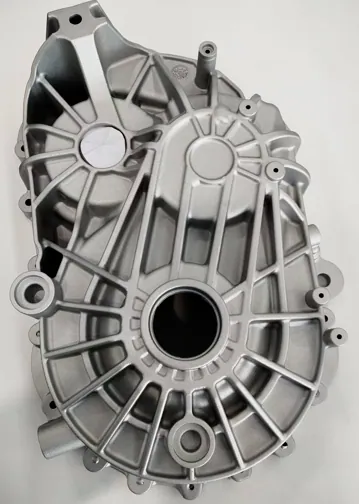
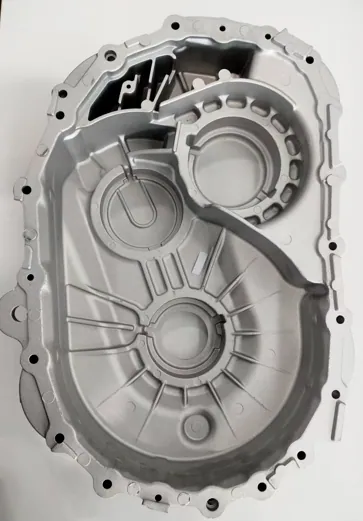
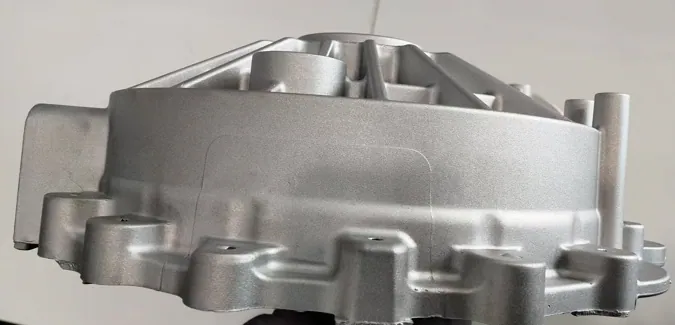
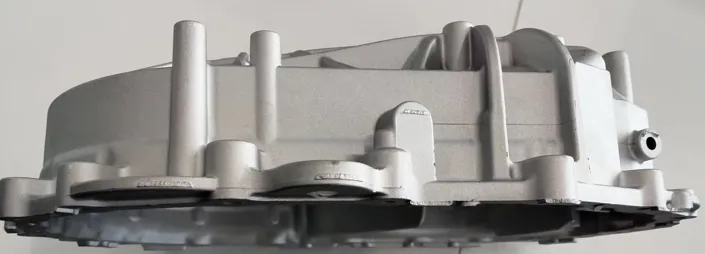
总结改善结果
用排除法寻找准确的抛丸起皮的原因,然后制定对应措施,以较小的实验成本解决ADC12合金产品起皮问题,这种结果是压铸行业的追求,也是目标。
结论与展望
1、研究结论
通过对铝合金ADC12材料的化学成分、物理性能、机械性能的分析,通过对压铸工艺过程的分析,总结出保证ADC12铝合金产品强度及硬度的必要条件,通过对抛丸丸粒的了解,通过对抛丸工艺过程的分析,总结出抛丸过程对产品具有冲击力和刮削力,综合解析为:如果ADC12铝合金强度和硬度不达标,抛丸易起皮;如果抛丸丸粒大,抛丸弹丸流量大,抛丸时间过长,ADC12合金产品经抛丸后也易起皮,所以需要两者平衡。
如以上案例所述,产品的强度和硬度不达标,通过改善提高了强度和硬度,抛丸的时间过长,通过改善缩短了抛丸时间,最终获得了ADC12合金的抛丸合格产品。
2、研究不足与展望
研究过程的不足:由于实验次数较少,且难以检测产品局部强度,所以没有真正找到产品强度和硬度的适应抛丸不起皮的临界点(数据),没有达到最低成本成就ADC12合金产品强度和硬度与抛丸的冲击力和刮削力的平衡。
未来研究方向的展望:随着大数据AI技术的发展,相信同行业会将ADC12合金抛丸起皮的问题解决得更彻底,花费成本更低,收获效益更多。
常见问题
- Q: ADC12的铸造性能优势是什么?
A: 流动性极佳,易成型复杂精密零件,且耐腐蚀性强,适合大批量生产。 - Q: 如何避免抛丸起皮?
A: 需综合控制材料成分、模具排气设计、压铸工艺参数(如温度、压力)及抛丸参数。 - Q: 抛丸工艺参数如何设置?
A: 弹丸材质(如不锈钢丸)、速度(50~70米/秒)、时间(5~15分钟)需根据工件特性调整。 - Q: ADC12抛丸后常见缺陷有哪些?
A: 起皮、起皱、变形等,多由材料成分超标、模具设计不良或抛丸参数不当引起。 - Q: 模具优化方向有哪些?
A: 通过模流分析改善浇道设计,增加排气道和溢流槽,避免气孔和冷隔。 - Q: 压铸工艺如何调整?
A: 提高保温炉温度(660°C±10°C),优化铸造压力和填充速度,确保产品致密。 - Q: 抛丸丸粒如何选择?
A: 使用直径0.2~0.6mm的不锈钢丸,筛选去除过大颗粒,新旧丸粒按比例混合。 - Q: 抛丸参数设置的最佳实践?
A: 初始参数设为低速度、短时间和低弹丸流量,逐步调整至不起皮且表面质量达标。