铝压铸模具设计与制造
发布时间:2024-08-05 分类:新闻 浏览量:1801
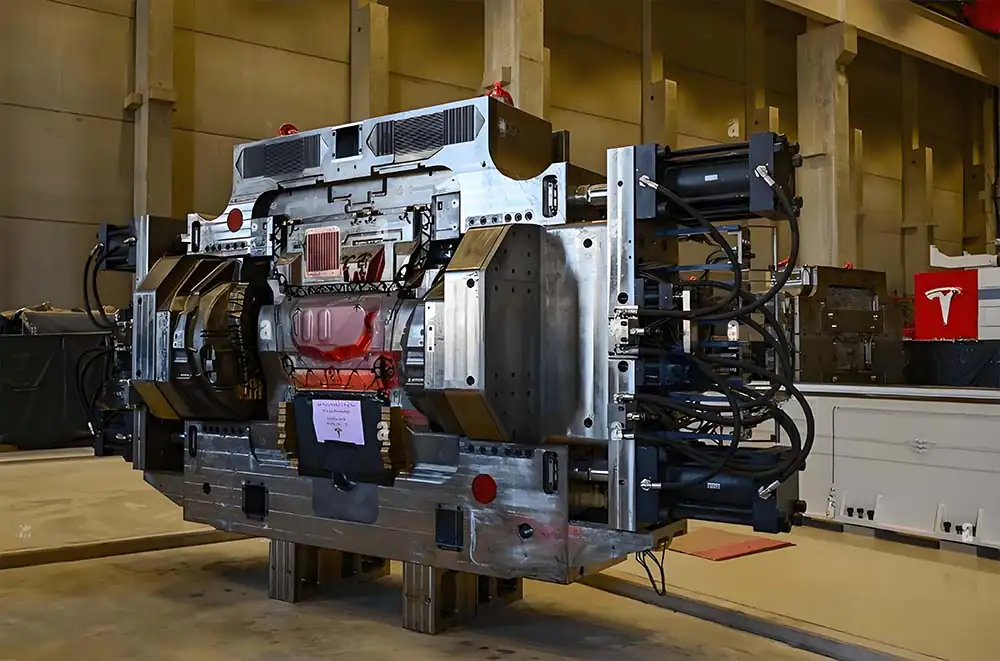
A、压铸成型技术简介
压力铸造简称压铸,是利用压铸机的压力作用将合金熔融液体以一定速度充填满按照一定的零件结构和工艺要求设计并经过精密制造的模具型腔,且合金熔融液体保持在一定压力作用下,在模具型腔中冷却凝固并成型的一种高效益、高效率的精密铸造技术。
B、压铸成型技术的特点与应用范围
1、压铸成型技术的特点
高压、高速是压铸液态或半液态金属充填成型过程的两大主要特点,也是压铸成型技术与其它铸造方法最根本的区别。
2、压铸成型技术的应用范围
压铸技术是最先进的金属成型方法之一,是实现少切屑、无切屑的有效途径。目前压铸用的合金已不再仅局限于锌、铝、镁和铜等合金,而是逐渐扩大到用铸铁和铸钢等铁合金来生产压铸件。
C、压铸成型技术的发展趋势
由于采用压铸成型技术,对企业有其积极和明显的经济效益。今后压铸成型
技术的发展方向为:
⑴、压铸成型技术向智能化方向发展。
⑵、研发压铸新材料,满足工业技术进步的需要。
⑶、研发新式压铸设备,提高自动化水平。
⑷、发展新型检测技术。
⑸、发展压铸新技术,改善和提高压铸工艺水平。
⑹、提高压铸模寿命,降低生产成本,以解决黑色金属压铸问题逐渐扩大到用铸铁和铸钢等铁合金来生产压铸件。
压铸模设计
A、压铸模设计概述
- 压铸时,压铸模、压铸机、压铸合金通过压铸工艺参数的相互联系协调,共同完成压铸件的压铸成型过程。压铸模在压铸生产过程中的作用如下:
- ①、确定浇注系统,特别是内浇口位置和导流方向以及排溢系统的位置,它们共同决定着熔融金属的填充条件和成型状况;
- ②、压铸模是压铸件的复映,决定了压铸件的形状和精度;
- ③、模具成型表面的质量直接影响压铸件的表面质量以及脱模阻力的大小
- ④、在压铸成型后,保证压铸件顺利从压铸模中脱出,且推出模体后,应无变
- 形、破损等现象的发生;
- ⑤、模具具备的强度和刚度承受压射力以及内浇口速度对模具的冲击;
- ⑥、在压铸过程中,控制和调节模具的热交换和热平衡;
- ⑦、最大限度发挥压铸机成型效率。
B、压铸模设计的基本原则
⑴、充分了解压铸件的用途和与其它结构件的装配关系,并根据压铸件的结构特点、使用性能,在模具设计时分清主次,突出模具结构的重点以及结合模具加工的工艺性,合理选择模具的分型面、型腔数量和布局形式、压铸件的推出形式和侧向脱模形式。
⑵、了解现场模具实际的加工能力,如现有的设备和可协作单位的装备情况,以及操作人员的技术水平,结合实际地设计出符合现场加工能力的模具结构形式。
⑶、模具应适应压铸生产的各项工艺要求,选择符合压铸工艺要求的浇注系统和排溢系统,特别是内浇口位置、内浇口速度和液流方向,应使金属液流动平稳、顺畅,并有序地排出型腔内的气体,以达到良好的填充效果和避免压铸缺陷的产生。
⑷、在保证压铸件质量稳定和安全生产的前提下,压铸模应具备:
①、结构简单、先进合理,运行准确可靠,减少操作程序。
②、操作方便,安全快捷,易损零件拆卸方便,便于维修,制造成本低。
③、有较高的压铸效率,实现充模快、开模快、脱模机构灵活可靠以及自动化程度高等特点。
⑸、模具结构件应满足机械加工工艺和热处理工艺的要求。选材适当,尤其是各成型零件和其它与金属液直接接触的零件,应选用优质耐热钢,并进行淬硬处理,使其具有足够抵抗热变形能力、疲劳强度和硬度等综合力学性能以及耐蚀性能。
⑹、应充分考虑模具温度变化对相对滑动部位的配合精度带来的影响。
⑺、模具设计应在可行性的基础上,对经济性进行综合考虑。
①、模具总体结构力求简单、实用,综合造价低廉。
②、应选取经济、实用的尺寸配合精度。
③、注意减少浇注系统余料的消耗量。
除正常设计的基本要求外,还应特别考虑:
1、 采用合理先进的简单结构,使工件准确可靠,结构的刚性良好,即模具具有足够的厚度,以确保其有足够的刚度,以防止模具变形及开裂。同时也要考虑模具拆换方便,有利于
延长模具的使用寿命;
2、 模具上的零件应满足机械加工工艺和热处理工艺的要求。尽量避免或减少尖角和薄壁,以利于后续热处理,防止应力集中。如果结构不能避免尖角,应在开粗时预留足够的 R角,热处理之后加工到位,避免热处理开裂的风险。
3、 大型压铸模具(分型面投影面积大于 1 平方米),应采用方导柱导向系统,以避免动定模因热膨胀差异较大,造成导向精度下降;
4、 对于设计大型复杂压铸模具的浇注系统及排气系统和冷却系统,最好能做流动分析及热平衡分析。这样布置流道系统(直浇道、横浇道、内浇口)及恒温预热系统的位置、角度大小、数量等就会做到合理布局;众所周知,浇注系统是把金属液从压室导入型腔内,它与金属液进入型腔的部位、方向、流动状态等密切相关,并能调节填充速度、充填时间、型腔温度等充型条件。在压铸生产中,浇注系统对压铸件质量、压铸操作效率、模具寿命(高温、高压、高速的金属液对模具型腔壁的冲刷、腐蚀等),压铸件的切边和清理等也有重大影响,可见浇注系统
的设计及其重要;
5、 内浇口设计注意事项:
从内浇口进入型腔的高温金属液、不宜正面进入冲击动定模型壁及型芯,以防止型腔出现早期的冲蚀、粘模和龟裂等现象;采用多股内浇口时,要考虑防止出现金属液进入型腔后从几路汇合,相互冲击产生涡流,裹气和氧化夹渣等缺陷;内浇口厚度的选择,一般是按照经验数据制定,建议在满足充型的条件下,尽量选择大些,避免因过大的压射速度冲击,引起模具早期出现侵蚀、粘模、麻点和龟裂;
6、 溢流槽和排气槽的设计:
溢流槽的作用是积累首先进入型腔的冷却金属液和裹有气体的金属液,以及调节模具个部分的温度,改善模具热平衡,有利于延长模具使用寿命。一般设在金属液流程的末端,设置合适的溢流槽可以改善填充条件,提高铸件质量。排气槽用于从型腔内排出空气及涂料挥发产生的气体,其设置的位置与内浇口的位置及产品结构有关。为使型腔内气体压射时尽可能被压铸的金属液排出,将排气槽设置在金属液最后填充的部位。排气槽一般和溢流槽结合,布置在溢流槽后端,以加强溢流和排气效果。
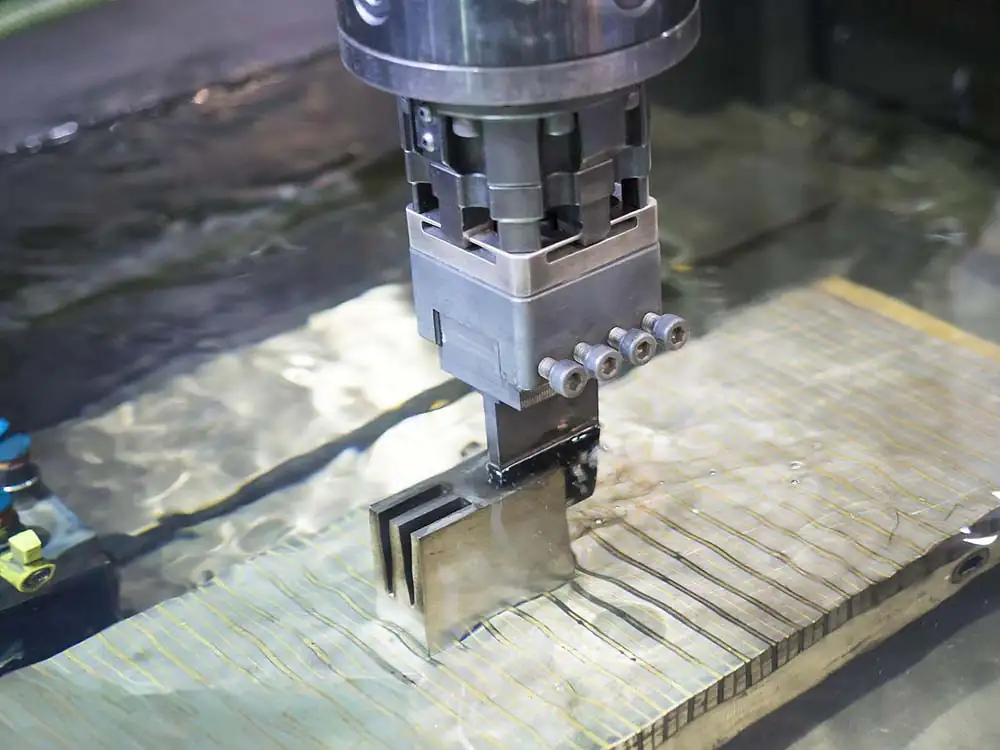
机械加工对模具失效的影响
众所周知,压铸模具制造周期较长,机械加工复杂,涉及到车、磨、铣、钻、刨机加工和放电加工(线切割、电火花)等工序。其加工质量,尤其是表面的加工质量在模具制造过程中和随后的使用过程中,会显著影响模具的断裂抗力、疲劳强度、热疲劳抗力和耐磨性、耐腐蚀性等。加工过程中稍有失误,就有可能造成模具早期失效。例如龟裂和热裂是铝合金压铸模的常见失效现象,它是模具表面的热疲劳、应力、低强度及表面粗糙引起的。
1、 切削加工的影响
模块在机加工切削过程中,由于破坏工件基体原先的平衡,会产生应力,这些内应力降低了模块表面的总强度,导致热疲劳强度的不足,从而在拐角和小半径圆弧过渡处产生龟裂或裂纹。所以,应尽量避免尖角。尖角和加工刀痕能显著引起应力集中,除非有特殊要求,否则,应避免尖角,并使拐角的圆弧曲率半径充分放大,目的就是避免或减少应力集中。例如:把圆弧半径 R 从 1mm 增大到 5mm,最大内应力约减少 40%,极大地提高了模具的强韧性。当模块圆弧半径由 2mm 提高到 20mm 时,其冲击韧性可提高 4倍。同理,模具表面粗糙度大小对模具寿命影响也较大。如存在明显的刀痕、裂口、切口等,这些加工缺陷均会引起应力集中,成为裂纹的根源。因此要保证模具的表面粗糙度要求,型腔表面应进行打磨抛光,去除刀痕等缺陷。冷却水孔的钻削加工,如果为双向钻削,出现错位,则会在该处引起早期开裂,导漏水。模胚切削加工余量不足,经过锻造和退火的模胚,或者模具胚料、型芯,加工后在空气炉中加热淬火,一般都存在一定厚度的脱碳层,切削加工时必须把脱碳层全部去除。否则,残留脱碳层在模具使用过程中,将会降低模具表面的热疲劳抗力,引起该部位龟裂。
2、 磨削加工的影响:
压铸模具热处理后,在磨削(包括钳工、砂轮打磨)时,可能会出现下列问题:
A、 发生龟裂或开裂,这是由于砂轮过硬,进刀量大、磨削速度快,磨削应力过大,冷却不足或是冷却液选择不当所致。由硬砂轮引起的摩擦热所产生的拉伸应力大于材料的断裂韧性时,就会产生开裂;
B、磨削烧伤、表层软化。软化的表面在与熔化的压铸金属相接触时,因其强度比较低,而且热疲劳强度也不足,容易导致产生龟裂、冲蚀和麻点。
C、磨削应力。模具表面的磨削存在磨削应力,降低了模具表面的强度和热疲劳抗力,会导致在模具型位拐角和小 R 圆弧过渡处产生龟裂或裂纹,它可以通过低于回火温度 20~30℃的温度下进行一次回火处理,达到消除应力的目的。
3、 放电加工的影响
A、 产生淬硬的白亮层
放电加工(电火花和线切割)模具型腔,一般是在模具淬火后进行的,以确保模具的精度。在加工过程中,由于一次放电瞬间产生的高温(温度高达数千摄氏度,甚至上万摄氏度),使模具表面金属快速熔融、气化、蒸发。应用冷却液快速冷却的结果,自表面往里依次为:再凝固层(粗打时厚度达 0.2mm,精打时达 0.01mm 左右),再淬火硬化层(其厚度一般在 0.05mm 以内,最表面一侧出现过热淬火组织,脆而裂纹敏感性高),高温回火软化层和正常基体组织。在这种硬化层的内部,特别是在再凝固层产生许多微细裂纹,裂纹甚至延伸到再淬火硬化层(常称为白亮层或变质层)。它的存在会引起模具早期龟裂或开裂等事故。(例如,汽车的离合器壳体、变速箱体等模具镶块均常出现这种情况)。因此,应采用人工研磨、化学研磨或电解研磨等充分消除此变形层是十分必要的。
B、电火花加工表面粗糙度和疲劳强度关系,其与放电加工的电规准参数、电极材料有关,与机加工相比,其疲劳强度低很多。粗打时,在脉宽 1050μ s 时其疲劳强度约为机加工的 60%。
C、防护措施
不论放电加工白亮层的深浅如何,对于工况恶劣的压铸模具来说,此白亮层必须予以消除(打磨);调整放电工艺参数,最好进行粗、精两级放电加工尽量使用高频率、小电流工艺参数,控制白亮层在 0.01mm 左右;放电加工后,除了打磨去除掉白亮层,还必须立即进行足够长时间的二次回火。回火温度通常比最终回火温度低 20~30℃或 30~50℃,以充分消除表面的拉伸应力,提高再淬火层的回火稳定性,降低脆性。
总的来说,模具表面的切削、磨削和放电加工的缺陷均会降低模具表面的质量造成应力集中。对于在高温高压工作状态下的压铸模具,承受交变热应力和交变机械应力的作用,模具表面容易产生龟裂和开裂及腐蚀,使模具出现早期失效。(当然还有受钢材质量、设计、热处理、使用、保养等诸多因素的影响)。所有这些都值得模具设计工程师、技术工艺师、生产操作者和质检人员的高度重视。提出合理的模具表面质量要求,尽量避免零件尖角和小半径圆弧过渡连接及明显刀痕,控制好放电加工的电规准参数,消除白亮层等。要制定切削加工、放电加工和钳工打磨的粗糙度验收标准,严格执行各工序检验制度。这将会有效的避免模具因加工不当引起的早期失效,提高模具的使用寿命。
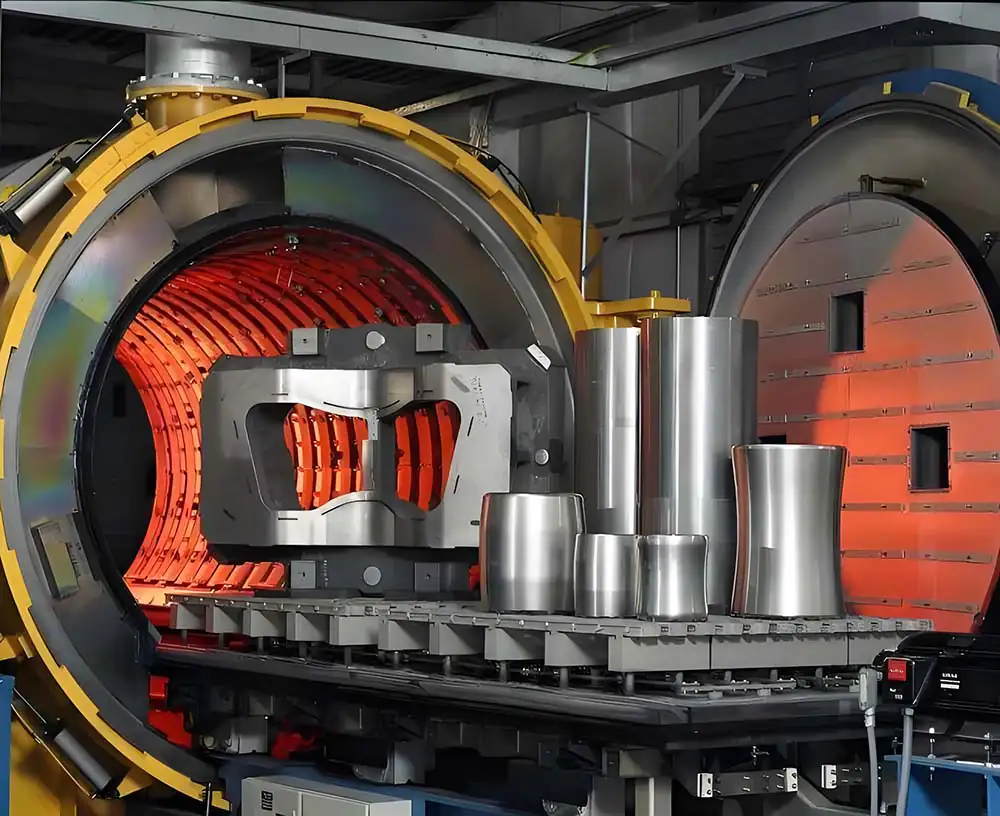
压铸模具热处理注意事项:
热处理对于压铸模具使用寿命的影响较大,据有关资料介绍,由于热处理不当,造成压铸模具早期失效占整个压铸模具事故的 44%左右。钢淬火时所产生的应力,实际上是冷却过程中的热应力与相变时的组织应力叠加的结果,钢淬火后处于高应力低韧性状态,具有高硬度和强度,较脆,实际上不能使用。而淬火应力是造成变形开裂的原因,并导致疲劳强度冲击韧性降低。为此,钢淬火后必须进行回火,去除应力。稳定组织,提高韧性。
1、 模具淬火前去应力退火处理
由于模具机加工时产生较大的内应力,为防止与热处理时产生内应力迭加,引起模具变形和开裂,故要求模具在机加工后、淬火前进行一次去应力退火处理。退火温度 600~650℃,保温时间按照厚度每 25mm,保温 1 小时计算,保温随炉冷却至 300℃(也有冷至 500℃)出炉空冷。
2、 制定合理的热处理工艺
A、 淬火工艺采用多段预热和严格控制升温速度1.2343/44 类型钢属于中碳高合金钢,相对于低合金钢其导热性能较差。因此淬火加热应采用多段预热(2~3 段),为 300℃、650℃、850℃预热,目的是使工件心部和表面的温度趋于平衡,以减少温差产生的热应力。同时其升温速度应执行缓慢加热的原则(100~200℃/h),以减少加热过程中产生的热应力。在高温加热阶段可采用较快升温速度(10~15℃/h)以缩短高温加热时间,防止晶粒粗大;
B、防止工件过热现象
若加热阶段温度超过正常的淬火温度(包括仪表失灵或工件摆放靠近加热元件等引起的),随着淬火温度的提高,保温时间的延长,晶粒普遍粗化,组织脆性增加,残余奥氏体增加,球状碳化物转变为多角状碳化物,并且有网状组织出现,模具在使用过程时容易出现开裂;
C、淬火加热介质和冷却介质的选择
当今世界对于大型复杂精密模具多采用真空或保护气氛下热处理,以防止模具表面氧化脱碳,尤以真空高压气冷淬火工艺应用广泛。但要注意,气冷速度不能太低,那就要求氮气的压力大小足够,通常要求工件从淬火温度(1020~1050℃)冷至 538℃过程中,其表面冷却速度大于等于 28℃/分,也有要求工件心部冷却速度大于等于 28℃/分。如果该温度段,冷却速度太慢,则淬火后其显微组织会有碳化物或其他转变产物沿晶界析出,从而降低钢的韧性,增加脆性,在使用过程中过早开裂。另外有条件者,对于特别复杂的大型压铸模具可采用分级等温淬火,能有效的减少模具变形和避免开裂。
D、回火工艺
淬火后要及时回火。工件淬火后冷却至 90~70℃应立即进行回火,因为工件淬火后处于高应力、低塑性状态,容易引起开裂;回火要充足。大型复杂压铸模具淬火后,通常进行三次回火,每次回火时间按工件有效厚度每 25mm 保温 1 小时计算,但不少于 4 小时。目的是减少组织转变应力和稳定尺寸。
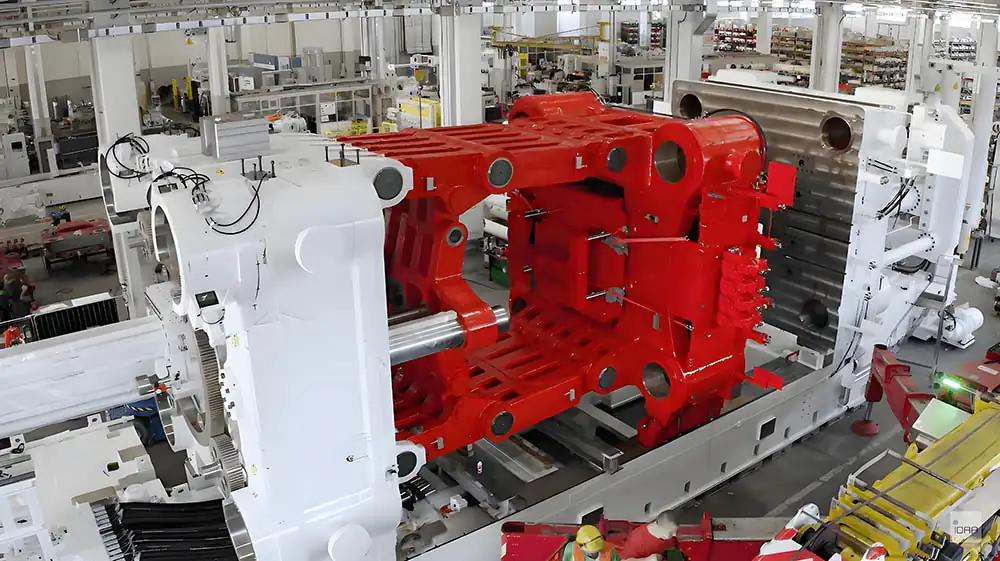
压铸模具压铸生产和维护注意事项
1、 模具的良好预热
模具装配后试模或正常生产,必须预热模具而且模温要均匀。铝镁合金的压铸模具的预热温度建议在 250~320℃,最好采用模温机预热;模具预热到 300℃,其冲击韧性提高很快,但当模温低于 200℃时,材料的冲击韧性降低很多,脆性增加;经过良好预热的模具,其热传导率要比没有良好预热的模具高近 20%;模具浇注温度与模具表面温度(预热温度)之差越大,则热应力越大,越容易引起热疲劳和龟裂。日本压铸协会编辑资料介绍,模具温度从 250℃提高到 350℃,即浇注温度与模具表面温度之差减少 100℃,则模具寿命几乎可以提高 10 倍。
2、 制定正确的浇注工艺
浇注温度要合理,不能太高。否则浇注温度太高,虽然流动性更好,但铸件冷凝时间长,易产生缩孔,气孔,容易降低模具表面硬度,出现粘模、产生龟裂。调整压铸机的锁模力,使模具受力均匀。正确选择(或调整)充型速度和充型压力。充型速度(压射速度)过高会增大型腔表面由于侵蚀和粘模的损伤几率,过低充型速度,虽然有利于气体排出,但会使铸件机械性能下降和表面质量变坏。同理,充型压力增大,也会使喷嘴充型速度增大。总之,要调整一个适度的数值。
3、 生产时关闭冷却水
在中断压铸浇注作业时,切记要关掉冷却水,以免使模具温度下降太多,以致恢复浇注作业时,影响铸件质量和模具寿命。
4、 选择合适的脱模剂及正确的喷涂方式
压铸时要将脱模剂喷涂在于金属溶液接触的型腔表面,其主要作用是避免金属液粘附在型腔表面和保证铸件与型壁分离,延长模具寿命。脱模剂有水剂、油剂,近年来还研制出粉剂和颗粒状脱模剂。要求:脱模剂不能对铸件表面质量有不良的影响,无气味冒烟发生,也不得留下残留物。脱模剂浓度要适当,要经常搅拌,千万不能让其沉淀,否则模具型腔会因为极冷引起热疲劳龟裂。喷涂量要少,喷的要均匀,形成的膜要薄。喷涂太多太厚会造成铸件疏松、夹渣、起泡、气孔等缺陷。如水剂脱模剂喷涂效果不佳,应选择油剂脱模剂或粉剂脱模剂。但要在真空状态下使用。铸件脱模快、生产率高、质量好,而且模具产生的热应力较少,有利于延长模具使用寿命。
5、 确保浇注的铝合金质量保证铝合金的成分;
铝合金熔化与保温槽必须分开。中央熔炼要严格控制气体如氧化物的含量、绝对避免把废品和回炉料直接加入保温炉中,否则会污染金属液,不但严重降低铸件的质量,更会容易造成粘模及腐蚀模具。铝合金溶液 Fe 的含量应控制在 0.7~1.3%之间,如果低于 0.7%则容易引起粘模现象,如果大于 1.3%则会形成金属化合物硬质点,产生冲蚀。
6、 建立良好的模具维护制度,使模具处于良好的工作状态:
A、及时清洗和打扫模具,去除型腔残留物和飞边;B、更换或修复已损坏的零件;C、定期对模具进行消除应力处理:第一次去应力处理为,初期投产模具使用约 2000~5000 模次时;第二次去应力处理为,使用 10000~20000 模次时;其余每次去应力处理间隔同上,最大不能超过 15000 模次。D、模具使用一段时间之后,检测模具表面硬度有所降低,出现粘模现象时,应将模具表面研磨光滑,进行一次软氮化处理,渗氮层厚度为 0.08~0.12mm,或软氮化+氧化复合处理,它将有效的提高模具的使用寿命。