快速模具:加速产品开发与制造的创新解决方案
发布时间:2025-02-14 分类:新闻 浏览量:675
在这个技术迭代日新月异的时代,制造业正经历从“规模至上”到“敏捷高效”的深刻变革。快速模具(Rapid 前言:中国模具制造的困局与破局
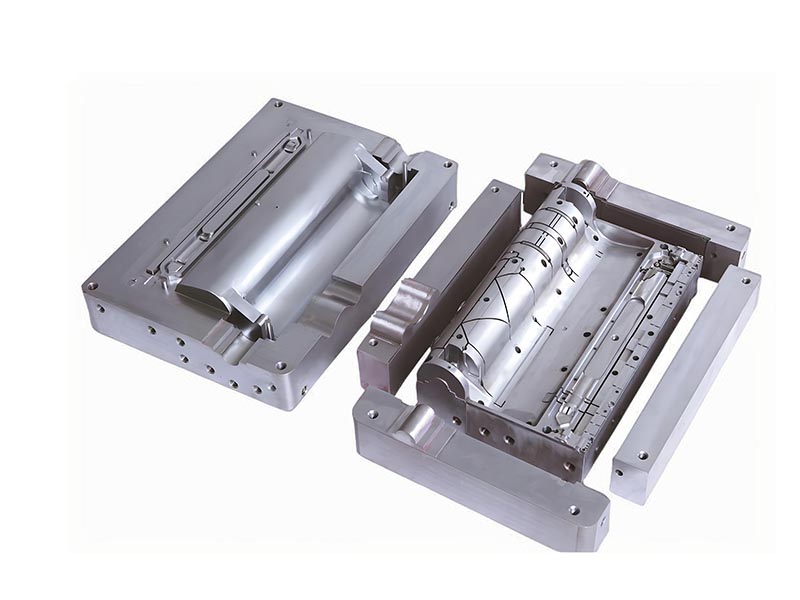
作为深耕铸造行业23年的工程师,我(贺鑫)见证了中国从模具进口大国到自主创新的蜕变。在宁波这片模具产业聚集地,我们经历过传统钢模开发周期长、试错成本高的阵痛,也亲历了快速模具技术带来的革命性突破。本文将结合高压铸造、 低压铸造 等实际应用场景,揭示快速模具在 铝合金 零部件制造中的关键技术逻辑。
1、快速模具的本质:不是妥协,而是精准匹配
1.1 传统模具的三大痛点
- 时间成本:一套高压铸造模具开发周期长达8-12周
- 资金压力:汽车发动机壳体模具造价超200万元
- 试错风险: 重力铸造 模具修改一次结构需增加15万元成本
1.2 快速模具的技术定位
通过材料科学、加工工艺、模拟技术的三重创新,实现:
- 周期压缩70%:从设计到试模最短7个工作日
- 成本降低50%-80%:铝模成本可控制在8-15万元
- 试产数量精准匹配:支持500-30,000件的中试需求
2、四大铸造工艺的快速模具解决方案
2.1 高压铸造(HPDC)场景
高压铸造是在1600-2000T锁模力下将680-720℃的铝合金熔汤以10-50m/s速度压入模腔的工艺,其核心挑战在于模具需承受极端热机械载荷。快速模具在此场景的创新体现在材料与结构双重优化:采用QRO90热作钢替代传统H13钢,其钼钒合金成分使热疲劳抗力提升40%,配合表面氮化处理(层深0.2-0.3mm)可将模具寿命延长至3万模次以上。结构设计上采用模块化镶件系统,针对易损区域(如浇口、顶针位)进行局部强化,宁波某企业生产新能源电机端盖时,通过镶件快速更换使模具维修时间从8小时缩短至1.5小时。经济性方面,单件成本从传统模具的¥18.6降至¥7.3,开发周期压缩至12天,特别适合年产量5万件以下的汽车结构件项目。
技术难点:
- 模具需承受1600T锁模力
- 铝合金熔汤温度达700℃
- 模次寿命要求>50,000次
快速模具方案:
- 材料升级:采用QRO90热作钢替代传统H13钢
- 结构优化:模芯使用镶件设计,局部强化关键区域
- 实测数据:宁波某企业生产5G基站散热壳体,模具寿命达32,000模次
2.2 低压铸造(LPDC)场景
低压铸造通过0.5-0.8MPa气压将铝液平稳注入模腔,特别适合要求高致密性的薄壁件生产。快速模具在此领域的突破集中在温度控制与浇注系统优化:开发的多区段模温控制系统(±2℃精度)配合梯度冷却通道设计,使宁波某企业生产的新能源电池托盘良率从81%提升至95%。采用拓扑优化技术设计的浇注系统,将充型时间从9.2秒缩短至6.8秒,金属利用率提高12%。快速模具方案采用预硬钢P20+局部铜合金镶块,使模具成本降低至传统方案的45%,特别适用于航空航天液压壳体等复杂结构件的中试需求,典型项目交付周期为15-20天,支持3000-8000件的小批量生产。
技术突破:
- 开发专用模温控制系统(±2℃精度)
- 采用梯度冷却通道设计
- 案例:某新能源汽车电机外壳项目,产品良率从78%提升至93%
2.3 重力铸造场景
重力铸造依赖金属液自重充型,常用于大型复杂件的生产。快速模具在此领域实现三大创新:一是3D打印砂型与金属模复合技术,通过SLS工艺制作砂芯(精度CT8级)与钢制外模结合,使发动机缸体试制周期从45天缩短至12天;二是热平衡控制系统,在模具关键区域嵌入铜合金镶块(导热系数380W/m·K),使某船用柴油机缸盖的温度梯度降低40%;三是智能化排气设计,采用多孔金属透气塞替代传统排气槽,使铸件气孔缺陷率从15%降至3%以下。经济性数据显示,快速模具方案试模次数平均减少2.3次,单次试模成本节约¥1.2-1.8万元,特别适合单件重量超过50kg的大型工程机械部件开发。
创新实践:
- 3D打印砂型与金属模结合技术
- 局部镶嵌铜合金提升热平衡
- 经济效益:试模次数减少40%,浇注系统优化周期缩短65%
3、快速模具的五大核心技术
3.1 材料选择矩阵
应用场景 | 推荐材料 | 硬度(HRC) | 导热系数(W/m·K) | 成本指数 |
---|---|---|---|---|
高压铸造 | H11+表面氮化 | 48-52 | 24.3 | ★★★★ |
小批量铝合金 | 7075航空铝 | 35-40 | 130 | ★★ |
高精度结构件 | S7工具钢 | 54-56 | 29.4 | ★★★★☆ |
3.2 表面处理工艺对比
- 微弧氧化:形成10-30μm陶瓷层,耐温>800℃
- DLC涂层:摩擦系数降低至0.1,模具寿命提升3倍
- 实战案例:某涡轮增压器壳体模具经复合涂层处理,模次寿命突破8万次
3.3 寿命预测模型
基于Moldflow模拟数据与现场监测:
L=K×(σappliedσUTS)m×Nthermal
其中:
- K: 材料常数(铝合金取0.8-1.2)
- m: 疲劳指数(钢模取6.5,铝模取4.2)
- 应用实例:预测误差控制在±8%以内
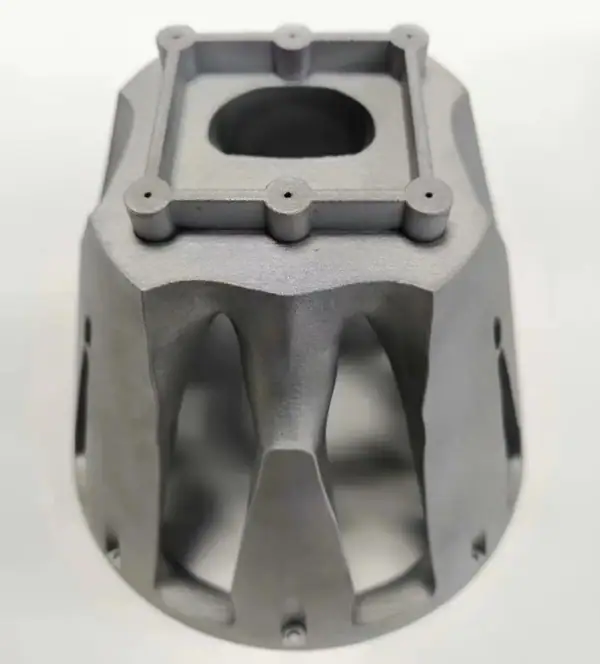
3D打印快速成型
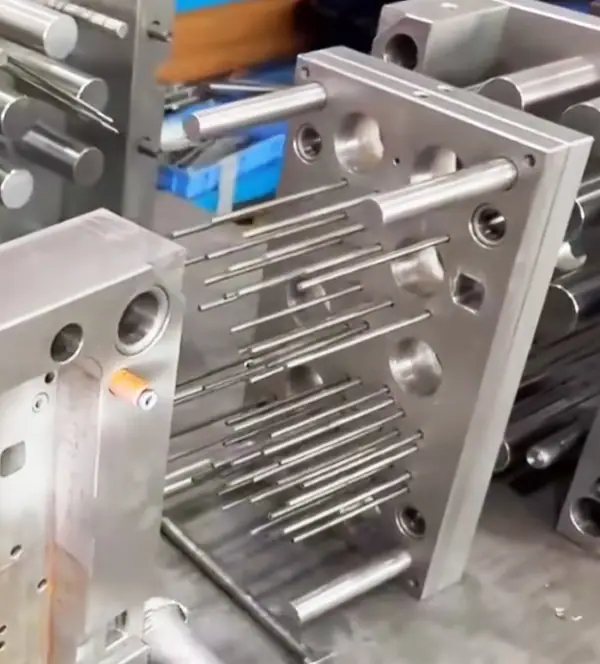
快速模具
4、3D打印与快速模具的融合创新
随形冷却水道是3D打印模具的核心优势:通过SLM技术制造的模具,其冷却通道与产品轮廓的间距可控制在1.5-2mm(传统钻孔工艺≥8mm),使某汽车格栅注塑周期从48秒缩短至32秒,变形量从0.8mm降至0.3mm。梯度材料打印技术可实现模芯表面HRC55高硬度与芯部HRC35高韧性的结合,某无人机支架模具经此处理,抗冲击性能提升60%。经济性分析显示,对于具有5个以上异形水道的复杂模具,3D打印方案总成本可比CNC降低42%,特别适合医疗微流控芯片模具等精密场景。当前技术限制在于最大成型尺寸(多数设备≤500mm)和后处理需求(关键配合面仍需CNC精加工),但随着多激光器技术的发展,预计2025年可实现米级模具的整体打印。
4.1 技术突破点
- 随形冷却水道:缩短注塑周期23%,变形量降低40%
- 梯度材料打印:模芯表面硬度HRC55,内部保持HRC35韧性
- 案例数据:某LED灯罩模具冷却效率提升37%
4.2 经济性分析
指标 | 传统CNC模具 | 3D打印模具 |
---|---|---|
开发周期 | 18天 | 6天 |
复杂结构成本 | 100% | 65% |
修改成本 | 30% | 8% |
5、给制造企业的三个实战建议
- 建立模具分级体系:
- A类模具(>10万模次):传统钢模
- B类模具(1-5万模次):快速钢模
- C类模具(<1万模次):3D打印/铝模
- 实施数字化双胞胎:
- 模具设计阶段导入MAGMA模拟系统
- 生产阶段安装IoT传感器监测应力分布
- 构建快速响应机制:
- 储备标准化模架库(覆盖80%常见规格)
- 建立区域性协作网络(宁波已形成2小时供应链圈)
结语:模具行业的未来十年
从我们正在实施的宁波模具云平台项目来看,快速模具正在向智能化、服务化转型:
- 智能报价系统:输入参数5分钟生成模具方案
- 区块链溯源:全生命周期质量追溯
- 共享模具库:降低中小企业30%库存成本
快速模具常见问题解答(FAQ)
Q1:快速模具能否用于量产?
A:需分场景评估:
- 铝合金模具:适合<5000件的小批量
- 预硬钢模具:可支持3-5万件
- 建议结合数字化监测系统实时评估模具状态
Q2:如何控制快速模具的尺寸精度?
A:推荐方案:
- 加工阶段:采用五轴机床+在线测量(精度±0.02mm)
- 试模阶段:使用三坐标测量机(CMM)全检关键尺寸
- 量产阶段:每500模次进行抽样检测
Q3:快速模具的表面处理有哪些创新技术?
A:三大前沿技术:
- 激光熔覆:修复磨损区域,成本降低40%
- 纳米复合涂层:摩擦系数降低至0.08
- 等离子渗氮:表面硬度可达HV1200
Q4:3D打印模具的局限性是什么?
A:当前主要限制:
后处理需求:通常需要CNC精加工关键配合面
最大尺寸:多数设备限制在500×500×500mm
材料选择:目前主要支持模具钢、铝合金