汽车铝压铸件轻量化应用的技术路径与实践探索
发布时间:2025-03-04 分类:新闻 浏览量:575
作者:宁波贺鑫模塑有限公司高级工程师(20年铸造行业经验)
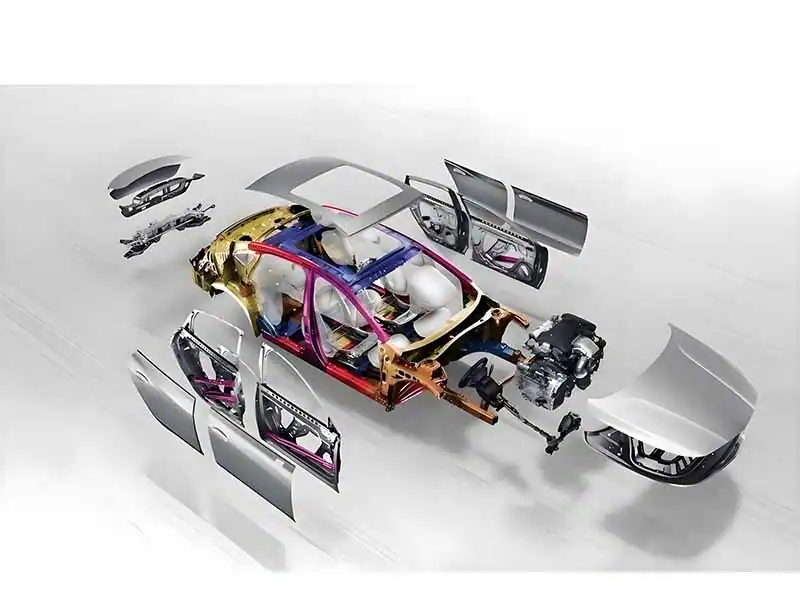
1、铝合金材料的战略价值
随着全球碳减排政策持续深化,汽车工业正经历从"以钢为主"向"多材料协同"的结构转型。 铝合金 材料凭借其低密度特性与可循环优势,成为实现整车轻量化的核心突破口。在新能源车型架构中,铝合金压铸件已渗透至车身框架、三电系统、底盘结构等关键领域,形成覆盖全车身的轻量化解决方案。
当前产业实践表明,采用模块化压铸技术可大幅降低零部件数量与装配复杂度。典型案例显示,通过结构整合与工艺革新,某车型白车身成功实现材料减重与产线效率同步提升。这种技术路径不仅响应了节能减排需求,更为车企创造了显著的经济效益。
2、铝压铸工艺技术体系
2.1主流工艺对比
通过真空辅助技术与模具智能温控系统,现代压铸工艺已突破传统壁厚限制,实现更复杂的轻量化结构设计25。
2.2技术创新方向
- 一体化成型:将多零件整合为单一构件,减少连接工艺与材料冗余。
- 复合工艺开发:融合铸造与锻造技术,提升关键部件力学性能。
- 数字化仿真:通过CAE模拟优化浇注系统设计,降低工艺开发成本。
3、行业应用实践
3.1 车身结构革新
全铝车身技术通过拓扑优化设计与高强韧合金应用,在保证碰撞安全性的前提下大幅降低白车身重量。典型车型已实现车体铝压铸件占比过半,显著提升续航与操控性能。
3.2 三电系统升级
驱动电机壳体等关键部件采用薄壁化压铸方案,在满足密封防护需求的同时突破传统重量限制,助力提升能量利用效率。
4、产业链协同发展挑战
技术瓶颈 | 创新解决方案 | 协同效应体现 |
---|---|---|
超大构件形变控制 | 开发多维度补偿模具系统 | 提升尺寸精度稳定性 |
材料回收利用率 | 构建光谱分选-熔炼一体化装置 | 降低碳排放指标 |
工艺稳定性 | 部署在线监测与机器学习系统 | 实现缺陷实时预警 |
行业龙头企业正通过智能化压铸岛建设,将工艺参数控制精度提升至新量级。某生产基地引入全流程MES系统后,关键质量指标波动幅度收窄显著。
5、未来技术演进方向
- 超大型压铸装备:推动前舱/后底板模块化生产普及。
- 数字孪生技术:构建虚拟调试平台缩短新品开发周期。
- 低碳制备体系:完善再生铝供应链实现绿色制造。
当前技术突破已延伸至材料-工艺-装备协同创新层面,某新型压铸生产线通过能源回收系统,成功将单位能耗降低至行业先进水平。
结语
汽车铝压铸轻量化已从局部替代发展为系统性工程解决方案。作为拥有全产业链服务能力的铸造企业,我们将持续深耕材料改性、工艺集成与智能制造领域,为全球汽车工业的绿色转型提供技术支撑。