压铸技术:将愿景化为现实的关键制造工艺
发布时间:2024-12-24 分类:新闻 浏览量:1050
在现代制造业中,压铸工艺被视为精密金属零件制造的重要手段。它通过高压将熔融金属注入精密模具,能够生产复杂形状的金属部件,广泛应用于汽车、电子等领域,支撑了多个领先行业的技术发展。本文将深入分析压铸工艺的核心流程、材料选择及应用,以及这一工艺如何在制造业中实现创新和卓越。
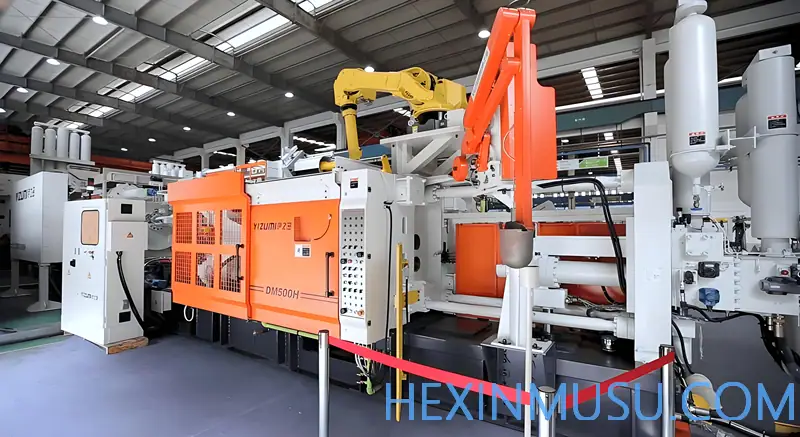
什么是压铸?
压铸是一种高效、精确的金属铸造方法,利用可重复使用的模具生产复杂形状的金属零件。与传统铸造工艺不同,压铸通过高压将熔融金属注入模具,尤其适合于大批量生产,能够提供高精度、可重复性以及优异的表面光洁度。
压铸工艺最初用于印刷行业,但其广泛应用潜力很快扩展到了多个领域,包括汽车、航空航天和电子行业。如今,压铸主要使用铝、锌、镁等轻金属,满足从小型复杂部件到重要汽车零件等多种产品的制造需求。压铸的核心优势在于其能够制造具有极小公差、减少后续加工需求的零件,这使得它成为现代制造业中不可或缺的技术。
压铸工艺流程
压铸的生产流程可分为多个关键步骤:
- 模具准备
模具是压铸工艺的基础,常见的模具类型包括单型腔模具、多型腔模具和组合模具。模具设计需要考虑零件的复杂性和生产规模,模具在使用前需要进行清洁和预热,避免裂纹和热缺陷的产生。 - 注射过程
注射过程中,熔融金属在不同系统中熔化并注入模具。对于热室系统,熔化发生在铸造机内部,而冷室系统则将熔融金属倒入冷室,再通过压力将其注入模具。 - 冷却与凝固
熔融金属在模具中冷却并凝固,形成最终零件。冷却过程需要控制压力,以防止零件因收缩而出现缺陷。 - 弹射
一旦金属完全凝固,模具被打开,机器顶针将零件推出。 - 修整与后加工
为确保零件质量,需要去除多余的材料和毛边。必要时,还可通过磨削等后加工方法进一步提高零件的精度。
压铸的类型
根据熔化和注射过程的不同,压铸工艺可分为热室压铸和冷室压铸两种主要类型:
- 热室压铸
适用于低熔点金属,如锌和某些铝合金。该工艺通过连接到压铸机的熔融金属储罐,利用气动柱塞将金属注入模具。它具有高效、快速的特点,适合大批量生产小型零件,常见于消费电子产品的生产中。 - 冷室压铸
用于高熔点金属,如铝和铜合金。在冷室压铸中,熔融金属先倒入冷室,再通过柱塞将金属注入模具。这种工艺适合于需要较高强度和耐热性能的零部件,广泛应用于汽车和航空航天领域。
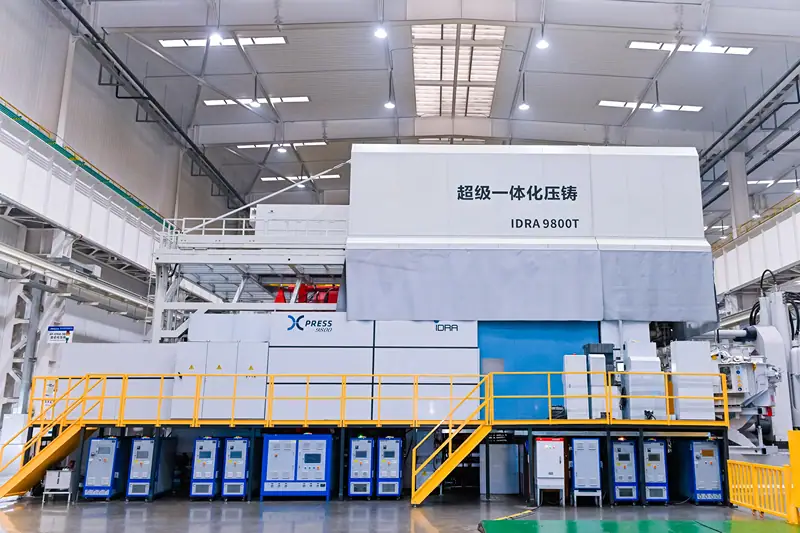
压铸的变种与创新
随着技术的不断发展,压铸工艺也出现了多种变种和创新,以满足不同工业需求。例如:
- 重力压铸:利用重力将熔融金属注入模具,适用于大批量精密铸件的生产。
- 压力压铸:通过低压或高压填充金属,适用于生产精度要求高的零件,如汽车和航空航天零件。
- 真空压铸:通过创造真空环境,减少空气滞留,提高表面质量和尺寸精度,适合高端产品。
- 挤压压铸:可提高零件的机械性能和精度,常用于汽车零部件。
- 半固态压铸:通过特定的铸造温度,生产复杂几何形状的零件,具有更高的精度和强度。
压铸的优缺点比较
金属压铸作为一种广泛应用于工业生产的制造工艺,其优点使得它在大批量生产中占据了重要地位。然而,它也存在一些局限性,可能影响其在某些应用场景中的使用。以下是压铸的主要优缺点及其原因分析:
压铸的优点
- 极佳的尺寸精度
金属压铸能够生产尺寸精度高的零件,特别适用于需要严格公差的应用。精度取决于模具设计和制造工艺,特别是当模具使用高精度数控机床(如5轴数控机床)制造时,能实现更高的尺寸精度。此外,采用低压压铸(LPDC)和重力压铸等工艺变体,有助于模具的准确填充,从而提高零件的精度。 - 复杂的几何形状
压铸能够制造具有复杂几何形状的零件,包括铸件、薄壁等设计。这一特点使得压铸在航空航天、汽车和消费电子等领域中,能够生产出结构复杂、功能多样的零件。通过这种方式,设计人员可以将更多的功能集成到单一零件中,减少了后续的装配需求。 - 大批量生产,快速交付
压铸是一种大批量生产工艺,适合制造大量的零件。在高压铸造中,由于使用的高压力,生产速度较快,从而降低了单位零件的生产成本。特别是在使用组合模具的情况下,可以同时制造多个零件,提高生产效率和单件的成本效益。 - 光滑的表面处理
由于压铸过程中高压力注入金属,铸造金属零件通常具有光滑的表面光洁度,尤其是在低压铸造、重力铸造等工艺中。这种高质量的表面处理不仅提高了零件的外观质量,也减少了后续表面处理的工作量。 - 模具寿命长
压铸模具通常由高质量的钢制成,具有优良的耐高温和耐高压性能。这些坚韧的钢材使得模具能够承受长时间的使用,具有较长的使用寿命,减少了模具更换频率和长期生产的维护成本。
压铸的缺点
- 仅适用于有色金属
压铸工艺主要适用于有色金属,如铝、锌和镁等。这些金属的熔点适中,易于在高压下注入模具。然而,对于熔点较高的黑色金属(如钢和铁),压铸并不适用。钢铁等金属需要特殊设备和更复杂的工艺才能进行铸造,这使得压铸的应用范围受到一定限制。 - 模具成本高
压铸模具的制造成本较高,尤其是在采用数控加工时,模具的制作过程复杂且成本较大。特别是当制造复杂零件时,使用高质量钢材的模具将进一步推高成本。虽然压铸工艺适合大批量生产,但对于小批量或复杂零件,其模具成本可能成为限制因素。 - 对缺陷的敏感性
压铸零件在生产过程中可能出现孔隙、收缩、气孔等缺陷,尤其是在高压铸造时,这些缺陷更为常见。例如,在铸造过程中空气滞留可能导致零件表面气孔的产生,这些气孔在热处理过程中可能会形成气泡,影响零件的质量。为了解决这些缺陷,可能需要额外的表面精加工步骤,从而增加了生产成本。 - 不适合小规模生产
尽管压铸适用于大批量生产,但其初始投资较高,尤其是模具制造、设备设置等固定成本较大。因此,压铸工艺通常不适合小规模生产或一次性零件生产。对于小批量生产,其他工艺(如注塑或CNC加工)可能更加合适,能够降低成本和生产周期。
贺鑫金属材料在压铸中的应用
压铸工艺使用的金属材料通常是有色金属合金,如铝、镁、锌等。这些合金具有不同的性能特征,适用于不同的应用需求。以下表格对常见的压铸合金进行了详细比较,列出了它们的主要成分、熔点、特性以及典型应用。
合金 | 常见亚型 | 主要成分 | 熔点 (°C) | 主要特性 | 典型应用 |
---|---|---|---|---|---|
铝合金 | A380, A360, A390, A413, ADC12 | 铝 (Al)、铜 (Cu)、硅 (Si)、镁 (Mg) | 577 - 660 | 重量轻、耐腐蚀、强度高、可加工性好,性价比高。 | 汽车(发动机部件、车轮、底盘)、航空航天(结构件、外壳)、电子(外壳、机身) |
镁合金 | AZ91D, AM60B, AS41B | 镁 (Mg)、铝 (Al)、锌 (Zn) | 632 - 650 | 极轻,铸造性好,适合重量敏感的应用,优良的铸造性能。 | 航空航天(机体结构、内饰件)、汽车(轻量化部件)、电子(手持设备、手机外壳) |
锌合金 | 锌合金#2、#3、#5、#7、ZA8、ZA27 | 锌 (Zn)、铝 (Al)、铜 (Cu)、镁 (Mg) | 381 - 419 | 铸造性极佳,熔点低,适合复杂设计,性价比高。 | 电子(连接器、外壳)、五金(锁具、按钮)、玩具和汽车零部件(装饰部件、齿轮) |
铜合金 | 黄铜(如C85700)、青铜(如C93200) | 铜 (Cu)、锌 (Zn)(黄铜);铜 (Cu)、锡 (Sn)(青铜) | 900 - 1083 | 强度高,导电性和耐腐蚀性优异,耐用。 | 管道(耐腐蚀水管、气管)、电连接器(接线端子、电接点)、船舶部件(耐腐蚀部件)、轴承 |
锡合金 | – | 锡(Sn)(90%)、铜(Cu)(2.5%)、铅(Pb)(7.5%)、锑(Sb) | 170 - 230 | 熔点低,流动性好,耐腐蚀,易铸造。 | 装饰品(珠宝、手工艺品)、小雕像、纪念品 |
铅合金 | – | 铅 (Pb)、锡 (Sn) | 183 - 327 | 熔点低,柔软,耐腐蚀性好,适用于辐射屏蔽。 | 辐射屏蔽(医疗设备、核设施)、电池(逐步被替代) |
锡基合金 | – | 锡 (Sn)、铜 (Cu)、锑 (Sb) | 232 | 低熔点,良好的铸造性能,耐腐蚀性好。 | 电子元件(焊接材料、电子零件)、珠宝、特殊应用(小型零件、精细饰品) |
压铸与其他制造工艺的比较
压铸与其他制造工艺(如注塑、锻造、冲压等)常常被混淆,尤其是对于制造业新手来说。尽管它们有相似之处,但每种工艺都有其独特的优点和适用领域。以下是压铸与注塑、锻造等常见工艺的比较,帮助了解它们之间的区别和适用场景:
压铸与注塑的区别
压铸和注塑是两种流行的成型工艺,它们都使用注射原理,适用于制造复杂细节和具有优良表面光洁度的零件。然而,它们的适用材料和工艺流程有所不同。以下是两者之间的主要差异:
差异 | 压铸 | 注塑 |
---|---|---|
流程 | 在压力下将熔融金属注入预先设计的钢模具中 | 在压力下将熔融塑料注入预先设计的钢或铝模具中 |
材料 | 有色金属合金(如铝、锌、镁) | 热塑性或热固性塑料 |
模具材料 | 钢 | 钢或铝 |
冷却时间 | 较长的冷却时间 | 较短的冷却时间 |
生产速度 | 相对较慢 | 较快 |
加工成本 | 模具成本较高(使用钢模具) | 模具成本较低(使用铝模具) |
零件成本 | 较高(由于生产时间较长) | 较低(生产时间较快) |
压铸与锻造的区别
锻造和压铸的主要区别在于它们的成型方式。锻造是通过施加压缩力使金属在固态下成型,而压铸则是将熔融金属注入预先设计的模具中。两种工艺在适用材料、生产速度和零件性能方面也有所不同:
差异 | 锻造 | 压铸 |
---|---|---|
流程 | 施加压缩力使加热的金属成型 | 在压力下将熔融金属注入模具中 |
材料 | 适用于黑色金属和有色金属,如钢、铝 | 适用于有色金属,如铝、锌、镁 |
成型材料 | 不需要模具,但使用模具来优化形状 | 必须使用模具 |
生产速度 | 较慢 | 较快 |
公差控制 | 中等耐受性 | 高精度公差控制 |
最终零件属性 | 提高机械性能 | 机械性能取决于铸造材料 |
压铸与冲压的区别
冲压是通过压力机将金属片材冲压成型的一种工艺,适用于大批量生产薄壁零件。与压铸相比,冲压的成型材料和工艺流程有所不同,尤其在适用零件的复杂性和生产效率方面:
差异 | 压铸 | 冲压 |
---|---|---|
流程 | 将熔融金属注入模具中成型 | 使用模具将金属片材通过冲压形成零件 |
材料 | 主要为有色金属合金(如铝、锌) | 适用于各种金属板材(如钢、铝) |
模具材料 | 钢 | 钢 |
零件形状 | 适用于复杂形状的零件 | 适用于薄壁零件和简单形状 |
生产速度 | 较慢 | 较快 |
精度 | 高精度 | 精度较低 |
压铸与3D打印的区别
3D打印是一种基于增材制造的工艺,通过逐层叠加材料来制造零件。相比于压铸,3D打印具有更大的灵活性和更快的原型制作能力,但在生产速度和零件性能方面有所不同:
差异 | 压铸 | 3D打印 |
---|---|---|
流程 | 将熔融金属注入模具中成型 | 根据数字模型逐层打印材料 |
材料 | 有色金属合金(如铝、锌) | 热塑性塑料、金属粉末等 |
模具材料 | 钢 | 无需模具 |
生产速度 | 较慢 | 较快 |
精度 | 高精度 | 精度适中 |
应用 | 批量生产复杂零件 | 快速原型制作、低批量生产 |
常见压铸材料与选择
铝、锌、镁等合金是常见的压铸材料,它们各有独特的性能,适用于不同的应用场景。以下是几种常见合金的特点:
- 铝合金:重量轻、耐腐蚀、易加工,广泛用于汽车、航空航天和电子领域。
- 镁合金:非常轻,适用于对重量要求严格的应用,如航空航天和消费电子。
- 锌合金:熔点低,铸造性优良,常用于电子产品、五金和玩具零件。
- 铜合金:具有高强度和良好的导电性,适用于电气连接器和船舶部件。
设计与制造优化
压铸设计不仅仅依赖于材料选择,还需要考虑零件的几何形状、拔模角、圆角半径等因素,以提高零件的性能、可制造性和成本效益。例如,适当的拔模角可以有效防止零件粘模,减少损坏风险;合理的圆角半径有助于均匀分布应力,避免应力集中。
结论
压铸工艺凭借其高精度、大批量生产的能力,已成为现代制造业中不可或缺的技术。无论是汽车零件、电子外壳,还是航空航天部件,压铸技术都为创新和卓越设计提供了坚实基础。随着材料和工艺的不断进步,压铸将在未来继续为各行各业带来更高效、更高质量的解决方案。
压铸常见问题与应对策略
压铸件为何容易出现气孔?
气孔通常是由于金属在注射过程中未能完全排气,或模具设计存在缺陷(如排气系统不良)所致。应对策略包括优化模具排气设计、调整注射速度和压力,以及使用更高效的排气系统。
为什么压铸件表面可能出现瑕疵?
表面瑕疵如气泡、褶皱和划痕多由模具表面不平整或金属流动不均引起。为避免此类问题,应定期检查模具表面光洁度,确保注射温度和流速的稳定。
压铸件出现缩孔是怎么回事?
缩孔是由于铸件冷却时金属收缩未能补充填充物,常出现在大件或复杂形状的压铸件中。通过优化模具设计、提高浇注系统效率及调整冷却速度,可以有效避免缩孔。
压铸件是否容易出现裂纹?
裂纹通常发生在金属流动不均或冷却过快时,可能由于注射压力过大或模具设计不合理造成。通过控制注射速度、温度和压力,以及使用高强度材料,可减少裂纹发生。
压铸件的尺寸不稳定怎么办?
尺寸不稳定可能是由于模具磨损、注射压力不稳定或温度控制不当。定期检修和保养模具,保持稳定的注射条件,以及对温控系统进行精细调整,能有效解决尺寸不稳定的问题。
模具磨损如何影响压铸质量?
模具磨损会导致产品精度下降,甚至影响铸件的外观和性能。为了应对模具磨损问题,应定期检查和更换模具,使用耐磨材料,并优化模具的设计和工艺。
压铸件为什么容易变形?
变形通常是由于冷却不均或模具设计不合理所致,尤其在铸件较大或结构复杂时。通过调整冷却系统和优化模具设计,可减少变形的风险。
如何减少冷隔现象?
冷隔是由于金属在注入模具时未能完全融合而形成的分层缺陷。为防止冷隔,需优化注射速度和温度,确保金属流动顺畅,并合理设计浇注系统和流道。
压铸件的后加工是否必要?
压铸件的后加工需求取决于零件的设计要求和表面质量标准。有些零件需要额外的加工,如磨削、钻孔或去毛刺,以满足严格的公差和表面光洁度。