铸造与机械加工:我们该如何选择?
发布时间:2025-03-19 分类:新闻 浏览量:581
作为宁波贺鑫铸造技术团队的核心成员,我在高压铸造、低压铸造、重力铸造 及铝材料领域深耕20余年,主导过数百个工业级项目的工艺开发。每当客户提出“铸造与机械加工如何选择”的疑问时,我的回答始终是:“没有绝对优劣,只有最适配场景的技术组合。” 以下从技术原理、实战经验与行业趋势三个维度,深度剖析两者的核心差异与选择逻辑。
什么是铸造?
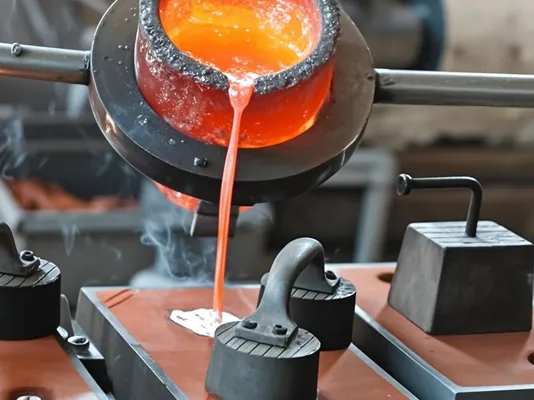
铸造是熔炼金属,制造铸型,并将熔融金属浇入铸型,凝固后获得一定形状与性能铸件的成形方法。 铸造与其他零件成形工艺相比,具有生产成本低、工艺灵活性大、几乎不受零件尺寸大小及形状结构复杂程度的限制等特点。
铸造技术作为人类文明的重要推手,其发展史可追溯至公元前4000年的古欧洲,保加利亚瓦尔纳遗址出土的黄金铸件揭示了早期金属铸造的雏形。同期,美索不达米亚的工匠已用铜合金铸造工具,而中国夏商时期的青铜礼器更以分铸法展现了东方铸造智慧,比欧洲早千年突破铁器铸造技术。跨文明的技术交流推动工艺迭代:埃及失蜡法塑造精美雕像,中国宋代《天工开物》系统记载泥范铸造,伊斯兰世界则将铸造融入精密仪器制造。
18世纪工业革命成为铸造史的转折点,焦炭炼铁法与蒸汽动力压铸机的结合,使铸铁件实现规模化生产,支撑起铁路、纺织机械等工业体系的构建。现代铸造更迈向高科技领域,20世纪铝镁合金压铸助推航空业发展,3D打印砂型技术打破传统工艺局限。如今全球铸件年产量超1亿吨,覆盖汽车、能源、医疗等关键领域。中国作为铸造发源地之一,现以全球40%以上产量稳居产业龙头,并通过绿色智能铸造技术持续引领革新。这项跨越八千年的技艺,正以数字化与可持续理念重塑现代制造业根基。
铸造是如何进行的?
铸造是通过将熔融金属注入特定模具型腔,待其冷却凝固后获得预定形状的工业技术。其核心流程分为五大阶段:首先根据零件结构设计可分离的模具,传统砂型铸造采用石英砂与粘结剂制作带有浇注系统的型腔,而精密铸造则使用陶瓷壳或蜡模;接着在高温炉中将金属原料熔炼至液态,铝合金 需加热至700°C以上,铸铁则需达到1400-1500°C,并添加合金元素调整性能。浇注阶段需精准控制金属流速和温度,避免产生气孔或冷隔缺陷,现代真空压铸技术通过负压环境提升充型完整性。
凝固过程决定铸件内部质量,工程师通过冷却系统设计调控晶粒生长方向,船用柴油机缸体等大型铸件常采用顺序凝固技术消除缩孔。脱模后需进行清砂、切割浇冒口等处理,数控机床对关键部位进行精密加工,航空航天部件还需X射线探伤检测内部缺陷。当代铸造已融合数字化创新,3D打印砂型技术可将复杂油路通道直接成型,仿真软件能提前预测金属流动轨迹,而绿色铸造则通过旧砂再生系统将废弃物利用率提升至95%,彰显智能制造与可持续发展的深度融合。
铸造的优点
适用于复杂部件:通过模具设计可成型带有空心结构、曲面或不规则轮廓的金属零件,解决其他工艺难以实现的几何复杂性。
材料兼容性广:能够加工多种金属及合金,包括回收废料或低纯度原料,仅需确保熔炼温度与模具耐热性匹配。
规模化成本优势:模具一次性投入后,可重复生产大量相同铸件,单件成本随批量增加显著降低。
尺寸适应性强:砂型铸造支持大型构件制造,而压铸等技术则适用于中小型精密零件成型。
多材料集成能力:通过在模具中预置金属或非金属嵌件,直接铸造出复合结构件(如强化衬套)。
铸造的缺点
内部缺陷风险:工艺参数波动或材料问题易导致气孔、缩松、冷隔等缺陷,需严格质量控制。
人力依赖度高:传统铸造流程涉及模具准备、浇注、清理等多环节人工操作,自动化程度较低。
环境负担:熔炼金属释放有害气体与粉尘,废砂、废渣处理不当可能污染环境,需配备环保设施。
什么是机加工?
机加工(机械加工)是通过物理切削方式对金属、塑料等材料进行精密成型的核心技术,广泛应用于现代制造业的关键环节。该工艺利用车床、铣床、数控机床等设备,配合钻头、刀具或砂轮,以毫米级甚至微米级精度去除材料余量,将毛坯转化为符合设计要求的零件。在汽车制造中,发动机缸体的曲轴孔需经多道车削与镗孔工序确保同心度;航空航天领域则依赖五轴数控机床切削出钛合金框架的复杂曲面,公差可控制在±0.005mm以内。相较于铸造或3D打印,机加工能实现更高的表面光洁度,精密磨削可使轴承滚道达到Ra0.1μm的镜面效果,同时可加工淬火钢等超硬材料。但传统切削会产生30%的材料损耗,近年来绿色加工技术通过微量润滑和高速切削将效率提升40%,而智能数控系统更可自动优化刀具路径,降低能耗与成本。从医疗器械的微型骨钉到风力发电机的主轴,机加工以“减法制造”的精准特性,持续支撑着高端装备与精密器件的工业化生产需求。
机加工的优点
高精准度:通过多轴数控技术可实现微米级精度控制,尤其适用于涡轮叶片、医疗植入体等对尺寸要求严苛的复杂零件。
快速响应小批量需求:无需复杂模具开发,直接根据设计文件加工,显著缩短原型验证和小规模生产的周期。
稳定重复性:依托数控程序与标准化刀具路径,确保批量生产中零件尺寸、表面质量的一致性。
自动化生产:数控系统实现全流程自动化,减少人工干预,降低操作误差并提升设备连续作业效率。
材料适应性广:兼容金属、工程塑料、陶瓷及复合材料,满足不同行业对材料性能的多样化需求。
机加工的缺点
内部结构加工受限:深孔、内腔等复杂内部特征需多次换刀或定制工具,加工难度与成本显著增加。
尺寸受设备约束:受机床行程与主轴刚性限制,超大型或超重工件难以实现整体精密加工。
资源利用率低:切削工艺产生大量金属屑或粉尘,原材料损耗率高于增材制造或近净成型工艺。
机械加工与铸造:类型和技术
加工类型
铣削:利用旋转多刃刀具沿多轴方向切削工件,适用于加工平面、曲面及复杂三维结构,广泛应用于模具型腔、异形零件制造。
车削:通过工件旋转与刀具直线进给的配合,高效成型回转体零件(如轴类、盘套类),可完成外圆、内孔及螺纹加工。
钻削:采用螺旋钻头旋转穿透材料形成圆孔,支持通孔、盲孔及台阶孔加工,常用于零部件装配定位孔的批量制作。
磨削:以高速旋转的砂轮对工件表面进行微量切削,提升尺寸精度与光洁度,适用于刀具刃口修磨、高精度轴承滚道加工。
镗削:通过单刃镗刀扩大预钻孔的内径,精准控制孔的同轴度与圆柱度,多用于发动机缸体、液压阀体等精密内腔加工。
拉削:使用带多级齿形的拉刀一次性成型键槽、花键或异形内孔,效率高且表面质量稳定,适合齿轮、联轴器的批量生产。
线切割:通过电蚀原理切割导电材料,可加工超硬金属的复杂轮廓,尤其适用于精密冲模、航天发动机叶片成型。
刨削:刀具直线往复运动切削平面或沟槽,适用于大型机床导轨、基础板的平面加工,操作简单但效率较低。
电火花加工:利用脉冲放电腐蚀导电材料,可加工微细孔、复杂型腔及硬质合金模具,突破传统切削的硬度限制。
每种工艺根据刀具特性、运动轨迹与材料适应性组合应用,共同覆盖从粗加工到超精加工的全产业链需求。
铸造类型
砂型铸造:利用硅砂、黏土或树脂粘结剂制作一次性或半永久性铸型,通过模型压印形成型腔,适用于铸铁、铸钢等高熔点金属的多样化生产,常见于发动机缸体、阀门等结构件制造。
压铸:将熔融金属高速压入高强度钢制模具,快速冷却成型,专精于铝、锌、镁等有色金属的精密薄壁件量产,广泛应用于汽车部件、电子外壳等表面光洁度要求高的产品。
熔模铸造:以蜡模替代实体模型,包裹多层耐火涂料形成陶瓷型壳,熔失蜡模后注入金属液,可复制涡轮叶片、艺术品等复杂精细结构,尤其适合航空航天领域的高温合金件小批量定制。
离心铸造:借助离心力使金属液均匀贴附旋转模具内壁,成型无缝管材、轮毂等回转对称部件,兼具材料致密性与生产效率,多用于管道、轴承套圈的生产。
低压铸造:通过气压将金属液平稳注入密闭模具,减少湍流与氧化,成型铝轮毂、气缸盖等致密性要求高的中空件,兼具工艺稳定性与材料利用率优势。
消失模铸造:采用泡沫塑料模型替代传统模具,浇注时模型气化并由金属液填充,可一体化成型带复杂内腔的铸件,适用于矿山机械、泵阀壳体等单件或小批量生产。
连续铸造:金属液通过水冷结晶器连续凝固并拉坯,直接生产棒材、板材或型材,大幅提升钢铁、铜合金等材料的成型效率,成为冶金行业规模化生产的核心工艺。
每种铸造技术根据模具特性、金属流动性及生产需求匹配应用,形成从艺术铸件到工业构件的全领域制造能力。
机械加工与铸造的主要区别
工装特性
机械加工依赖铣刀、钻头、车刀等切削工具直接成型零件,而铸造需通过模型制作、模具制备等前期工艺构建成型空间,工具链覆盖从蜡模雕刻到砂型制备的全流程。
精度控制
机械加工通过数控系统实现微米级精度,尤其擅长高表面光洁度与复杂几何细节;铸造件受模具精度、金属收缩等因素影响,需借助精密压铸或熔模工艺提升尺寸一致性。
材料兼容性
铸造材料受限于熔点与流动性,砂型铸造适配铸铁、铸钢等高熔点金属,压铸聚焦铝、锌等低熔点合金;机械加工可处理金属、工程塑料、陶瓷等多元化材料,硬度范围更广。
设计复杂度
机械加工擅长锋利边缘、薄壁结构及精密孔槽的成型,但对深腔、内弯等封闭结构存在加工盲区;铸造可一体成型带内部空腔、曲面流线的复杂部件(如发动机缸体),但细节锐度较低。
生产规模适配
铸造在大批量生产中具备成本优势,模具一次性投入后可快速复制;机械加工无需模具,通过程序调整即可响应小批量或单件定制需求,灵活性强。
零件性能
机械加工件因无凝固缺陷,力学性能更均匀;铸造件通过定向凝固、热处理等工艺优化晶粒结构,可接近原材料强度,但内部可能存显微气孔或夹杂。
原型开发效率
机械加工基于CAD模型直接切削,数小时内完成原型试制;铸造原型需经历模具开发与金属浇注,周期较长,但熔模铸造可通过3D打印蜡模加速流程。
综合成本结构
铸造前期模具成本高,适合规模化摊薄单件成本;机械加工无模具费用,材料损耗与工时成本随批量线性上升,更适配中小规模或高附加值产品。
两类工艺在制造业中形成互补:铸造解决复杂构件的批量成型,机械加工实现精密特征的最终修正,共同支撑从毛坯到成品的完整制造链路。
铸造和机械加工用在哪些地方?
行业分类 | 铸造典型应用 | 机械加工典型应用 |
---|---|---|
汽车制造 | 发动机缸体、变速箱壳体、轮毂、悬挂支架 | 变速齿轮、活塞环、曲轴轴颈、制动卡钳 |
航空航天 | 涡轮机匣、发动机叶片、起落架结构件 | 钛合金框架、燃油喷嘴、飞行控制精密零件 |
医疗器械 | 医疗床架基座、影像设备外壳 | 人工关节、手术器械、微型植入物(如骨钉) |
能源电力 | 风力发电机舱罩、核反应堆压力容器 | 涡轮机叶片榫槽、液压阀芯、输电连接件 |
工业装备 | 阀门壳体、泵体、重型机械底座 | 高精度轴承、丝杠、模具镶块、自动化机械臂 |
电子通信 | 5G基站散热器、铝合金外壳(压铸) | 射频连接器、芯片散热片、微型传感器外壳 |
轨道交通 | 火车制动盘毛坯、轨道扣件 | 轮对加工、转向架精密衬套、信号系统零件 |
船舶制造 | 螺旋桨铸件、船用柴油机缸套 | 推进轴系、舵机精密齿轮、液压管路接头 |
家用消费品 | 铸铁锅具、门锁主体、卫浴五金件 | 智能家电齿轮、精密铰链、电子产品金属边框 |
建筑与基建 | 市政井盖、钢结构连接节点、桥梁支座 | 建筑模板紧固件、电梯导轨、抗震支撑配件 |
工艺适配逻辑:
- 铸造侧重复杂一体成型:如带内腔的发动机缸体、薄壁压铸电子外壳、耐高压阀门等;
- 机械加工聚焦精密功能部件:如高转速轴承滚道、微米级医疗植入物、航空燃油精密流道等。
两类工艺常协同使用——铸造提供近净形毛坯,机加工完成关键部位精修,共同实现高性能终端产品。
我该选择哪一个?机械加工还是铸造
在决定制造项目采用机械加工还是铸造时,需基于设计特性、生产目标及资源条件综合评估。以下是关键决策维度的深度解析,帮助您精准匹配工艺与需求。
1. 生产规模与扩展性
- 选择铸造:若项目需要长期、稳定的大批量生产(如汽车零部件、家电结构件),铸造工艺的单件成本随产量增加显著降低。模具的重复利用特性使其在规模化生产中具备天然优势,尤其适合标准化产品的快速复制。
- 选择机械加工:对于小批量定制化需求(如原型验证、航空航天专用件)或需要频繁迭代设计的产品,机械加工无需高昂的模具投入,可快速响应订单变化,灵活适配中小批量生产。
2. 零件结构复杂度
- 选择铸造:若零件包含内部空腔、薄壁结构、多向流道等复杂几何特征(如发动机缸体、液压阀体),铸造可通过模具型腔一次性成型,避免机械加工的多工序耗时难题。
- 选择机械加工:若设计侧重外部精密轮廓、微孔阵列或超精细表面(如光学器件基座、医疗植入物),机械加工的切削精度能实现复杂曲面的毫米级控制,尤其适合开放型结构的深度雕琢。
3. 精度与一致性需求
- 选择铸造:铸造件的尺寸精度通常依赖模具质量与工艺控制,适合中等精度要求的场景(如管道连接件、装饰性构件)。对于高精度配合面,可通过“铸造+局部精加工”的混合工艺降低成本。
- 选择机械加工:若零件需满足微米级公差或严格的装配匹配(如精密齿轮、半导体设备腔体),机械加工凭借数字化编程与高刚性设备,能稳定输出一致性极高的成品。
4. 材料特性与兼容性
- 选择铸造:适用于铝合金、锌合金、铸铁等流动性良好的金属。对于再生材料(如回收铝锭),铸造工艺能高效熔炼并重塑,显著提升资源利用率。
- 选择机械加工:兼容更广泛的材料类型,包括高硬度合金(钛合金、淬火钢)、非金属(工程塑料、陶瓷)及复合材料。尤其适合加工难以熔融成型或对热敏感的材料。
5. 材料利用率与可持续性
- 选择铸造:近净成形技术可最大限度减少材料浪费,尤其适合贵重或稀缺金属的加工。再生铝铸造的碳排放强度仅为新铝材加工的1/3,符合绿色制造趋势。
- 选择机械加工:切削过程中产生的碎屑与边角料可能占原材料重量的较大比例,需配套废料回收系统以降低环境成本。
6. 生产速度与交付周期
- 选择铸造:模具开发阶段需一定时间,但量产启动后效率极高,适合长周期、稳定输出的项目。
- 选择机械加工:从图纸到成品的周期短,适合紧急订单或快速迭代的原型开发,尤其受益于数字化制造的敏捷性。
7. 成本结构对比
- 铸造的核心成本项:模具设计与制造费用占初期投入的绝大部分,适合产量摊薄成本的场景。
- 机械加工的核心成本项:设备折旧、刀具损耗及人工编程成本占主导,适合小批量高附加值产品。
8. 混合工艺的创新实践
对于多数工业场景,单一工艺往往无法满足所有需求。推荐策略:
- 铸造+精加工:利用铸造实现复杂主体结构,再对关键配合面进行数控精修(如汽车变速箱壳体);
- 增材制造+切削:3D打印近净形毛坯,减少机加工余量(如航空航天异形支架)。
总结:动态权衡,精准决策
- 优先选择铸造的场景:大批量、复杂内腔结构、材料成本敏感、绿色制造导向;
- 优先选择机械加工的场景:小批量、高精度需求、硬质材料加工、快速交付压力;
- 混合工艺的黄金组合:平衡效率与精度,实现成本与性能的最优解。
在宁波贺鑫的实战经验中,成功案例往往源于对上述维度的动态评估。建议企业建立多部门协同的工艺评审机制,必要时引入第三方技术咨询,确保每个项目的工艺选择科学、经济、可持续。
常见问题
Q1:如何根据生产需求选择铸造或机械加工?
选择工艺需权衡生产批量、零件复杂度、材料特性和精度要求——铸造适合大批量复杂结构件(如发动机缸体),可成型内腔但精度受限;机加工适配小批量高精度需求(如精密齿轮),能处理多样化材料但效率随复杂度降低。
Q2:哪种工艺更经济高效?
铸造前期模具成本高但单件成本随量递减,适合规模化生产(如百万件电子外壳);机加工无模具投入,适合中小批量定制(如航空零件),但材料损耗推高成本,新兴技术如3D打印砂型正打破传统成本边界。
Q3:材料选择如何影响工艺决策?
铸造受限于金属流动性(如铝压铸)和熔点(如铸铁砂铸),而机加工可切削超硬合金(如钛合金)和工程塑料,但对脆性材料(如陶瓷)易产生崩裂,需特殊刀具和工艺。
Q4:如何处理高度复杂的零件?
铸造通过熔模技术一体成型复杂内腔(如涡轮叶片),机加工用五轴数控切削精密曲面(如叶轮),但封闭结构需组合工艺:铸造毛坯+机加工精修(如缸体镗孔),实现功能与成本平衡。
Q5:哪种工艺更环保?
铸造面临高能耗熔炼和废砂处理难题,需旧砂再生系统;机加工需处理切削液污染和金属屑回收,但绿色技术(干切削、微量润滑)逐步降低环境影响,两者均需闭环生产优化。
Q6:是否需要结合两种工艺?
协同应用成常态:铸造提供近净形毛坯(如齿轮铸件),机加工完成高精度特征(如齿面磨削);增材制造+数控精修则突破传统局限,满足航天件等超复杂需求。
Q7:原型开发选哪种更快?
机加工凭CAD直切优势,数小时交付金属/塑料原型;铸造结合3D打印蜡模可将周期从数周缩至数天,适合需验证材料性能或结构强度的功能性原型。
核心逻辑:铸造重“成型效率”,机加工重“精度可控”,选型需围绕成本、时间、性能三维度,多数场景需两者互补而非替代。