低压铸造铝轮毂裂纹形成原因及改进措施
发布时间:2025-01-27 分类:新闻 浏览量:1365
低压铸造 可以实现高度机械化和自动化,提高生产率(10~15型/h) ,它还可以减少许多不利于生产过程的人为因素,提高成品率,大大降低工人的劳动强度。然而,低压铸件的质量受到工艺方案、工艺参数、模具结构和人工操作等因素的影响,任何设计不合理或操作不当的环节都可能导致低压铸件的缺陷。铝轮毂裂纹的产生是影响企业生产成本、生产效率的重要因素。因此,探讨低压铸造铝轮毂裂纹的原因尤为重要。接下来,小编将与您讨论在中国低压铸造工厂铸造 铝合金 汽车轮毂裂纹的形成和消除措施。
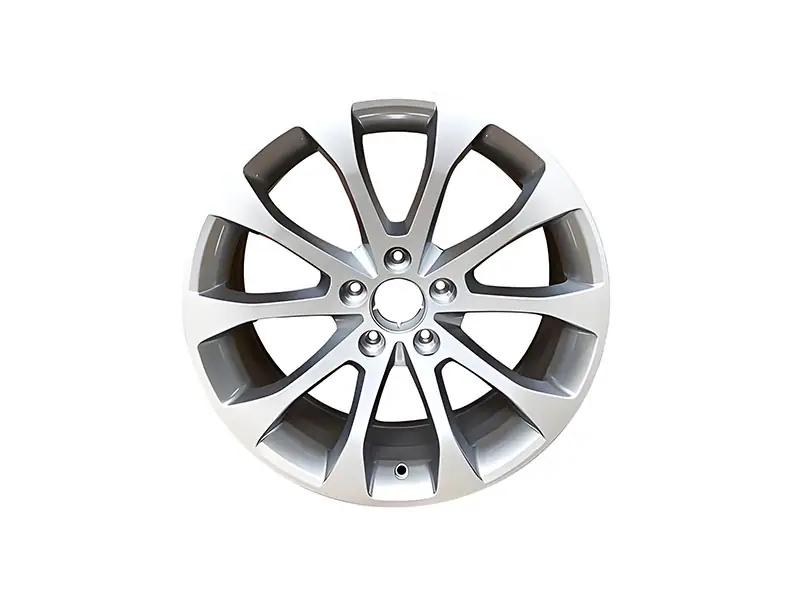
什么是低压铸造轮毂?
低压铸造轮毂通过低压铸造技术制造,具有高密度、高强度和良好的质量控制。该工艺将液态合金在低压下注入模具,合金在模具中冷却并凝固。低压铸造产生的轮毂密度高,结构均匀,强度和韧性良好,适合大规模生产。
生产过程分为几个步骤:首先,液态合金被注入模具;接着,合金冷却固化;最后,通过热处理、修饰和喷涂等工艺,完成轮毂。该过程减少气泡和杂质,提高强度与精度,增强轮毂的安全性。
与重力铸造相比,低压铸造更高效,产品质量更好。重力铸造依赖重力流动金属,可能导致不均匀分布,影响质量和安全。低压铸造通过施加压力,控制铝合金流动,确保轮毂精度和强度。
因此,低压铸造轮毂在汽车制造中越来越重要,提供高效率、高质量且安全的产品。
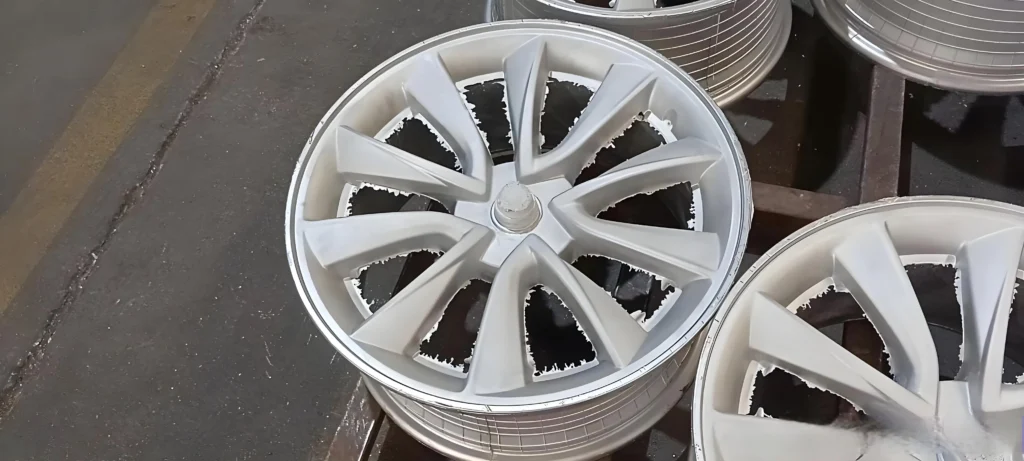
低压铸造轮毂技术优势与产业价值重塑
机械自动化驱动的精密制造革命
低压铸造技术通过高度机械化和自动化生产,实现了每小时10~15件的稳定产能,较传统重力铸造效率提升约30%。其核心原理是利用低压气体(0.02-0.08MPa)将液态铝合金平稳压入模具型腔,避免了重力铸造中金属液自由流动导致的卷气、氧化夹渣等问题。以某新能源汽车轮毂量产项目为例,通过引入全自动低压铸造线,产品良率从82%跃升至96%,同时人力成本降低45%。模具温度闭环控制系统与智能压力传感器的结合,使得铸件内部晶粒细化至微米级,轮毂动态弯曲疲劳寿命突破100万次循环,充分满足高端车型对轻量化与安全性的双重需求。
低压铸造轮毂裂纹成因的跨学科诊断
裂纹形态学与失效机理的深度关联
在铝合金轮毂生产过程中,裂纹的形成往往是材料特性、结构设计、工艺参数等多因素耦合的结果。根据断裂力学分析,轮毂裂纹可分为三大类型:
- 热裂(凝固缺陷):多发生于轮辐与轮辋连接处,表现为沿晶界分布的网状裂纹。其本质是凝固末期枝晶骨架间的残余液态金属无法承受收缩应力,典型案例显示,当局部冷却速率超过4℃/s时,热裂概率增加60%。
- 冷裂(机械应力):常见于轮毂法兰根部,断口呈现典型的脆性断裂特征。某商用车轮毂的失效分析表明,脱模时升液管残留的凝固金属导致铸件承受超过200MPa的拉应力,直接引发贯穿性裂纹。
- 应力腐蚀裂纹(环境交互):在沿海高湿度环境中,轮毂内部残余应力与氯离子协同作用,导致裂纹沿晶界缓慢扩展。此类裂纹在显微观察中呈现独特的树枝状分叉形貌。
关键致裂因子的系统性分析
1. 结构设计缺陷的力学放大效应
- 尖角应力集中:轮辐过渡区域的内圆角半径若小于3mm,应力集中系数(Kt)可达3.5-4.2,远超A356-T6铝合金的屈服强度(220MPa)。某运动型轮毂的仿真数据显示,将R角从2mm优化至5mm后,最大等效应力从315MPa降至185MPa。
- 壁厚突变效应:当相邻区域壁厚差异超过3:1时,冷却过程中产生的热应力梯度可突破材料抗拉强度极限。某轻量化轮毂的断裂案例显示,轮辋与轮辐连接处厚度从8mm骤减至3mm,导致局部应力峰值达到280MPa。
2. 工艺参数失配的系统性风险
- 保压时间窗口狭窄:保压时间不足15秒会导致补缩中断形成缩松,超过40秒则升液管金属凝固产生机械阻力。某项目DOE试验证实,保压时间控制在25-30秒区间时,裂纹发生率从7.2%降至0.8%。
- 充型速率控制失当:当充型速度超过120mm/s时,金属液紊流卷气概率提升40%,气体滞留形成的微观缺陷成为裂纹萌生起点。采用阶梯升压工艺(初始0.03MPa,终段0.06MPa)可有效平衡充型速度与卷气风险。
3. 模具热管理的动态平衡挑战
- 温度梯度失控:模具温差超过50℃时,铸件各区域凝固收缩差异率超过0.8%,诱发热裂。某工厂通过植入模温监测点发现,轮辐区域温度波动达±30℃,加装分区控温系统后温差稳定在±5℃以内。
- 冷却介质选择不当:传统水冷易导致模具表面温度骤降,采用气雾混合冷却技术可将冷却速率精准控制在3-8℃/s,避免因激冷产生淬火应力。
裂纹防治的工程级解决方案
1. 升液系统动力学优化体系
- 流道几何重构:将升液管直径从Φ60mm增至Φ85mm,配合30°倾斜流道设计,使金属液流速稳定在0.8-1.0m/s。某项目实践表明,此举使升液管冻结概率降低70%。
- 保温材料升级:采用纳米微孔保温套(导热系数≤0.1W/m·K),较传统陶瓷纤维材料保温时效延长40%,确保补缩通道畅通。
2. 结构设计的仿生学优化路径
- 应力流线映射技术:基于拓扑优化算法重新分配轮辐材料,使主应力方向与加强筋走向一致。某轻量化轮毂通过此技术减重12%,同时弯曲刚度提升18%。
- 渐变过渡法则:在壁厚突变区域设计1:4锥度过渡带,并在轮辐根部增设深度1.5mm的应力释放槽,成功将局部应力峰值从295MPa降至175MPa。
3. 模具智能温控系统创新
- 多区段耦合控温:开发六区独立温控模块,轮辋区设定320℃(促进补缩),轮辐区保持280℃(抑制热裂)。某高端品牌轮毂量产中,该系统使模温均匀性达到±3℃。
- 动态冷却策略:充型阶段采用气冷维持模温,保压阶段切换雾冷加速凝固,使整个生产周期缩短8秒。
宁波贺鑫的工艺创新实践
在与某德系豪华品牌的合作中,贺鑫团队通过三项关键技术突破实现行业标杆:
- 低压铸造-旋压复合成形技术:在轮辋部位叠加旋压工艺,使晶粒沿周向定向排列,轮毂径向冲击强度提升35%。
- 梯度加热系统(专利技术):模具表面镀覆0.2mm厚氮化钛涂层,配合感应加热装置,实现轮辐区域温差≤5℃的精准控温。
- 数字化工艺仿真平台:集成MAGMAsoft与ANSYS系统,将试模次数从12次压缩至3次,开发周期缩短60%。
选择合适的低压铸造轮毂工厂
优质供应商需具备四大核心能力:
- 材料数据库:积累数万组工艺参数与合金性能的映射关系,快速匹配最佳材料方案
- 全流程品控:从铝锭纯度分析(Fe含量≤0.15%)到X射线探伤(ASTM E505标准),建立12道质量关卡
- 柔性化生产:兼容16-24寸轮毂的快速换模系统,切换时间<45分钟
- 绿色制造:铝屑回收率≥95%,单位产品能耗较行业均值低28%
常见问题及解答
1. 为何低压铸造轮毂更适合新能源汽车?
其高致密性可承受电机瞬时扭矩(≥3000N·m),而轻量化特性(较钢轮毂减重40%)直接提升续航里程5%-8%。
2. 如何通过金相分析判断裂纹成因?
- 热裂:晶界处存在连续氧化物膜,裂纹呈曲折网状
- 冷裂:断口平直,可见明显解理台阶
- 应力腐蚀:裂纹尖端存在Cl元素富集(EDS检测)
3. 模具寿命如何影响裂纹率?
当模具使用超过5000模次后,表面微裂纹会导致铸件脱模阻力增加25%,需定期进行激光熔覆修复(恢复表面硬度至HRC 45以上)。
4. 未来技术发展方向是什么?
将人工智能引入工艺优化,通过机器学习算法实时调控压力曲线,目标是将裂纹率控制在0.1%以下,同时生产效率再提升20%。